Competency A1: Install Medical Gas Systems
Learning Task 3
Install Piping for Medical Gas Systems
The medial gas system supplies clean, contaminant-free gasses through hundreds, if not thousands, of feet of pipe and tube that has been cleaned and installed per requirements of the CSA standard.
Certification requirements
The Z7396.1 Standard states in clauses 11.4.1.1 and 11.4.1.2 that:
An installer shall meet the requirements of the CSA Medical Gas Piping & Systems Installation Personnel Certification Program or equivalent.
And that:
Prior to any installation, with the exception of stationary liquid supply systems, installers shall submit evidence of qualification to install medical gas systems to the health care facility for inclusion in its permanent records.
Note: In Canada, evidence of qualification to install medical gas systems consists of a valid medical gas licence meeting the requirements of the CSA Medical Gas Piping & Systems Installation Personnel Certification Program or equivalent.
To meet the certification needs of industry, the CSA Group has formed a training partnership with the United Association Canada (UA) and the National Association of Union Schools and Colleges (NAUSC). The UA Med G.A.S. program prepares journeyperson and apprentice pipe trades workers with the skills and abilities to complete medical gas piping installations safely and securely in all forms of construction and maintenance operations in the hospital construction industry. Once certified the installer will possess the necessary knowledge of the following:
- CSA-Z396-1 Standard requirements
- medical gas tools and equipment
- principles of medical gas pipeline systems
- brazing and purging theory
- certification requirements
- hospital shutdowns
- practical brazing and purging
- installation tests
To apply to take the Medical Gas Piping and Systems Installer exam for certification, candidates must satisfy the following prerequisites and submit documentation:
- Certificate of Qualification (C of Q) Plumber or Steamfitter/Pipefitter; and
- Documented completion of a recognized medical gas training program that includes:
- 32 hours classroom training, and
- 4-hour practical/hands-on training (brazing / purging procedures); and
- Valid provincial brazing test (acceptable to the AHJ in province of residence).
The Standard also states:
If applicable, prior to any installation, installers shall submit evidence of qualification (e.g., a valid brazing licence, as issued by an authority having jurisdiction in accordance with CSA B51) to the health care facility for inclusion in its permanent records. Currently, the Technical Safety of BC – Boiler and Pressure Vessel Safety Program has been designated to perform the oversight functions cited in Clause 4.5 of CSA B51.
In addition to meeting the requirements of the CSA Medical Gas Piping & Systems Installation Personnel Certification Program, installers of Corrugated Medical Tubing (CMT) shall complete and pass the manufacturer’s training course.
Codes and regulations
The installation, use and verification of medical gas pipeline systems are governed by the CSA Z7396.1 Standard. The current version is not a legislated document that is mandatory in all areas of Canada. It is a voluntary standard that is available for use or reference by those involved with medical gas piping systems. In order for the standard to become mandatory, it must be listed within the National Building Code (NBC), which sets out construction and building standards for Canada.
The Standard provides a detailed list of supporting standards that are referenced to be used in conjunction with the CSA Z7396.1. These other standards are primarily from Canada, the United States or the European Union and cover areas such as pressure vessels/piping (CSA B51), performance requirements for piping material (ASTM) and electrical requirements (CSA Z22.1), to name a few. The rationale for using these other standards is that they deal with very specific topics that have a direct relationship with medical gases or pipeline systems.
Besides the various sections that list the system requirements, there are also diagrams, tables and annexes, which offer both mandatory and normative references. These are intended to further assist in understanding various concepts, give examples of specific situations or provide much more detail of particular requirements.
Location
The positions of pipes, supports, fixings and terminals are determined from plans and specifications or site requirements, so as not to cause damage or interference to surrounding structures. The CSA Z7396.1 Standard states the installation requirements for pipelines in the following clauses:
- 11.2.1: Pipelines and electrical services shall either be run in separated compartments or, if in the same compartment, separated by at least 50 mm (2 in.) or by conduit.
- 11.2.2: Pipelines in corridors and other exposed locations shall be protected from physical damage (e.g., from the movement of portable equipment, such as trolleys, stretchers, and trucks).
- 11.2.3: Unprotected pipelines shall not be installed in hazardous areas (e.g., in areas where flammable materials are stored). Where installation of pipelines in such a location is unavoidable, the pipeline shall be protected by an enclosure that will prevent the release of medical gas within the room if leaks occur.
