Competency D1: Install Sewage Treatment Systems and Components
Learning Task 3
Describe a Private Sewage Treatment System Installation
As described in Competency D1, Learning Task 1, the installation of a residential sewage treatment system is a very structured and regulated process. More than one AP (authorized person) could be involved in the different phases of the installation, which are planning, installation and maintenance. This learning task will summarize the steps and processes involved in the installation of a private sewage treatment system for a single-family house with a Type 1 treatment method (septic tank and trickling gravity disposal field). The steps to be followed are similar for commercial or industrial buildings, with the major differences being the volume and strength of the sewage produced, and the dispersal method chosen.
Learning Objectives
After completing this learning task, you will be able to:
- Describe the process involved in determining daily design flow (DDS)
- Identify the terms used in describing system components
- Identify factors in the operation of tanks and disposal fields
- Describe considerations for choices of treatment and dispersal methods
Key Terms
- AIS: area of infiltrative surface
- AP: authorized person
- BOD or BOD5: 5-day biochemical oxygen demand
- DDS: daily design flow
- HAR: hydraulic application rate
- HLR: hydraulic loading rate
- HS: horizontal separation
- LLR: linear loading rate
- perc rate or perc: percolation rate
- POA: point of application
- ROWP: registered onsite wastewater practitioner
- SHWT: seasonal high water table
- SPM: sewerage system standard practice manual, version 3
- SSR: sewerage system regulation
- TSS: total suspended solids
- VS: vertical separation
Planning the Installation
The first step in any installation is for the certified planner to meet with the building owner. Information must be collected and recorded on official documents. The points below are considered minimum required information to be gathered:
- The full legal name of the owner(s), and contact information
- Legal description, civic address, and tax assessment roll number for the subject property
- Current or planned water source (i.e., an approved community water system, an on-site water well or freshwater body such as lake or creek)
- Current and planned uses of the property (i.e., residential only, commercial uses including home based business, or mixed commercial/residential)
- Current or planned size and use of non-residential buildings
- Current or planned water source (i.e., an approved community water system, an on-site water well or freshwater body such as lake or creek)
- Information regarding any wells located on the property, including well logs
- Current or planned residence information including:
- Living and non-living areas of the residence
- Number of bedrooms
- Anticipated number of occupants
- Water treatment devices (i.e., water softeners, filtration systems, disinfection, or similar devices)
- Garbage grinders/in-sink garbage disposal units
- Any other anticipated usage patterns that may affect sewage volume or constituents, which may include:
- Frequent large numbers of guests (i.e., from social events)
- Non-typical food processing such as canning, high volume of baking or deep frying, beer or wine making
- Home-based businesses with associated sewage discharges
- Hobbies with associated sewage discharges (e.g. photography, painting, pottery
- Information for the owner on their responsibilities under the SSR
- A signed declaration statement by the owner(s) including the following:
- Identification of ownership (who are the legal owners?)
- Confirm the accuracy of information provided
- Understanding that system use (including the design flow) is to be per the filing submitted to the Health Authority
The AP may choose to add a contract or simple letter of engagement to the declaration that specifies project roles, budget, etc. As well, the owner should be informed that any changes to the intended use or occupancy as attested to in the filing may drastically alter the performance and acceptance of the installation.
Determine the Daily Design Flow (DDF)
Once the obligatory information listed above has been collected and before a treatment method is chosen, the next step is to determine the suitability of the site for a conventional disposal field. To do this, an estimate of the daily design flow (DDF) must be made. Daily design flow is the estimated peak daily flow to be discharged and is synonymous with the SSR terms “estimated daily domestic sewage flow” and “daily design domestic sewage flow.”
There are two tables in the SPM to assist in determining the DDF, either of which can be consulted for determining the daily design flow from a residence.
Number of bedrooms | Maximum floor area (m2) | DDF litres/day |
---|---|---|
1 | 140 | 700 |
2 | 240 | 1000 |
3 | 280 | 1300 |
4 | 330 | 1600 |
5 | 420 | 1900 |
6 | 520 | 2200 |
Additional bedroom, add: | 300 | |
Additional m2, add: | 3 |
As an example of using Table II-8 above, a residence with three bedrooms and a floor area of 295 m2 would have an expected DDF of 1300 L.
Also, according to Table II-8 for a 3-bedroom home, for every m2 of house area over 280 m2, the DDF should be increased by 3 L. This would mean that the calculation would become:
[latex]1\;300\text{ L}+(15\times3=45\text{ L})=1\;345\text{ L}[/latex]
Adjustments to the table values are made wherever special circumstances are encountered, such as when garbage grinders or garburators are used. Vol. II- 5.1.3.2 of the SPM states “When garbage grinders (garburators) are used, increase the Daily Design Flow by a factor of at least 1.5.” This means that, if a garburator is used in our example, the DDF would be calculated to be:
[latex]1\;345\times1.5=2\;017.5\text{ L}[/latex]
Accordingly, the combination of the significant impact on the DDF and the negative effect rotting food can have on treatment, the use of garburators for septic systems is strongly discouraged.
Alternatively, Table II-9 can be used to determine the DDF on a per capita basis. We’ll use it instead of Table II-8 for our example and compare the two results.
Use | Per Person Flow (L/Day) |
---|---|
Single family dwelling | 350 |
Multi-family (apartment) | 300 |
Luxury homes | 700 |
Seasonal cottage | 250 |
Mobile home | 300 |
Number of bedrooms | Minimum number of occupants |
---|---|
1 | 2 |
2 | 3 |
3 | 3.75 |
4 | 4.5 |
5 | 5.5 |
6 | 6.5 |
According to Table II-9, a 3-bedroom home would have an expected minimum number of 3.75 occupants. Multiplying this by 350 L/day/person (from the top row of the table), the expected DDF would be:
[latex]350\times3.75=1\;312.5\text{ L}[/latex]
Again, if a garburator is used, this would be increased by a factor of 50% to be:
[latex]1\;312.5\times1.5=1\;968.75\text{ L}[/latex]
As you can see, regardless of any adjustments made because of the allowance for extra floor area, there is only a slight difference in DDF resulting from the use of either method.
