Competency B2: Install Regulators, Valves, and Valve Train Components
Learning Task 1
Installing Manual Valves
Proper location of manual shut-off valves is critical to ensure a gas piping system can be shutoff for both emergencies and equipment maintenance. The gas code specifies particular locations that require the installations of manual shut-off valves.
To ensure that valves are working properly, they must suit the application and be correctly installed.
Code requirements
Most gas shut-off applications will require the use of a manual valve that will fully open or close with a quarter-turn of the handle. The gas codes identify specific locations and equipment that require the installation of manual shut-off valves. Here are some examples that are identified in the B149.1 gas installation code:
- Automatic fire extinguishing systems
- Pressure regulators
- Test ports
- Quick-disconnect devices
- Supply to underground plastic pipe
- Appliance shut-offs
- Multiple piping systems
- Multiple buildings served
- Multiple propane risers from underground main
- Classroom or lab master shut-offs
- Gas hoses
- Purging operations
- Emergency generators
- Construction heaters
Check the code index listings under “manual shut-off” to find the installation details of each requirement.
Manufacturers specifications
Not all valves are approved to be used in combustible gas applications. The W.O.G. pressure rating does not cover flammable gas such as Natural gas or Propane. Valves for gas service (Liquid Propane (LP) and or Natural Gas (NG) must be certified and bear the CSA mark along with the applicable marking for the type of gas application.
It is important to know the operating conditions when selecting a valve. Then check the valve markings to determine if the valve is appropriate for the application. Here is a brief description of each of the rating marks on the gas valves
½ PSI
- Signifies ½ psig rating for appliance manufactures’ use
- ANSI Z21.15 (USA) CGA 9.1 CAN
- “American National Standard/Canadian Gas Association Standard for Manually Operated Gas Valves For Appliances, Appliance Connector Valves and Hose Ends Valves”
- Temperature Range of 0°C to 51.5°C (32°F to 125°F)
- Intended to be used as part of a gas fired appliance