- 11.2.4: Pipelines shall not be installed in elevator shafts.
- 11.2.5: Terminal units shall be located or protected so as to avoid physical damage to the terminal unit and attached auxiliary or control equipment. Risk analysis shall be in accordance with CAN/CSA-Z1002
- 11.2.6: Where medical gas pipelines are installed in pipe shafts with other services, they shall be suitably protected against physical damage and excessive temperatures.
If pipelines are placed in the same tunnel, trench, or duct with fuel pipelines, steam lines, or other services, they shall be a minimum of 50 mm (2 in) apart.
Ducts in which pipelines are installed shall be ventilated. - 11.2.7: Buried pipelines shall be placed below the frost line in free-draining, non-corrosive backfill. Measures (i.e., permanent signage, physical barriers, or both) shall be taken to protect the pipeline from accidental digging or other damage. A medical gas pipeline shall not be placed in a tunnel, trench, or duct where it can be exposed to oil. Corrugated medical tubing shall be routed in a watertight, non-metallic conduit when installed underground or when encased in concrete.
- 11.2.8: A continuous tape or marker placed at half-depth above the pipeline shall clearly identify the pipeline by name
Pipe types
Copper has antibacterial properties which make it ideal for use in medical gas installations. The pipelines shall be either:
- Seamless copper tubing that complies with the ASTM B 819 standard. Type K or L hard temper copper tube is used for all locations except underground, where soft temper is preferred in order to reduce the number of inaccessible joints. Type K must be used where operating pressures are above 1275 kPa (185 psi) and the pipe size is larger than NPS 3 inch.
- Listed corrugated medical tubing (CMT) and fitting system fabricated from copper alloy No. 51000 strip meeting ASTM B103/B103M and is certified to UL 1365 (Figure 28). The CMT is externally coated with a non-metallic sheath which has the proper flame and smoke rating. The CMT has a minimum pressure rating of 1100kPa (160 psi) and cannot be used for vacuum piping.
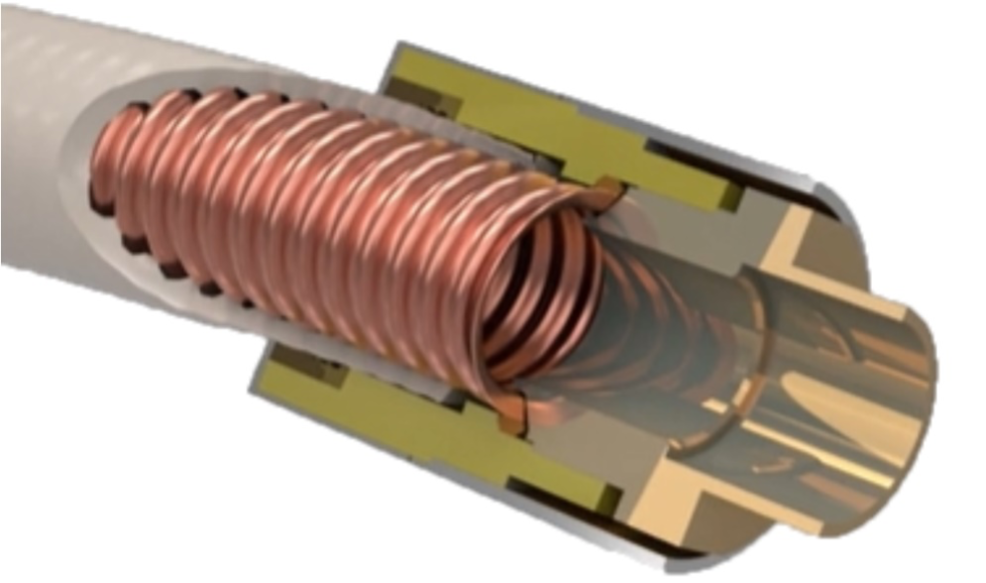
The only exception to these two pipeline materials requirements are approved flexible connection assemblies which are used for vibration isolation and expansion control.
Hangers and supports
Hangers and supports are installed to comply with plans, specifications, standards, authorities’ requirements and manufacturer recommendations. Installation requires added care for the protection of pipes from physical harm. Medical gas pipe is hung independently from other piping, and the hangers must be of a type, style and strength that will prevent accidental pipe movement. Figure 29 lists the maximum spacing of piping supports.