For a luxury home, sewage flow per occupant (700 L/day) is higher than for an average home (350 L/day), as they often include the following:
- Larger overall floor area with larger rooms than an average home
- More water use appliances than an average home
- Large parties, frequent guest use, and the probability of domestic service workers adding to the DDF
Determine Site Conditions for Dispersal
Once the DDF is calculated, the next step in the planning process is to select the type of distribution allowed by the SPM. Factors in this step include:
- site capability standards, as found in Section II- 4.1.2
- vertical separation standards from Section II- 5.3, as well as
- the standards of Section II- 6 for the specific type of dispersal system
According to the SPM, the simplest distribution and dosing system which meets site capability should typically be considered first. Once again, for the purposes of explanation, we’ll focus on the use of a gravity trickling disposal field.
The SPM contains a great many definitions. Several of them that pertain to the explanations that follow are listed below.
Key Terms
- area of infiltrative surface (AIS): Infiltrative surface area, in m², receiving effluent from the distribution system. This is considered to be the bottom area of a trench in a trench-type gravity system.
- basal area: For sand mounds, sand-lined trenches, bottomless sand filters, Alberta At Grade systems and CTDS, this is the native soil that the sand will be placed on.
- blinding layer: A layer of clean coarse sand or mound sand that is installed between the infiltration surface (bottom of aggregate, base of chamber, etc.) and the native soil, and which is up to 10 cm (4 inches) thick.
- consistence: Attribute of soil expressed in degree of cohesion and adhesion, or in resistance to deformation or rupture.
- gravel: Rounded or subrounded rock fragment that is between 0.1 inches (2 millimetres) and 3 inches (76 millimetres) in diameter. Often called “drain rock.”
- hydraulic loading rate (HLR): A measure of the volume of effluent, in litres, applied each day, per unit area (m²) of infiltrative surface.
- infiltrative surface: In drainfields, the drain rock-to-original soil interface at the bottom of the trench; in mound systems, the gravel-to-mound sand and the sand-to-original soil interfaces; in sand-lined trenches/beds (sand filter), the gravel-to-sand interface and the sand-to-original soil interface at the bottom of the trench or bed.
- Kfs: A measurement of the saturated hydraulic conductivity of soil. In theoretical terms, hydraulic conductivity is a measure of how easily water can pass through soil or rock. High values indicate permeable material through which water can pass easily, such as sand or gravel; low values indicate that the material, such as clay, is less permeable.
- limiting layer: The shallowest of a restrictive layer, water table, seasonal high-water table or extremely permeable material (e.g., fractured rock, gravel).
- platy structure: Laminated or flaky soil aggregate developed predominantly along the horizontal axis.
- restrictive layer: A layer of soil or rock that impedes the vertical movement of water, air, and the growth of plant roots. This may include hardpan, some compacted soils, bedrock, glacial till and unstructured clay soils.
- soil horizon: Layers of soil or soil material approximately parallel to the land surface and different from adjacent layers in physical, chemical, and biological properties or characteristics such as colour, structure, texture, consistence, and pH.
- soil structure: The combination or arrangement of individual soil particles into definable aggregates, or peds, which are characterized and classified based on size, shape, and degree of grade (distinctness).
- soil texture: The relative proportions of the various soil separates (e.g., silt, clay, sand) in a soil.
- vertical separation in native soil: The depth of unsaturated, original, undisturbed permeable soil below the infiltrative surface and above any limiting layer. This is the vertical depth of soil that the dispersal system is expected to be discharged into.
Determining Soil Characteristics
The soil structure and consistency of the proposed dispersal field must be determined, and this can only be accomplished by performing a soil analysis. To do this, test holes must be dug, and the sides of the holes inspected. The procedure listed in III-3.3.2.1 “Test pits” (observation holes) includes the following points:
- Excavate a minimum of two test pits (observation holes). In some cases, two pits will not be enough to describe the soil conditions. If platy structure is found, site investigation should include a minimum of 4 observation test pits in the dispersal area and two in the receiving area to determine the extent and uniformity of the platy soil layer(s) more accurately. If soils are variable or the area is large, excavate additional test pits
- Augered (bored) holes can be used to investigate soil conditions. This may be preferred on some sites to minimize the number of test pits. A minimum of two observation test pits should be excavated to confirm the auger test results
- The test pit should be dug to a depth that provides the soil and water table information for designing the sewage system. In all cases test pit depth may be limited by refusal, i.e., rock or other layer which cannot readily be excavated. If feasible, considering the hardness of the ground, excavate to:
- A minimum of 1.2 m depth in total
- A minimum of 0.9 m below the proposed infiltrative surface
- A minimum of 1.5 m below the proposed infiltrative surface, if Volume II standards specify a larger vertical separation. This would apply, for example, in the case of gravity dispersal to gravelly sand soil (the standards specify a vertical separation of 150 cm)
- A minimum of 3 m overall depth and a minimum of 1.2 m below the planned base elevation, for a proposed BC zero discharge lagoon. If sand lenses or rock outcrops are suspected, consider investigation to greater depth
- A minimum of 1.2 m below the base of a proposed ETA bed.
In some cases, nearby water well logs, where available, can provide an indication of the water table elevation and soil conditions below the depth feasibly assessed by test pits. Water well logs are accessible through the BC Water Resources Atlas.
In British Columbia, “Onsite Soils Assessment” is one of the requisite courses that an ROWP Planner must take for certification. It is a rigorous, subjective, hands-on 3-day course. This learning guide will not attempt to explain any of the countless variations in soil makeup. With that in mind, a summary of soil structure would be that:
- The more clay there is in soil, the less favourable it is for a trickling gravity system because of clay’s low hydraulic conductivity.
- As well, the coarser and grainier the soil, such as gravel or sand, the less favourable it is because the effluent flows quickly through it and will not be retained long enough for proper aerobic bacterial action to take place.
- Soils that have a mixture of sand, loam and a limited amount of clay can usually be suitable for a disposal field. Again, the amounts of each constituent will influence the percolation rate through the soil and affect the hydraulic loading rate.
Once the soil structure and consistence are determined from the test holes, the information gathered is compared to various tables within the SPM to determine if the soil conditions are “favourable,” “poor,” “very poor,” or “NA” (not allowed). These terms refer to the proposed use of a gravity dispersal system and are factors in the use of tables in the SPM. If “NA” is encountered in the tables, a conventional trench system cannot be used, and either an above grade system or a lagoon must be used.