- Not for use in building piping systems
5G
- Signifies 5 psig rating for inline valves
- Standard 3.88 (USA) & CR91-002 (CAN)
- “Manually Operated Gas Valves For Use On Piping”
- CR91-002 Temperature range between −40°C to 52°C (−40°F to 125°F)
- Standard 3.88 Temperature range between 0°C to 51.5°C (32°F to 125°F)
BRS
- Signifies 125 psig rating for United States
- ASME B16.33 Standard
- “Manually Operated Metallic Gas Valves For Use in Gas Piping Systems Up to 125 psig sizes ½” to 2”
- Temperature range between −20°F to 150°F
CAN-3.16
- Signifies 125 psig rating for Canada for Outdoor Use
- CAN/CGA 3.16 Standard
- “Lever Operated Non-Lubricated Gas Shut-Off Valves”
- Suitable for continuous use over the temperature range of −30°C to 65°C (−22°F to 140°F)
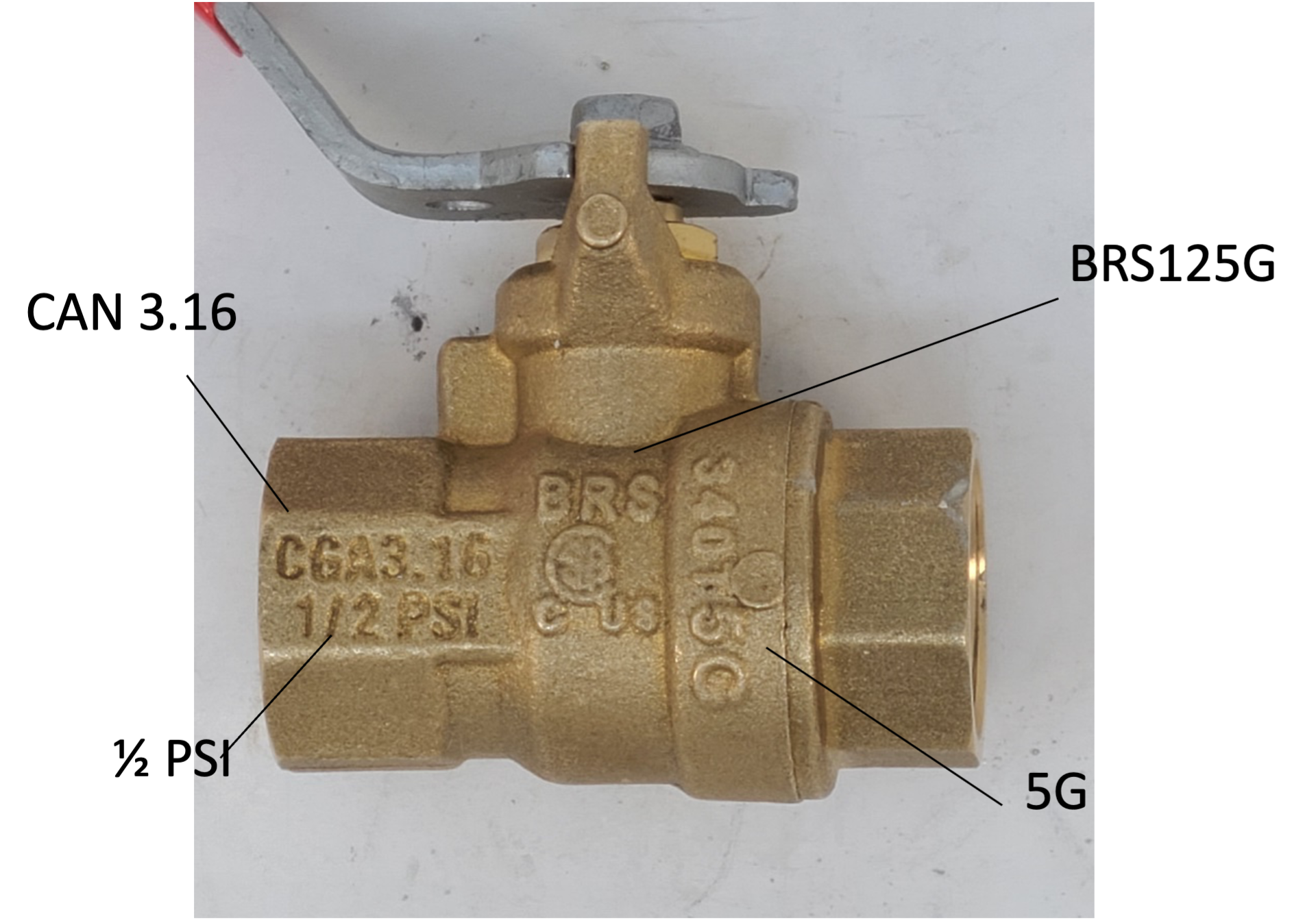
Having a 125 psi rating does not override the ½ PSI or 5G marks. Approval marks must be shown for the application. Valve with 5G rating are acceptable for use indoors and out in Canada. The ½ PSI valves are for indoor use.
Installation procedures
To ensure that valves are working properly, it is essential that they are correctly installed.
Here are some basic valve installation guidelines:
- Review that the valve fits its intended purpose. The valve should comply with the system design, pressure, and temperature requirements
- Before installation check that the valve body, seat, and ball are free from any damage caused by transportation or storage.
- After the installation is completed, it is recommended to operate the valve multiple times to ensure it is not defective and rotates through its entire 90-degree operation.
- Ball valves can also be installed in any orientation or angle, providing there is enough space to allow for 90-degree operation. Some fitters prefer to install the valve so the handle points in the direction of flow whenever possible. Another best practice is to install the valve in the fail-safe position (Figure 2). Fail safe means that the valve is installed so that should the packing become loose or the valve arm be unintentionally moved, the arm will move to the close position. Installation upside down is not recommended because it can cause dirt to accumulate by the stem packing.