NPS (mm) | Spacing of support ft. (m) Horizontal | Spacing of support ft. (m) Vertical |
---|---|---|
½” (12) | 6 (1.8) | 6 (1.8) |
¾” (18) | 8 (2.4) | 6 (1.8) |
1” (25) | 8 (2.4) | 8 (2.4) |
1¼” (32) | 10 (3.0) | 8 (2.4) |
1½” (40) | 10 (3.0) | 8 (2.4) |
2” (50) and larger | 10 (3.0) | 10 (3.0) |
Joining methods
Medical gas piping may be joined using two distinct types of joints:
- Silver Brazed
- Axially swaged, elastic strain preload fittings
- Threaded
Brazed fittings shall be constructed from wrought copper, brass, or bronze complying with ASME B16.50 or ASME B16.22. They must be rated for the maximum pipeline pressure that could be encountered in the installation, testing, and service of the system.
Approved axially swaged, elastic strain preload fittings are used on CMT and create a permanent and non-separable connection. These fittings must be installed by qualified persons in accordance with the manufacture’s instructions.
Threaded joints ½” or less are used on main line gauges, zone valve gauges, alarm sensors, gas specific check valves and relief valves. Central supply source equipment and manifolds also use threaded connections. Joints shall be made up with approved Teflon tape or joint compounds rated for medical use that must not contain oil if used on oxygen systems. Joint sealant is applied to the male threads only, keeping the first three threads bare to prevent any compound from squeezing into the pipe. This type of joining method is only used in accessible locations for testing/ inspection and only to connect devices that cannot be brazed. The use of threaded joints should be minimized as they are more susceptible to leaking.
Cleaning and storing methods
The contractor who installs medical gas piping must take care to use only clean pipe. Since copper is used for many other applications, pipe that is cleaned specifically for medical purposes will be stamped accordingly. Each length of copper tubing or CMT shall be delivered plugged or capped by the manufacturer. On-site cleaning of medical gas piping shall not be permitted (Figure 30).
Special cleanliness requirements are called for because oxygen under pressure may cause the spontaneous combustion of some organic oils (the residual of lubricating oil used during manufacture) and for the safety of patients receiving medical gases. It is the responsibility of the installer to ensure they are using the proper type of piping material and that it meets with the cleaning requirements of the CSA Z7396.1 Standard.
Care must be taken when storing and handling piping material. The contractor should establish “clean areas” on the job site for storage. Material for use in a medical gas system should be stored separately from pipe and fittings use for water distribution and must be capped or plugged to prevent recontamination before final assembly. Immediately before final assembly, the material must be examined internally for contamination.
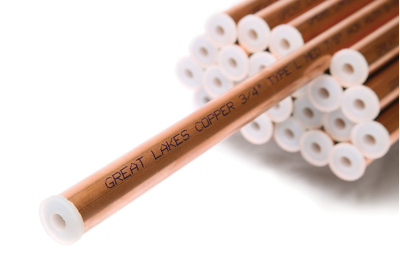
Degreasing
Copper tube used in medical gas systems typically arrives at the site degreased, capped and holding a nitrogen purge. Fittings used in the installation are also available cleaned and degreased from some manufacturers. Alternatively, on-site cleaning of fittings and hand tools can be accomplished by washing them in a hot solution of trisodium phosphate (TSP) or sodium carbonate. This solution is mixed at a rate of 40 g of cleaning material per litre of hot water.
The fittings or tools are scrubbed if necessary and rinsed in clean hot water. After cleaning, fittings and components are carefully stored or packaged to prevent recontamination until final installation is completed.
Capping
Medical gas copper tubing is available from the manufacturer degreased, oil-free and nitrogen purged. The manufacturer installs caps in the tube ends that fit snug to the tube’s ID surface and do not require any special tools to remove. The reason for the nitrogen purge is to prevent copper oxide from forming inside the tubing. Once the caps are removed and the tube is cut for installation, the nitrogen protection is lost. Oxygen in the air combines with copper to form cupric oxide.
This substance is often visible on the surface of the copper tube as a light to dark brown discoloration, even when in storage.
Cutting, fitting and brazing methods
All tools used for assembly of medical gas piping systems must be free of grease and oil before they are used. Reamers and cutters may be cleaned (degreased) on-site by washing them in a hot solution of trisodium phosphate (TSP) or sodium carbonate.