Percolation Test Procedure
Taken from III-8.3.2 of the SPM.
A percolation test is also performed to determine the soil’s acceptance rate for the effluent discharge. The following steps are used to conduct a percolation test in BC. Other provinces and states may use a different procedure:
- Perc test holes should be made at points and elevations selected as typical in the proposed absorption field.
- Typically, test holes are to be dug at each end of the area of the absorption field and near the centerline. Further holes could be needed, depending upon the nature of the soil, the results of the first tests and the size of the proposed dispersal area. Testing of the receiving area may also be necessary.
- Test holes should be 30 cm (12″) square or 36 cm (14″) round and excavated to the proposed depth of the absorption field (or as instructed by the designer). It is generally easiest to dig a larger hole part way down, then dig an 18 to 20 cm (7 to 8″) deep accurately sized test hole in the base of the larger hole.
- To make the percolation test more accurate, any smeared soil should be removed from the walls of the test holes. This is best achieved by digging the hole approximately 5 cm undersized (2″) and then enlarging the hole to the accurate size as follows: using a rigid knife, insert the blade into the top side of the hole opposite you approximately 2.5 cm (1″) deep, holding the blade with its cutting edge vertical. Pull the blade away to break out a chunk of soil, repeat about 2.5 cm (1″) apart around the hole, then repeat for another “ring” below until reaching the base. The result will be a hole with a ragged inner surface which looks like a freshly broken clod of soil.
- The base of the hole should be cleaned of debris and be approximately flat. Use a metal scoop or similar implement. It should also be picked to present a natural surface. Note that a picking action, using a pointed tool, is needed, not a scratching action (which just produces smears that are indented).
- Place 5 cm (2″) of clean fine gravel in the bottom of the hole. If the sidewalls are likely to collapse, use a paper basket to support the sidewalls (see note below). Place a piece of white plastic or similar provided with clear marks at 5″ and 6″ from the bottom of the test hole prior to adding the gravel. For greater accuracy a float and pointer arrangement can be set up.
- If the soil contains considerable amounts of silt or clay, and certainly for any soil with “clay” as part of the texture description, the test holes should be pre-soaked before proceeding with the test. Pre-soaking is accomplished by keeping the hole filled with water for 4 hours or more. The water should be added carefully and slowly to avoid disturbing the soil (including the sidewall soils). The test should be carried out immediately after pre-soaking.
- To undertake the test, fill the accurately sized test hole with water. The water should be added carefully and slowly to avoid disturbing the soil (including the sidewall soils). When the water level is 5″ or less from the bottom of the hole, refill the hole to the top. No recording of time needs be done for these 2 fillings.
- When the water level after the second filling in step 8 is 5″ or less from the bottom of the hole, add enough water to bring the depth of water to 6″ or slightly more. Note that these measurements are from the base of the soil bottom (using the marker installed in step 6), not the gravel layer.
- Observe the water level until it drops to the 6″ depth, at precisely 6″, commence timing. When the water level reaches the 5″ depth, stop timing, record the time in minutes.
- Repeat steps 9 and 10 until the last two rates of fall do not vary more than 2 minutes per inch or by more than 10% (whichever is less).
- Report the slowest rate for each hole.
- Backfill the holes with the excavated soil and flag and label their locations so you can recognize them when creating the plan of the installation.
Table II-5 of the SPM is then consulted to determine whether a gravity distribution system is allowed and is based on the soil type, vertical separation, percolation rate, and expected rainfall.
Soil type, Site constraint, or Planned Type of System | Other Factors | Gravity Distribution? |
---|---|---|
Very or extremely gravelly sand or coarse sand | not allowed | |
Gravelly sand, coarse sand, loamy coarse sand, sand and loamy sand | And where vertical separation (VS) is at least 150 cm in native soil (can include blinding layer) | allowed |
Fine sand, loamy fine sand, sandy loam, loam | And Type 1 effluent HLR, where VS is at least 90 cm in native soil (can include blinding layer)
And Type 2 effluent HLR, where VS is at least 120 cm in native soil (can include blinding layer) |
allowed
allowed |
Silt loam, silt | And where VS is at least 120 cm in native soil (can include blinding layer) | allowed |
Clay loam, sandy clay loam, silty clay loam, sandy clay, silty clay, or clay | And dispersal to an ET bed or ETA bed or to a lagoon
And dispersal to any other than an ET bed or an ETA bed or to a lagoon |
allowed
not allowed |
Kfs > 17000 mm/day
Or perc rate faster than 0.5 min/inch |
not allowed | |
Kfs > 1500 ≤ 17000 mm/day
Or perc rate 0.5 min/inch to less than 5 min/inch |
And where VS is at least 150 cm in native soil (can include blinding layer) | allowed |
Kfs ≤ 1500 mm/day
Or perc rate 5 min/inch or slower |
And Type 1 effluent HLR, where VS is at least 90 cm in native soil (can include blinding layer)
And Type 2 effluent HLR, where VS is at least 120 cm in native soil (can include blinding layer) |
allowed
allowed |
Kfs < 150 mm/day
Or perc rate slower than 60 min/inch |
And dispersal to an ET bed or ETA bed or to a lagoon
And dispersal to any other than an ET bed or ETA bed or to a lagoon |
allowed
not allowed |
Table II-6 identifies key constraints for the contemplated use of various types of dispersal systems.