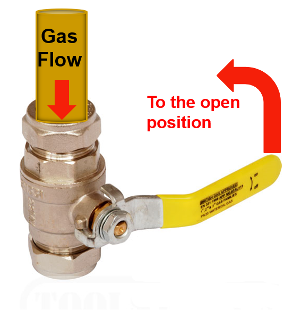
- When installing two-piece body ball valves always use two wrenches when making up pipe joints to these valves. Position one wrench on the valve end closest to the pipe joint being tightened and the other wrench onto the pipe to prevent transmitting torque through the valve body joints. This also prevents distortion of the internal parts of the valve.
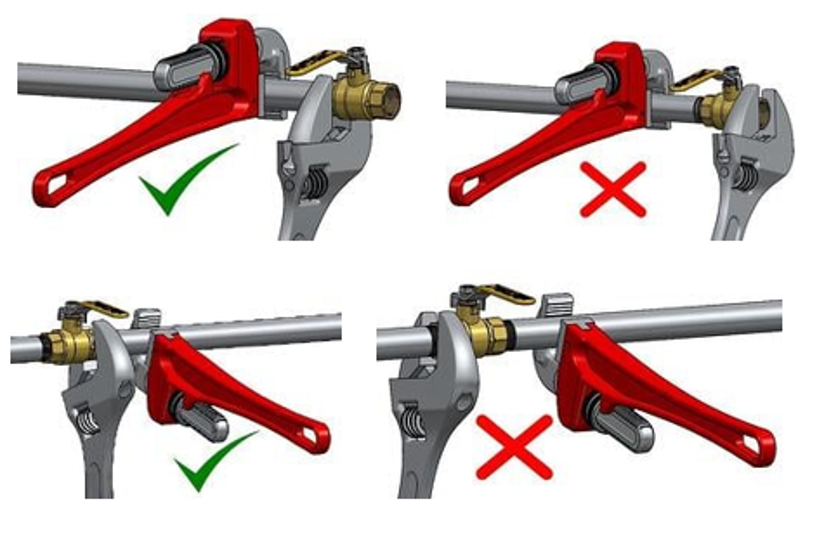
Maintenance
Other than cycling of the valve from open to closed position periodically, inspection and maintenance are not required on manual ball valves. Repair or replacement of two-piece ball valves’ internal parts is not recommended. Damage can occur to the body and tailpiece during disassembly that would make the valve inoperable.
Normal stem packing wear may cause a slow leak. If a minor leak is identified at the valve stem remove the handle and tighten the packing nut in [latex]\frac{1}{8}[/latex] increments until a soap test verifies the leakage has stopped (Figure 4). Over tightening will increase the torque required to operate the valve and result in excessive wear on the packing.
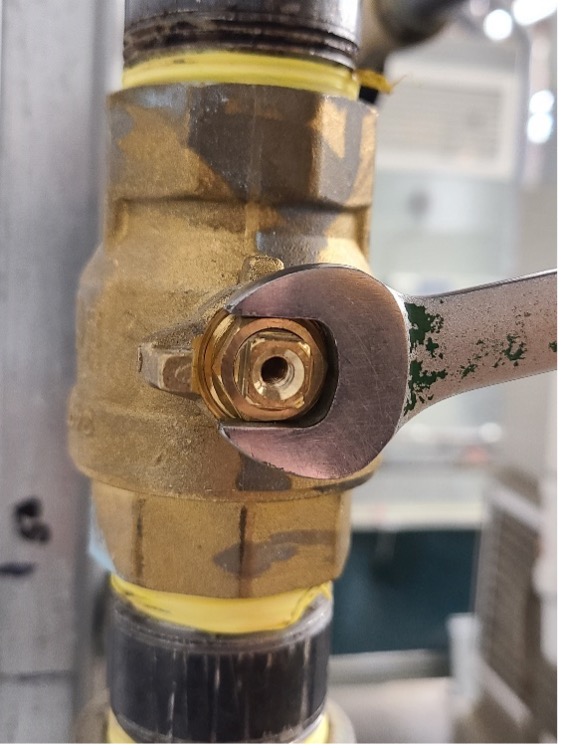
Lubricated plug valves usually only require relubrication once every few years unless they are exposed to a lot of heat or intense sunlight which liquifies the grease. If a faint gas odor is noticed at the gas valve it may need relubrication.
