Competency A2: Test and Commission Medical Gas Systems
Learning Task 1
Describe the Testing and Commissioning of Medical Gas Systems
In practice, the commissioning process comprises of a set procedure to check, inspect and test every operational component of the system. Few installations that a tradesperson will be involved with have more ability to cause immediate loss of life than a medical gas system that has been incorrectly installed. The need to strictly test various aspects of medical gas piping installations is imperative.
The system must pass alarm notification, piping pressure, cross-connection, gas concentration, particulate contaminant and terminal unit flow tests. The requirements for each of these tests are very specific, and systems must pass all of the tests before receiving approval for operation. Under certain circumstances the authority having jurisdiction may require additional testing.
System testing involves a series of procedures before systems can receive final approval. Some of these tests are performed by the installer as described in Appendix B of the CSA Z7396.1 Standard, and some by the inspection body as described in Appendix D. Some of the tests are the same or similar for both parties to ensure consistent results.
Before using a new or modified supply system or pipeline distribution system or an addition or
renovation to an existing system, the health care facility shall obtain documented evidence from an approved testing agency that the system complies with the CSA Standard.
Approved testing agencies
The CSA Standard Z7396.1-12 states that medical gas pipeline systems shall be commissioned after installation and then be subjected to a certification inspection. This inspection must be completed by an approved testing agency. In order for a company to become an approved testing agency, it must first be recognized as an inspection body by the Standards Council of Canada for the inspection of non-flammable medical gas piping systems for compliance with the CSA Standard.
Medical gas testing services include:
- testing and certification of newly installed or renovated medical gas systems
- annual maintenance assessment and gas purity testing
Verification of installer qualification
In order to certify the system, the testing agency is required to verify the qualifications of the installer. The installer will be required to produce:
- Evidence of qualification meeting the requirements of the CSA Medical Gas Piping & Systems Installation Personnel Certification Program or equivalent
- A valid brazing license issued by an authority having jurisdiction
- A current copy of relevant standards
Installer testing
The medical gas system installer and the designer shall be jointly responsible for the performance of the tests. The installer shall provide documentation to the inspection body that all tests have been performed.
Clause 11.4.3.2 of the CSA Z7396.1 Standard lists the tests to be performed by the installer after the connection of the terminal units, these include:
- a 24-hr. standing pressure test,
- a final leak test,
- purge the terminal units,
- a particulate filter test, and
- cross-connection tests
If the system fails any of these tests, the failure condition shall be investigated and corrected, and the system shall then be retested.
Annex B of the CSA Z7396.1 Standard describes the installer test procedures.
To perform the tests you will need to have a terminal unit testing assembly similar to Figure 1.
- Terminal unit
- Manufacturer’s gas-specific connector
- 0–690 kPa (0–100 psi) oxygen cleaned pressure gauge with a resolution of at least ± 7 kPa (± 1 psi) for compressed gases or 0–101 kPa (0–30 in Hg) with a resolution of ± 3.4 kPa (1 in Hg) for vacuum and AGSSs
- ¼” NPT tee
- ¼” NPS non-restrictive shut-off valve
- ¼” NPT cap centre drilled to create a clean 1.98 mm (5/64 in) orifice
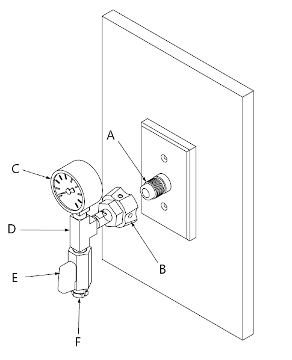
You will need to change the gas specific connector (DISS shown) on the assembly for each type of gas or have multiple assemblies. The drill cap will only be installed for tests that require a controlled flow rate
Leak (pressure) testing
Before system components are attached, each section of the piping system must be subjected to a pressure test with oil-free, dry nitrogen. When pressure testing a medical gas installation, it is very important that the test pressure reading on the gauge is accurate. The test dial should be larger than 38 mm (1 ½ in.) in diameter to allow a more accurate reading. Most pressure gauges have their highest accuracy in the middle third of the gauge; therefore, the selected gauge should have a range of about twice the required test pressure.