System type | This type of system is not allowable if: |
---|---|
Trench systems | The land slope in the dispersal area is > 45%
Or > 25% and the vertical separation is < 90 cm |
Raised systems, sand mounds & at-grade beds | The land slope in the dispersal area is > 25% |
Trickling gravity distribution | The land slope in the dispersal area is > 15% (except ET beds or ETA beds with sequential distribution) |
Dosed gravity, close to D-box or splitter tee | The land slope in the dispersal area is > 15% |
Alberta At Grade systems | Treatment method is Type 1
Or the land slope in the dispersal area is > 15% Or the soil profile has < 5 cm of undisturbed L-F-H horizon or equivalent Or the site is not forested |
Type 1 below-grade seepage beds, Type 1 sand lined beds and Type 1 bottomless sand filters | The soil at the infiltrative surface is loam, silt loam, silt, clay loam, sandy clay loam, silty clay loam, sandy clay, silty clay or clay
Or the soil at the infiltrative surface is loamy sand, fine sand, loamy fine sand, sandy loam, fine sandy loam, with a structure and consistence category of Poor or Very Poor Or the median Kfs is < 250 mm/day Or the median perc rate is slower than 40 min/inch |
Seepage beds, sand lined beds and bottomless sand filters | The land slope in the dispersal area is > 15% |
BC zero discharge lagoons | The median Kfs is > 150 mm/day
Or the median perc rate is faster than 60 min/inch The property is smaller than 1.6 Ha The land slope is > 12% There is no annual net positive evaporation The VS is < 90 cm to SHWT or to a soil type or layer with perc or permeability unsuitable for a lagoon |
ETA beds | The median Kfs is > 150 mm/day
Or the median perc rate is faster than 60 min/inch There is no annual net positive evapotranspiration The VS is < 90 cm to SHWT or to a soil type or layer with perc or permeability unsuitable for an ETA bed |
ET beds | The annual net positive evapotranspiration is < 600 mm |
For the purposes of this area of study, the system type “Trickling Gravity Distribution” would be allowed provided that the land slope in the proposed dispersal area is not > 15% (13.5° from horizontal).
If soil constraints disallow the use of a gravity or dosed gravity distribution system, Table II-7 gives the planner guidance as to other options for dispersal.
Soil | Structure and consistence category | Constraining factor | Requirements (in addition to other standards) |
---|---|---|---|
Very or extremely gravelly sand or coarse sand Or Kfs > 17000 mm/day Or perc rate faster than than 0.5 min/inch |
F or P |
Very high permeability, risk of bypass flow and reduced treatment
|
Uniform distribution with timed or micro-dosing |
Clay loam, sandy clay loam, silty clay loam |
F or P VP |
Low permeability and risk of bypass flow
Restrictive layer |
Uniform distribution with timed or micro-dosing
Lagoon, Et bed or ETA bed |
Kfs 75 to 150 mm/day Or perc rate 60 to 120 min/inch |
Any |
Low permeability |
Uniform distribution with micro-dosing
Or sand mound with timed dosing Or lagoon, ET bed or ETA bed |
Sandy clay, silty clay, or clay |
F |
Low permeability and risk of bypass flow
|
Uniform distribution with timed or micro-dosing and Type 2 or 3
Or sand mound with timed dosing Or lagoon, ET bed or ETA bed |
Sandy clay, silty clay, or clay
|
P |
Very low permeability and infiltration capacity |
Uniform distribution with micro-dosing and Type 2 or 3 and minimum 30 cm sand media below infiltrative surface
Or lagoon, ET bed or ETA bed |
Sandy clay, silty clay, or clay
|
VP
|
Restrictive layer
|
Lagoon, ET bed or ETA bed
|
Kfs ≤ 75 mm/day
Or perc rate 120 min/inch or slower |
Any
|
Restrictive layer
|
Lagoon, ET bed or ETA bed
|
Soil with significant amounts of expandable clay minerals |
Blank
|
Restrictive layer |
Lagoon, ET bed or ETA bed
|
Organic soils
|
Blank
|
Limiting layer
|
ET bed
|
Soil structure and consistence category shows as “NA”
|
Blank
|
Restrictive layer
|
Lagoon, ET bed or ETA bed
|
High coarse fragment (c.f.) content (in any soil type)
(c.f. are soil particles larger than 2 mm) |
c.f > 35%
c.f. > 60% c.f. ≥ 90% |
Reduced soil treatment
Reduced soil treatment, risk of bypass flow Limiting layer |
Reduce HLR and HAR
Reduce HLR and HAR and uniform dosing and timed micro-dosing ET bed
|
Determine the Hydraulic Loading Rate (HLR), Area of Infiltrative Surface (AIS), and Linear Loading Rate (LLR)