There are two common methods used to inject the approved lubricating sealant. One method is to use a high-pressure grease gun equipped with a button head coupler (figure 5). The button head grease fittings are a heavy-duty fitting distinguished by their flat low-profile appearance. By pulling onto the button head fitting, the couple slides over it to give a high pressure no leak engagement.
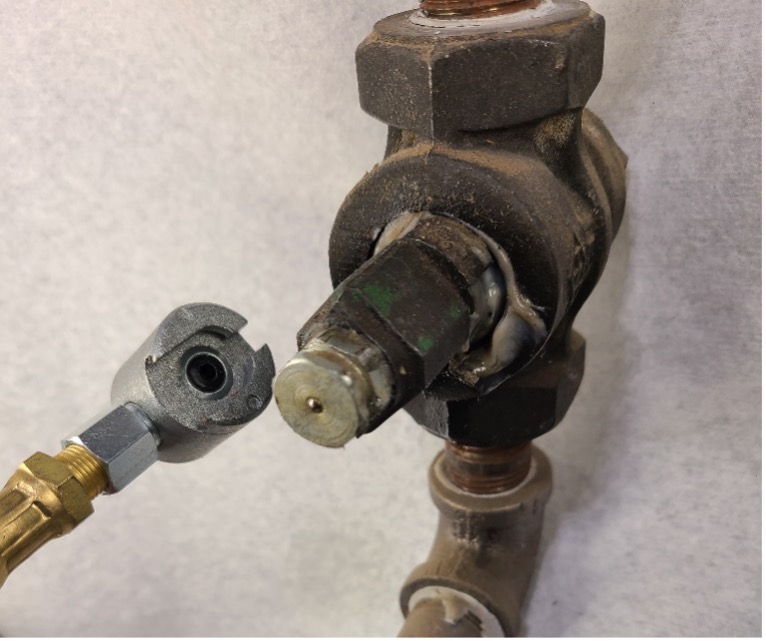
Another method of relubrication is to use screw injector tool. A small stick of lubricant is loaded into the tool (Figure 6). When the screw is wound in it exerts a powerful hydraulic force and injects the sealant into the valve.
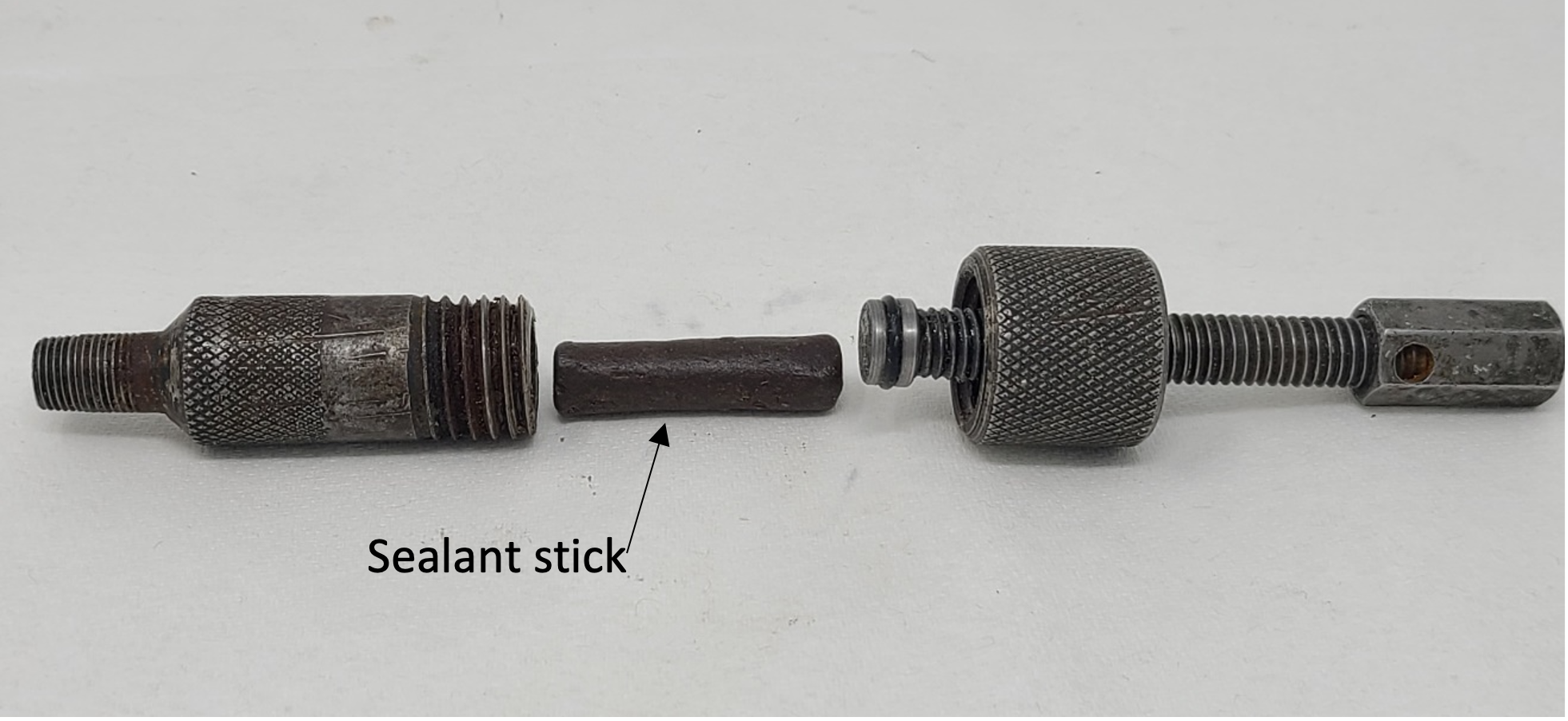