Two pressure tests for the detection of leaks shall be performed:
- The standing pressure test to confirm the work is of the required quality
- The final leak test to provide a record that the installation of the system meets code requirements
The standing pressure test shall include the following:
- All joints are subject to a 24-hour standing pressure test.
- The test gas shall be oil-free dry air or oil-free nitrogen and all piping shall be pressurized to 1030 kPa (150 psi) or 1 ½ times the operating pressure, whichever is greater.
- Vacuum lines are tested to a maximum of 415 kPa (60 psi).
- The only allowable change in pressure during the 24-hour test is due to ambient temperature changes in the areas around the piping tested.
Upon completion of the 24-hour test and the installation of the final components (alarm components and outlet covers), the final leak test at system working pressure shall be performed.
Purge terminal units
After completion of the pressure tests, the terminal units must be purged a sufficient number of times to clear them of particulate matter. Using appropriate adapters (or the test assembly without the orificed cap), each outlet should be purged with an intermittent high-volume flow of test gas until the purge produces no discoloration in a clean white cloth loosely held over the adapter (Figure 2).
Start at a point closest to the source of supply and move outward to the end of the pipeline. Rapidly interrupting the flow several times (pulse purging) has been found to effectively break up materials in the pipeline such as cupric oxide scale.
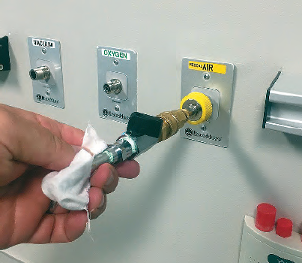
The outflow from each gas terminal unit must also be observed to confirm the absence of visible moisture (i.e., droplets or mist).
Particulate filter test
After the entire piping system has been purged the installer shall perform a visual test of all compressed pipelines for particulate contamination. This test is very similar to final step of the purge procedure; were a clean white cloth or a white 0.3 micron particulate filter is placed over the end of the terminal unit test assembly. The significant difference is that a flow regulation orifice is installed in the test assembly to ensure a minimum flow of 120 L/min (4 SCFM) for at least 15 seconds. The filter shall be free from particulate matter when viewed by the naked eye in good light. At least one terminal unit for each compressed gas in each zone shall be tested.
Cross-connection testing
Cross-connections are the main cause of deaths and injuries with medical gas systems, therefore the initial cross-connection test should be considered the most important installer performed tests. The installer ensures that there are no cross-connections in the installed systems and then the inspection body will also perform cross-connection tests to validate the installers results. The CSA Z7396.1 Standard describes two methods of conducting a cross-connection test. Depending on the number of gas services provided the installer will complete a cross-connection test using one of the methods described in the CSA Z7396.1 Standard.
During the initial cross-connection test, it is vital to confirm that the labelling and identification of the terminal units match the correct pipeline being checked.
Method 1 (Individual Pressurization method can be used when there are one or more services)
- Involves the pressurization of a particular medical gas piping system with oil-free air or oil-free nitrogen to 345 kPa (50 psi). All other pipelines shall be reduced to atmospheric pressure.
- A gauge is then attached to each terminal unit to ensure that only the proper outlets for the medical gas system being tested is pressurized. Disconnect the test gas from the system that was just tested and reduce the pressure in the system to atmospheric.
- This test must be carried out for each medical piping system and all terminal units are checked each time to ensure no pressure is registered at any terminals that are not part of the gas service being tested.
- Each terminal unit shall be inspected to ensure that it is properly identified by name and colour.
Method 2 (Pressure differential method can be used when there are pipelines for more than two gases in addition to vacuum)
- Involves the pressurization of all medical gas piping systems at different pressures with oil-free air or oil-free nitrogen. The pressure in one system shall be raised to at least 140 kPa (20 psi) and the pressure in the other pipelines shall be adjusted to a level that has a clearly recognizable pressure difference of no less than 70 kPa (10 psi) between each gas.
- If medical vacuum or AGSS are to be tested, they shall be set to a level of 0 kPa (0 psi). If both are used, they shall be set at a level of 0 kPa (0 psi) and 70 kPa (10 psi) respectively.