Using the standards tables of the SPM involves selecting a soil type or a representative permeability. Selection of a soil’s hydraulic loading rate (HLR) involves selecting a soil texture class, structure and consistence category and a soil permeability or percolation rate. Once it has been determined that the soil conditions allow the use of a gravity trickling system and a percolation rate has been arrived at, in minutes per inch, the next step is to determine the HLR of the soil. The HLR is a measure of the volume of effluent, in litres, that can be applied each day per square metre of infiltrative surface (AIS). The maximum allowable HLR is based on maintaining the permeability of the infiltrative surface, by not overloading it, while treating the effluent within the unsaturated sand and soil. Two tables in the SPM are consulted using the soil conditions arrived at through the soil analysis and percolation test, and the lower of the two HLR numbers pulled from the two tables is used for the calculation of the minimum AIS. The formula used for that calculation is:
[latex]\text{DDF (L/day)}\div\text{HLR (L/day/m}^2)=\small\text{minimum area of infiltrative surface (AIS) needed (m}^2)[/latex]
Again, the explanations in this guide are abbreviated and descriptive only. An explanation of the process and procedures that must be followed in making a certifiable analysis of the soil conditions for the proposed field is far more in-depth and exhaustive than is warranted for the purposes of the explanations in this learning guide. Therefore, to illustrate the procedure used to determine the AIS and explain an example field sizing exercise, we’ll make these assumptions:
- A 3-bedroom house, with no garburator and not > 280 m2 of living area applied to Table II-8 = 1300 litres/day DDF
- After a soil test, it has been determined that the soil structure and consistence from Table II-21 (shown below) is considered “favourable” for a gravity trickle dispersal system
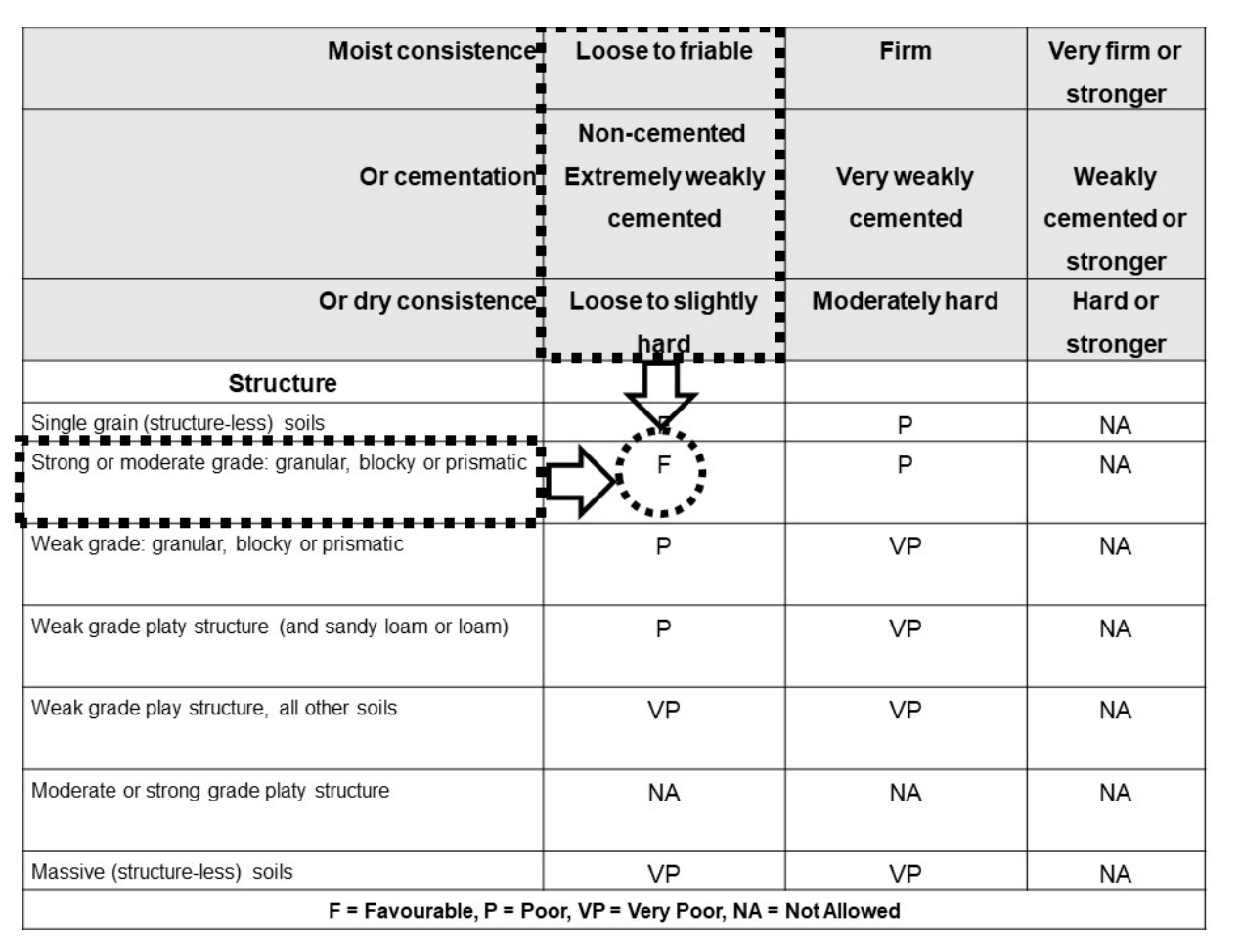
- The percolation rate, from the percolation test, is found to be 3 minutes/inch
- The soil type, from the soil analysis, is determined to be “loamy sand”
When the two applicable tables are consulted using the “loamy sand” determination and the percolation rate of 3 minutes/inch, the lesser of the two values is taken as the HLR for the dispersal area.
Using our assumptions, “loamy sand” and “favourable conditions” from Table II-22 indicate a hydraulic loading rate of 30 litres/day/m2 for our Type 1 system. When the percolation rate of 3 minutes/inch is entered into Table II-23, the HLR indicated is 35 litres/day/m2. This means that the HLR to be used will be 30 L/d/m2, which is the lesser of the two values.
Now that the HLR has been determined, it can be used in the following formula to determine the AIS required:
[latex]\small\text{minimum area of infiltrative surface (AIS) needed (m}^2)= \normalsize\text{DDF (L/day)}\div\text{HLR (L/day/m}^2)[/latex]
Using our example residence:
[latex]1\thinspace300\text{ litres/day}\div30\text{ litres/day/m}^2=43.33\text{ m}^2\text{ of infiltrative surface}[/latex]
This means that the total trench bottom area in the proposed field must be at least 43.33 m2.
Determine the Linear Loading Rate (LLR)
The total length of the disposal field can now be calculated and laid out within the area available. Local topography and other determining factors will be analyzed to determine where the trenches are to be dug, and their number, trench bottom width, and length. The total minimum length of the trenches is determined by computing the Linear Loading Rate (LLR).
The soil structure and consistence category are entered into a table to arrive at a linear loading rate. In a different table, just as with calculating the HLR, the soil permeability or percolation rate is entered to arrive at possibly a different LLR. The lesser of these two values is the LLR to be used in the following formula:
[latex]\text{DDF (L/day)}\div\text{LLR (L/day/m)}=\text{minimum system contour length (m)}[/latex]
As an example, if we were to use the DDF previously calculated as 1300 L/day and the LLR was found to be 35 L/d/m, the minimum contour (trench) length would be:
[latex]1\thinspace300\text{ litres/day}\div35\text{ litres/day/metre}=37.1\text{ metres of contour length}[/latex]
Longer, narrower trenches have more sidewall area than shorter, wider trenches and are therefore preferred by the SPM if site conditions allow. Also, there will be less water dispersed per meter which helps keep the infiltrative surface from becoming saturated.
Example of Trench Length Needed
Say there is a Daily Design Flow of 1300 L/day, HLR of 15 30 L/day/m2, and 0.6 m wide trenches.
The trench bottom area needed is:
[latex]\text{minimum AIS needed}=\text{DDF}\div\text{HLR}=1\thinspace300\div30=43.33\text{ m}^2[/latex]
Then the total length of trenches would be:
[latex]43.3\text{ m}^2\div0.6\text{ m}=72.2\text{ m }(236\text{ ft})[/latex]
The dispersal area would be mapped out to accommodate at least 72.2 m (236 ft) of trenches with a trench bottom width of 0.6 m (2 ft).