The screw injection tool shown in Figure 7 has had a hose added which makes it easier for the operator to use. Initially the hose will need to be purged with grease.
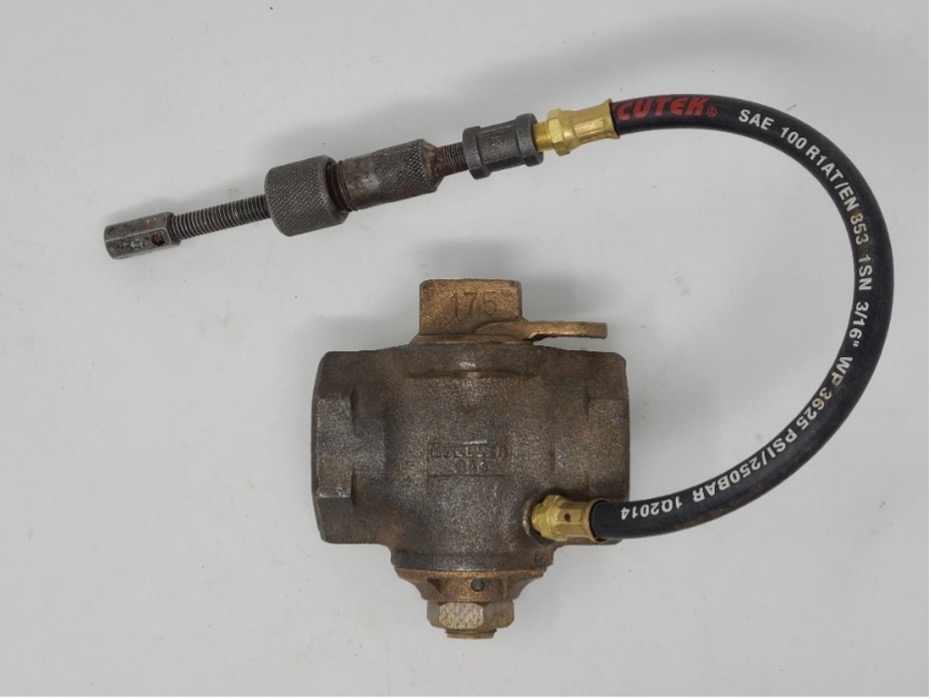
Another type of lubrication fitting is the combination button head/ screw fitting which enable the connection of the lubricating hand gun for the initial lubrication (Figure 8). Further relubrication can be done by screwing down the fitting with a wrench. When the fitting is finally turned into the valve as far as it will go, it indicates additional sealant should be added. The sealant fitting must be backed out a ways and sealant injected into the fitting’s reservoir, or remove the fitting and insert another stick of sealant.