- After the different system pressures have been set every terminal unit must be measured using a pressure gauge attached to the specific adapter for that terminal unit. The pressures must be monitored to ensure the differentials are maintained.
- Each terminal unit shall be inspected to ensure that it is properly identified by name and colour.
The pressure differential method (Method 2) is only meant as an option when there are pipelines for more than two gases in addition to vacuum . The individual pressurization method (Method 1) can be used for all sizes of systems as it provides for less chance of both mechanical and human error in identifying a cross connection.
Commissioning and Certification
After completion of the installer testing and prior to commencement of the compliance testing, the installer and a representative of the system designer shall review the installation and provide written and signed attestation to the health care facility that:
- every terminal unit in an occupied area under test is labelled to indicate that the system is under test and that it shall not be used
- all safety interlocks are functional (e.g. terminal unit disconnects)
- the system as installed is as designed and
- the pipeline installation test report has been submitted.
When all of the installer tests are satisfied the inspection body can be called to certify the system. The inspection body will conduct the final testing prior to use to demonstrate that the supply system or pipeline system, or both, complies with this Standard. The system shall not be used until it complies and the inspection body has provided a written certification report to the health care facility and the installer.
The following inspections/tests are performed by the inspection body in the presence of the installer.
Supply system inspection/testing
Each source within a supply system shall be functionally tested according to the requirements of the CSA Standard and the manufacturer’s manuals and specifications. Annex C of the CSA Z7396.1 Standard provides a detailed list of all of the visual inspections, functional tests, and alarm simulations that must be performed on each supply system and its control equipment. To prepare for this compliance testing of the supply systems all alarm wiring must be completed. The main isolation valve for each source will remain closed and locked out until the source commissioning and inspection is completed. At least two bottles of each type of pressurized gas will need to be connected to verify each supply manifold operation.
Supply manifolds
Once all of the components of the portable cylinder supply systems have been visually inspected the function of the manifold automatic changeover will need to be tested. The following are an example of the typical steps for commissioning and operational testing of a medical gas manifold. On the job it is important to follow the actual manufactures instructions.
- Remove the manifold control panel cover.
- Verify the following:
- Both master valves located on both header bars are turned fully counter clockwise (open)
- All four line regulator isolation valves are open
- Power supply has been connected
- Both red “Empty” indicators on the front of the manifold are illuminated
- If connected to a master alarm panel, “Secondary Supply” alarm is activated
- ¾” source shut-off valve is closed and locked out
- Slowly open one cylinder on the right side of the manifold.
- Verify the following:
- Right bank red “Empty” LED goes out
- Right bank green “In Use” LED illuminates
- Right bank cylinder contents gauge reads cylinder pressure
- Slowly open one cylinder on the left side of the manifold.
- Verify the following:
- Left bank red “Empty” LED goes out
- Left bank yellow “Ready” LED illuminates
- Left bank cylinder contents gauge reads cylinder pressure
- If connected to a master alarm panel, “Secondary Supply” alarm is not activated
- Close right bank cylinder. Slightly open vent/bleed valve. Verify the following:
- Right bank cylinder contents gauge drops slowly
- As the right cylinder contents gauge is nearly depleted, the manifold changes over to the left bank
- After changeover, the right bank green “In Use” LED goes out and the red “Empty” LED illuminates
- After changeover, the left bank yellow “Ready” LED goes out and the green “In Use” LED illuminates
- Verify the line pressure gauge reading is acceptable.
- Slowly open one cylinder on the right side of the manifold.
- Verify the following:
- Right bank red “Empty” LED goes out
- Right bank yellow “Ready” LED illuminates
- Right bank cylinder contents gauge reads cylinder pressure
- Close the left bank cylinder. Depress the valve located on the side of the line regulator. Verify the following:
- Left bank cylinder contents gauge drops slowly
- As left cylinder contents gauge is nearly depleted, the manifold changes over to the right bank
- After changeover, the left bank green “In Use” LED goes out and red “Empty” LED illuminates
- After changeover, the right bank yellow “Ready” LED goes out and green “In Use” LED illuminates
- Slowly open one cylinder on the left side of the manifold.