The figure below is a cross section that represents a conventional distribution trench.
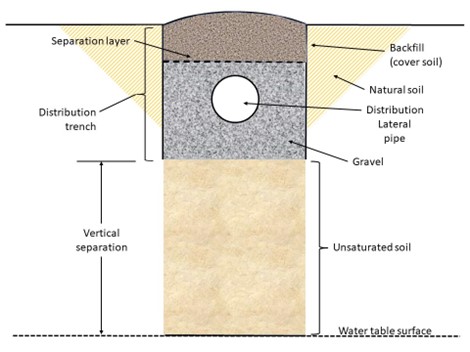
In the figure above, the unsaturated soil is native soil that hasn’t been excavated. It separates the “restrictive layer” (in this diagram the water table) and the bottom of the dug trench which is referred to as the “infiltrative surface.” The pipe (lateral) is laid into a bed of gravel (drain rock) over which is placed a “separation layer” such as lightweight non-woven geotextile or untreated building paper. The native soil is put back into the trench on top of the separation layer and is mounded to prevent surface water from flooding the field and allow for soil settlement.
The diagram below shows a cross section of a gravity distribution lateral with some minimum distances as mandated by the SPM.
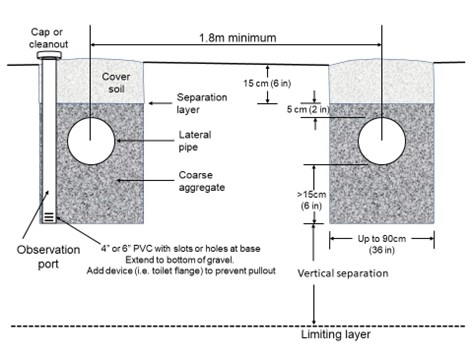
An “observation port” is simply a vertical pipe with a cap, placed in the trench, that allows the depth of water in the field to be easily checked.
Other suggestions from the SPM:
- Trench widths are 30-90 cm (12-36 in.); on slopes greater than 15%, use/specify a trench width of 30-60 cm (12-24 in.)
- Limit laterals to 15 m (50 ft) or less
- Install trenches level, or sloping in the direction of flow at no greater than 5 cm in 30 m (0.2%)
- Space trenches a minimum 1.8 m (6 ft) from centre line to centre line (c-c)
- On slopes greater than 15%, space trenches at least 3 m (10 ft) c-c
- Provide at least 0.9 m (3 ft) between adjacent trench edges
- Do not compact the soil under or over the lateral
- Use aggregate (drain rock) in the size range of 12 mm-63 mm (½″-2 ½″)
- Install aggregate to at least 15 cm (6 in.) depth below the distribution pipe and at least 5 cm (2 in.) above the pipe
- Install cover soil to at least 15 cm (6 in.) depth
- Install at least two infiltrative surface observation ports per drainfield
- Place observation ports 10–15 cm from the distribution pipe, and near the midpoint of the lateral
- Use 100 mm (4″) or larger diameter pipe
Self-Test 4
Self-Test 4
Treatment Methods
As mentioned previously, there are two distinct components to a sewerage treatment system – the dispersal area and the treatment method. Treatment methods are:
- Type 1: Treatment by a septic tank and dispersal field only.
- Type 2: Treatment that produces an effluent consistently containing less than 45 mg/L of TSS and having a BOD5 of less than 45 mg/L.
- Type 3: Treatment that produces an effluent consistently containing less than 10 mg/L of TSS and having:
- A BOD5 of less than 10 mg/L.
- A median fecal coliform density of less than 400 Colony Forming Units per 100 mL.
A Type 2 treatment system is typically a package treatment plant, and Type 3 is a municipal treatment facility. This literature will focus on Type 1 treatment method.
Septic Tank Installation
Pre-manufactured tanks must meet the standards found in CAN/CSA-B66-00 “Prefabricated Septic Tanks and Sewage Holding Tanks.” The septic tank process provides settlement of sludge and flotation of fats, oils, and grease, together with some anaerobic treatment and digestion of sludge. Settlement is improved in tanks that have a shallow and long flow path, and flotation is a function of surface area in relation to flow. Therefore, septic tank performance is improved by:
- Larger surface area (higher surface area-to-volume ratio)
- Longer distance between inlet and outlet pipes (higher length-to-width ratio)
- For two compartment tanks, letterbox openings in the compartment divider
Flow rates through the tank should be kept low to improve sedimentation efficiency and to prevent scouring of previously accumulated sludge. The SPM specifies using inlet and outlet baffles to achieve quiescent flow. An effluent filter is provided at the outlet of the tank, drawing effluent from the clear zone. This filter protects the dispersal system as well as improving BOD, TSS and Oil and Grease removal.
The working volume of a tank is its depth (measured from the invert of the outlet to the tank bottom) multiplied by its length and width and converted into a liquid measure.
Although the SSR does not address tank sizing, the SPM points to sizing the tank to meet the following criteria:
- For a daily design flow of up to 9100 L/day, the tank should have a working volume of at least 3 times the DDF
- For a DDF of more than 9100 L/day, the working volume should be at least 15000 L + (DDF in litres × 1.34) or as otherwise determined by a design professional
For example, if a 3-bedroom house has an expected DDF of 1300 L/day, a tank with a working volume of at least 1300 L × 3 = 3900 litres would be the minimum required size.
Septic tanks are available in single chamber and two compartment configurations. For tanks of equal volume and surface area, a single chamber tank will have improved settlement over a two-compartment tank. Conversely, a two-compartment septic tank will commonly have less scum accumulation at the outlet filter than a single compartment tank. The BC regulations no longer mandate the use of a 2-compartment tank, or 2 tanks in series. However, for tanks with 2 compartments or two tanks in series, the SPM specifies the use of tanks with ¾ to ½ of the total working volume in the first compartment.
The SSR recommends using larger tanks than the minimum for various reasons, including:
- To improve oil and grease removal
- To improve suspended solids removal
- To increase interval between pump outs
- To improve flow equalization where large surge flows are expected, such as from sewage sump pumps in basements.