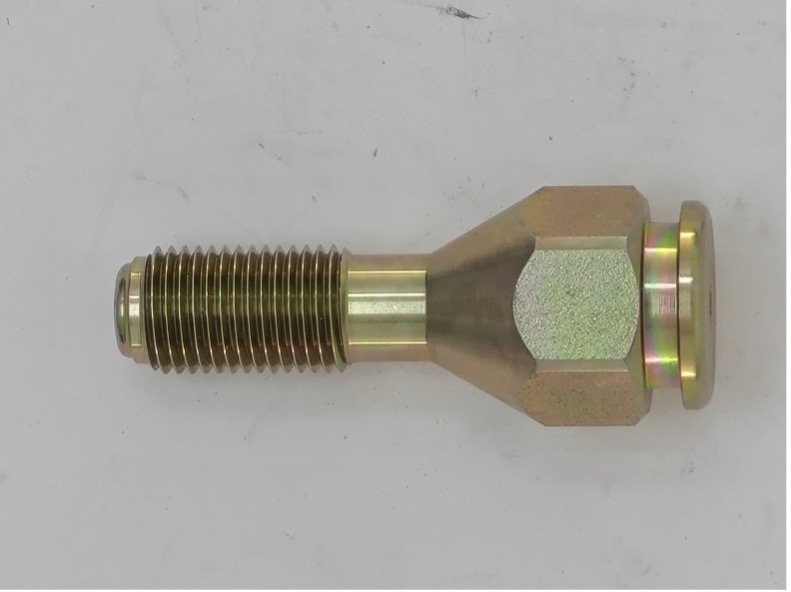
If it is OK to interrupt the gas flow, then turning the valve on and off while lubricating helps distribute the lubricant more evenly. Soap leak test the top and bottom plug seams as well as the lube port when finished.
Now complete Self-Test 1 and check your answers.
Self-Test 1
Self-Test 1
Media Attributions
- Figure 1. “Valve markings” by Rod Lidstone is licensed under a CC BY-NC-SA licence.
- Figure 2. “Ball valve fail safe position” by Camosun College is licensed under a CC BY-NC-SA licence.
- Figure 3. “Wrenching ball valves” from Boshart Industries is used for educational purposes under the basis of fair dealing.
- Figure 4. “Tightening ball valve packing nut” by Rod Lidstone is licensed under a CC BY-NC-SA licence.
- Figure 5. “Button head grease fitting and coupler” by Rod Lidstone is licensed under a CC BY-NC-SA licence.
- Figure 6. “Loading lubrication stick into screw injection tool” by Rod Lidstone is licensed under a CC BY-NC-SA licence.
- Figure 7. “Sealant screw injection tool with hose extension” by Rod Lidstone is licensed under a CC BY-NC-SA licence.
- Figure 8. “Combination giant buttonhead/lubescrew fitting” by Rod Lidstone is licensed under a CC BY-NC-SA licence.