- Verify the following:
- Left bank red “Empty” LED goes out
- Left bank yellow “Ready” LED illuminates
- Left bank cylinder contents gauge reads cylinder pressure
- If connected to a master alarm panel, “Secondary Supply” alarm is not activated
- Close the left and right-side cylinders.
- Record the pressure readings of the left and right bank cylinder contents gauges.
- Wait 15 minutes.
- Compare current readings of the left and right bank cylinder contents gauges to those recorded in step 15. If there is a noticeable pressure change on either gauge, perform leak testing.
- Reinstall manifold control panel cover.
- When the piping system is ready to receive gas slowly open the locked-out source shut-off valve.
Supply plants
Vacuum pumps, medical air compressors, and oxygen concentrators are to be started by factory rep and running for at least 24 hours. Failure to have an authorized manufacture technician start-up the system can void the manufacturer’s warranties.
New compressors often produce odours. At initial start-up the air produced by the compressor should be diverted from the system upstream of the dryers (and the receivers, if possible) and vented to waste, preferably outside the facility then the compressor can be operated until there is no detectable odour in the discharge air. This will ensure the downstream piping and equipment does not become contaminated with odour-causing materials.
A sample of the compressor discharge air will be taken by the inspection body at a point downstream of the dryers and upstream of the supply shut-off valve. A gas sample will be taken at each source to verify the gas conforms to the USP formulary. Samples must be analyzed by a laboratory meeting the requirements of ISO/IEC 17025 for the testing of medical gases. The source samples will also be used later as a comparison to an end point sample to ensure the pipeline distribution system is not adding contaminants to the source gas.
The supply plant tests detailed in Annex C shall be performed in the presence of the manufacturer’s representative as well as the inspection body, so that the test or simulation can be conducted without compromising the integrity of the equipment or voiding a warranty.
Pipeline distribution system inspection/testing
Annex D of the CSA Z7396.1 Standard provides a detailed list of all of the visual inspections, functional tests, and alarm simulations that must be performed on each pipeline, valve and zone alarm. The installer shall make the working as-constructed drawings available to the inspection body at the time of the inspection.
System pipeline purge
During this procedure, each gas-specific pipeline shall be filled and emptied a sufficient number of times to displace the test gas used in the testing performed by the installer. Each terminal unit shall be opened in turn to ensure that no sections of pipeline remain filled with test gas.
Inspection of outlets, junction points and valves
This inspection confirms that:
- Each outlet of a pipeline distribution system has a terminal unit that is brazed to the pipeline with no flexible hose intervening or a medical supply unit junction point.
- Each junction point for a medical supply unit is readily accessible for service and either permanently connected to the medical supply unit (e.g., by brazing or welding) or fitted with a gas-specific DISS connector.
- Each supply system shall have a shut-off valve located as close as possible to the supply system outlet.
- Each supply system located outside the facility shall have a service isolation valve, secured in the open position, within the supply system enclosure.
- Each pipeline and service isolation valve is installed as outlined in the CSA Z7396.1 Standard.
- All labelling is installed as stated in the CSA Z7396.1 Standard.
- All pipeline installations shall be checked for compliance with the CSA Z7396.1 Standard.
- The installation tests haves been performed by the installer.
- Each zone valve shall be checked for correct identification and operation.
- Each zone valve shall be checked to verify that they control only those terminal units intended by the system design.
Particulate filter test
The approved testing agency shall test all pipelines for compressed medical gases for particulate contamination. This procedure is identical to the earlier test performed by the installer.
Gas identity and cross-connection
This test is performed after the source of test gas shall be disconnected and the proper gas source of supply is connected to each system.
- Each system is purged a sufficient number of times to remove the test gas.
- The line pressure regulator controlling each piped gas must be adjusted to maintain a clearly recognizable pressure difference of no less than 35 kPa (5 psi).
- The medical vacuum system shall be in operation, and the cut-in and cut-out settings of the vacuum pump controller are to be measured and recorded.