To gain the best advantage from an increased tank volume, it is advisable to specify a tank with larger surface area and greater length between inlet and outlet as well as a larger volume. Treatment and digestion of the accumulated sludge and scum is improved with long sludge retention times. Larger tanks allow greater sludge accumulation which lengthens pump out intervals. According to Vol. III – 6.4.1.1 of SPM, pump out intervals of 5 years or more are preferred.
The SPM also notes that the use of low flow fixtures, such as ULF toilets, does not reduce the DDF rate for sizing purposes.
Tank Placement
In all likelihood the excavation for a septic tank will be more than 1.2 m deep, so workers in BC must adhere to WorkSafeBC® regulations requiring sloping or shoring when exceeding that depth. In all cases, tanks must be placed on a uniform level surface or bed that will not allow uneven settling, and which does not have rocks or roots that could create point loading on the tank. Bedding sand, drain rock or pea gravel should be used and compacted to an elevation that will allow gravity drainage flow through the building sewer at a minimum grade of ⅛″/ft [latex]\left(\frac{1}{100}\right)[/latex] according to the prevailing plumbing code.
Flotation Prevention
Tanks, especially if made of plastic, are prone to flotation especially when only partly full or empty. If groundwater conditions may lead to tank flotation, the ideal remedy is to drain the area around the tank. If this isn’t practical, prevent flotation by anchoring as per manufacturers’ recommendations. Water table standpipes, minimum 2″ diameter, can be installed vertically at the edge of the tank, for monitoring purposes. Pumping of the tank should be avoided in periods when the water table is high enough to cause the installed tank to float, as flotation can occur even though the tank is installed with adequate ground cover on it.
Tank Venting
All tanks are required to be vented. This is normally accomplished back through the sanitary building sewer. If this isn’t feasible, use a tank vent that is at least equal in cross sectional area to the tank inlet pipe and is installed to the standards found in Vol. II of the SPM.
Tank Access
After installation, there should be access to each chamber or compartment, above the inlets and outlets and for each baffle, tee or effluent filter. This allows for maintenance and helps to accommodate periodic inspections. Access tunnels, called “risers,” are sealed to the tank lid which is normally 12 inches or more below ground level.
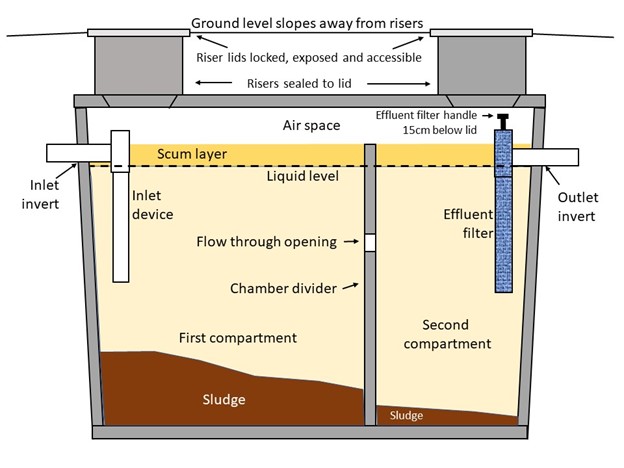
The following points regarding access should be considered:
- Any components that need to be accessed or removed should have handles or disconnect fittings located within 15 cm of the riser or access lid.
- Access lids should be exposed and readily accessible. They should be flush with finished grade or above (2.5 cm above is preferred).
- Access lids should be secure, either requiring special tools for removal, or provided with a lock.
- Removable access lids (including any job-built access components) should be capable of supporting at least 150 kg without collapse.
- Risers should be at least 50 cm internal diameter, or 60 cm when over a divider or if needed to access a pump etc.
- For tanks that are installed deeper than normal (over 90 cm of fill over the tank lid), larger access risers with a minimum diameter of 76 cm are preferable.
- Pump chambers will also require access. Provide two risers if one will be largely filled with the pump, connections, and float switches.
- The inlet pipe to the pump chamber should be accessible for visual inspection by the maintenance provider, or for collecting effluent samples for laboratory testing.
- Extend access risers to finished grade and slope the ground away from the riser lid
- Insulate the riser in cold climates
Backfilling
Backfilling should be done to tank manufacturers’ recommendations and guidelines.
Tank Testing
Test all tanks using water, to verify a rate of leakage less than 0.1% of volume per day. Alternately, use vacuum testing as described in the SPM. Test the tank, penetrations, and the lid seal.
Distribution Box Installation
Distribution boxes, if used, should be installed level on compacted fill. Speed levelers should be used in the outlets if the D-box is even slightly out of level. This ensures that the inverts of all laterals get equal flow. Like the septic tank, the D-box should have a riser large enough to accommodate maintenance and inspection, which should be extended to just above the surrounding ground.
Horizontal Separation
Table II-19 of the SPM, shown below, lists minimum clearance distances from wells, drinking water lines and cisterns, and water bodies to septic tanks and dispersal systems.
Minimum Horizontal Distance to |
From dispersal system (metres) |
From watertight treatment or pump tank (metres) |
---|---|---|
Surface source of drinking water
|
30
|
15
|
Domestic water supply well
|
30
|
30
|
Domestic water supply well, high pumping rate
|
60
|
30
|
Domestic water supply well, high pumping rate, in unconfined aquifer
|
90
|
30
|
Irrigation well or open loop geothermal well
|
15
|
7.5
|
Deep monitoring well or closed loop geothermal well
|
6
|
6
|
Shallow monitoring well
|
3
|
0
|
Minimum Horizontal Distance to |
From dispersal system (metres) |
From watertight treatment or pump tank (metres) |
---|---|---|
Drinking water suction line
|
30
|
15
|
Drinking water suction line, sleeved
|
7.5
|
3
|
Drinking water line, under pressure
|
3
|
3
|
Drinking water line, under pressure, sleeved
|
1
|
1
|
Drinking water supply cistern, below ground
|
15
|
3
|
Minimum Horizontal Distance to |
From dispersal system (metres) |
From watertight treatment or pump tank (metres) |
---|---|---|
Permanent freshwater body
|
30
|
10
|
Intermittent freshwater body
|
15
|
10
|
Marine water body
|
15
|
7.5
|
Breakout point or downslope drain
|
7.5
|
0
|
As well, Table III-16 of the SPM below provides more suggested distances for horizontal separations.