- After all of the different system pressures are adjusted and recorded, every terminal unit must be checked with a pressure gauge attached to the specific adapter for that terminal unit. The pressure at the terminal units is recorded while there is a flow of 15 to 25 L/min (0.5 to 1 SCFM). The recorded flow pressure must be the same as the previously recorded static pressure for the system.
- The outflow gas concentration from each gas terminal must be tested using the appropriate gas analyzer. Gas concentrations should measure at least 99% for oxygen, nitrous oxide, carbon dioxide, helium, and nitrogen and 19.5 to 23.5% oxygen for medical and instrument air.
Check of terminal units
Each terminal unit is checked to ensure that gas is released only when the correct gas-specific connection device is inserted into the terminal unit.
Contaminant testing
Tests for contaminants in a medical gas piping system are taken from a terminal unit after the gas has been allowed to travel the maximum length of the medical gas piping system. The gas samples are then sent to an independent laboratory for analysis. The terminal unit samples are compared to the previous taken system supply samples, to ensure there are no pipeline contaminants being added to the supplied gas.
Flow testing
Each terminal unit shall be tested for flow resistance. The flow test measures the pressure drop across the terminal unit and its inlet connector. The terminal unit test assembly complete with a 1.98 mm (5/64 in) flow regulation orifice is used to measure both static then flow pressure at each terminal unit. When testing, the pressure drop shall not exceed 70 kPa (10 psi) for nitrogen, 30 kPa (4 psi) for all other medical gases and 13 kPa (4″ Hg) for medical vacuum.
Alarm testing
The CSA Z7396.1 Standard lists the testing protocols for alarm testing in Table D.3. The table lists the different alarm system components, the characteristic or function being checked, and the type of tests performed. The approved testing agency would complete the entire list of prescribed tests before system certification.
A typical functional test of a positive pressure alarm would be the following:
- Close the applicable service (shutoff) valve to the area
- Increase the line pressure in the piping system to the high-pressure alarm set point.
- Check the applicable alarm panel to ensure that the properly labelled warning signal is activated
- Check a test gauge in the area to ensure that the pressure reading is the same as the reading on the alarm panel.
- Silence the audible signal. The visible signal should remain activated.
- Reduce the line pressure in the piping system to the normal operating pressure and check the applicable alarm has deactivated and the pressure readings are back to normal.
- Reduce the line pressure in the piping system to the low-pressure alarm set point.
- Check the applicable alarm panel to ensure that the properly labelled warning signal is activated.
- Check a test gauge in the area to ensure that the pressure reading is the same as the reading on the alarm panel.
- Silence the audible signal. The visible signal should remain activated.
- Open the service (shutoff ) valve to the area
- Check the applicable alarm has deactivated and the pressure readings are back to normal.
- Disconnect the low voltage alarm wiring from the pressure switch or transducer.
- Check the applicable alarm panel to ensure that the properly labelled warning signal is activated.
- Reconnect the low-voltage alarm wiring to the pressure sensor.
- Check the applicable alarm has deactivated
- Document the test results.
Final Approval
Medical gas supply and or pipeline distribution systems can not be used until the health care facility has obtained written confirmation from the inspection body that the installation conform to the requirements of the CSA Standard. When the results of the inspections meet the Standard, the inspection body must issue a certification report to the health care facility. The inspection body shall also confirm that working as-built drawings and evidence of installer qualifications have been provided to the health care facility. The health care facility shall retain the certification report, working as-built drawings, as well as copies of individual brazing licences (if applicable) for inclusion in their permanent records.
Either the installer or manufacture shall also provide the health care facility with all of the necessary operating and service manuals for the newly commissioned equipment as well as the recommend maintenance schedules.
Now complete Self-Test 1 and check your answers.
Self-Test 1
Self-Test 1
Media Attributions
- Figure 1. “Typical terminal unit test assembly” – The source for this image is unknown. It is being used for non-commercial, educational purposes. To receive credit for this image, please reach out to the publisher.
- Figure 2. “Piping purge being performed at a terminal unit” – The source for this image is unknown. It is being used for non-commercial, educational purposes. To receive credit for this image, please reach out to the publisher.