Distance to | From dispersal system (metres) | From watertight subsurface treatment tank (metres) |
---|---|---|
Property lines | 3 | 1 |
Building or structure (where there is not a perimeter drain) | 1 | 1 |
Dispersal system (including other dispersal system) | 6 | 3 |
Buried utility services | 1 | 1 |
Drinking water supply cistern, at or above ground | 1 | 1 |
Commissioning the System
The following checklist for system commissioning is general in nature, with most of the points being specific to pressurized dispersal systems.
- Set float switches or transducers, and test the system operation, including alarms
- Set the pump control panel (timers, data loggers and programmable controls) and test operation
- Test pumps, fan, and blower operation, and measure the voltage and run amperage
- Check the force mains, including the pressure effluent collection mains, for leaks
- Flush all lines in the treatment and pumping systems, transport lines and dispersal system
- Test back-flow preventers (i.e., check valves).
- Test and adjust the D-box and outlet controls (gravity system with D-box).
- Test the pressure distribution residual pressures (a.k.a. “squirt test”). This may include the final pressure distribution system, and treatment system distribution piping (i.e., sand and textile media filters). Adjust valves, as required, to equalize pressure. Record distal pressures (squirt heights).
- Test and record pump discharge flow rate or draw down. Record pump run amperage.
- Record the initial control panel settings, system operating parameters, and the start-up data logs. Note any changes to the design or operational settings.
- Complete a general review of the system operation to verify that it is operating as intended, and in accordance with the manufacturer’s specifications
- Perform baseline monitoring if applicable (e.g., record water table levels in observation standpipes, collect and test samples of water from drainage system).
- Put the sewerage system into service. Ensure that the breakers, switches and valves are in operating position, the tank lids are secure and that the site has been left in a safe and tidy condition.
Self-Test 5
Self-Test 5
Media Attributions
- Figure 26. “Typical gravity distribution trench” by Camosun College is licensed under a CC BY-NC-SA licence.
- Figure 27. “Typical trench installation with observation port” by Camosun College is licensed under a CC BY-NC-SA licence.
- Figure 28. “2-compartment septic tank” by Camosun College is licensed under a CC BY-NC-SA licence.
Image descriptions
Table II-21 image description:
Moist consistence | Loose to friable | Firm | Very firm or stronger |
---|---|---|---|
Or cementation | Non-cemented
Extremely weakly cemented |
Very weakly cemented | Weakly cemented or stronger |
Or dry consistence | Loose to slightly hard | Moderately hard | Hard or stronger |
Structure | Loose to friable | Firm | Very firm or stronger |
---|---|---|---|
Single grain (structure-less) soils | Poor | Poor | Not allowed |
Strong or moderate grade: granular, blocky or prismatic | Favourable | Poor | Not allowed |
Weak grade: granular, blocky or prismatic | Poor | Very poor | Not allowed |
Weak grade platy structure (and sandy loam or loam) | Poor | Very poor | Not allowed |
Weak grade play structure, all other soils | Very poor | Very poor | Not allowed |
Moderate or strong grade platy structure | Not allowed | Not allowed | Not allowed |
Massive (structure-less) soils | Very poor | Very poor | Not allowed |
Infiltrative surface area, in m², receiving effluent from the distribution system. This is considered to be the bottom area of a trench in a trench-type gravity system.
A registered onsite wastewater practitioner or professional.
5-day biochemical oxygen demand
daily design flow
hydraulic application rate
hydraulic loading rate
horizontal separation
linear loading rate
percolation rate
percolation rate
point of application
A person who is qualified to act as a registered onsite wastewater practitioner under section 7 (1) or (2) of the Sewerage System Regulation.
seasonal high water table
Sewerage System Standard Practice Manual, Version 3. Access a PDF version of the SPM online.
Sewerage System Regulation within the Public Health Act
total suspended solids
vertical separation
For sand mounds, sand-lined trenches, bottomless sand filters, Alberta At Grade systems and CTDS, this is the native soil that the sand will be placed on.
A layer of clean coarse sand or mound sand that is installed between the infiltration surface (bottom of aggregate, base of chamber, etc.) and the native soil, and which is up to 10 cm (4 inches) thick.
Attribute of soil expressed in degree of cohesion and adhesion, or in resistance to deformation or rupture.
Rounded or subrounded rock fragment that is between 0.1 inches (2 millimetres) and 3 inches (76 millimetres) in diameter. Often called “drain rock.”
A measure of the volume of effluent, in litres, applied each day, per unit area (m²) of infiltrative surface.
In drainfields, the drain rock-to-original soil interface at the bottom of the trench; in mound systems, the gravel-to-mound sand and the sand-to-original soil interfaces; in sand-lined trenches/beds (sand filter), the gravel-to-sand interface and the sand-to-original soil interface at the bottom of the trench or bed.
A measurement of the saturated hydraulic conductivity of soil. In theoretical terms, hydraulic conductivity is a measure of how easily water can pass through soil or rock. High values indicate permeable material through which water can pass easily, such as sand or gravel; low values indicate that the material, such as clay, is less permeable.
The shallowest of a restrictive layer, water table, seasonal high-water table or extremely permeable material (e.g., fractured rock, gravel).
A layer of soil or rock that impedes the vertical movement of water, air, and the growth of plant roots. This may include hardpan, some compacted soils, bedrock, glacial till and unstructured clay soils.
Laminated or flaky soil aggregate developed predominantly along the horizontal axis.
Layers of soil or soil material approximately parallel to the land surface and different from adjacent layers in physical, chemical, and biological properties or characteristics such as colour, structure, texture, consistence, and pH.
The combination or arrangement of individual soil particles into definable aggregates, or peds, which are characterized and classified based on size, shape, and degree of grade (distinctness).
The relative proportions of the various soil separates (e.g., silt, clay, sand) in a soil.
The depth of unsaturated, original, undisturbed permeable soil below the infiltrative surface and above any limiting layer. This is the vertical depth of soil that the dispersal system is expected to be discharged into.