When fitting the piping system before joining, accurately measure the length of each tube segment required for the installation. Cut the tubing using a tube cutter and remove all inside and outside burrs with a reamer. If the joint is to be silver brazed, remove all oxides and surface soil from the tube ends and fitting hub using a nonshedding abrasive pad for a distance slightly more than the depth of the fitting hub. Clean the fitting hubs by the same method or use a properly sized stainless or brass fitting brush. The removal of oxides is crucial for the proper flow of brazing alloy into the joint to provide strength. If the joint is to be threaded, it must be made up with Teflon tape or other thread sealants suitable for oxygen service. Sealants shall be applied to the male threads only.
Medical gas systems require that during brazing, the system shall be continuously purged with oil-free dry nitrogen. The purge gas displaces oxygen from the interior of the tubing while it is being subjected to the high temperatures of brazing and therefore eliminates the possibility of oxide formation (oxidation) on the interior surface of the tube. The purge shall be maintained until the joint is cool to the touch.
When brazing onto the pigtails of valves and terminal units take care not to heat up the valve body. It is recommended to wrap the pigtails with a wet rag or heat block putty next to the valve to prevent overheating and possible damage to the valve seals.
The outside of all tubes, joints and fittings should be cleaned by washing with hot water after the brazing process to provide a clear visual inspection of brazed connections. The inspection body will inspect the entire system before validation. If the inspection body deems it necessary, they may randomly choose fittings to cut out and inspect the joints for interior oxidation and depth of penetration of the brazing alloy.
Purging requirements and procedures
All medical gas piping must be purged with dry nitrogen while brazing. At high brazing temperature a heavy black oxide scale forms (cupric oxide). On cooling, this oxide scale flakes off. While on the exterior of the tube this is mostly cosmetic, on the inside the oxide flakes are carried by the gases through the system. To prevent oxidation, establish a flow of dry nitrogen through the tube during brazing. Nitrogen is inert (non-reactive) and will displace the oxygen to prevent scale formation.
Nitrogen is typically introduced into the system through a hose adapter/fitting at the manifold location or other system opening such as a valve port. Connect a hose or tube from the fitting to the regulator or flow control valve on the nitrogen cylinder. There is no universal requirement for the delivery pressure setting, but the goal is to use low volume/ pressure to displace the oxygen. A suggested starting point is 10–15 CFH. Some users set pressure until they feel a slight flow at the exit point on the back of their hand. It’s good practice to initiate nitrogen flow before heating and to continue the flow until the joints have cooled.
Avoid an excessive flow rate that builds pressure inside the tube. A high flow rate will tend to cool the tube, reducing brazing heat efficiency. Excess nitrogen pressure can build up inside the tube and reduce braze alloy penetration. A small hole in a cap at the end of the line will allow the nitrogen to escape. Some installers prick a hole in a balloon and attach it to the open end of the pipe. The balloon inflates enough to show a visible pressure as nitrogen escapes through the now-enlarged pinhole.
Brazing material requirements and characteristics
All brazed joints in the piping must be made up using brazing filler metals that bond with the base metals being brazed and that comply with Specification for Brazing Filler Metal, ANSI/AWS A5.8, which states:
- Copper-to-copper joints shall be made using a copper-phosphorus brazing filler metal (BCuP series) without flux. The phosphorous within the BCuP brazing rod acts as the flux on all copper connections.
- Dissimilar metals such as copper and brass shall be joined using an appropriate flux with either a copper-phosphorus (BCuP series) or a silver (BAg series) brazing filler metal. Apply flux sparingly to the clean tube only and in a manner to avoid leaving any excess inside of completed joints.
Tools and equipment
During disassembly and reassembly of any equipment, procedures shall be followed to ensure tools and parts are kept clean and free of contamination in the form of dust, dirt, grease or oil. Always keep medical vacuum parts and positive pressure parts separated from each other. You as the installer should exercise great care in the storage and handling of tools used in cutting and reaming to prevent oil, grease or other contaminants from being introduced into tubing during assembly. Ladders, scaffolds and personal protective equipment must be selected and checked for serviceability in accordance with WorkSafeBC guidelines.
Coordination with other trades
Coordination and communication early on with other trades is key to the success of any project to assure timely installations and to avoid conflicts and interference. Due to the complexity of medical facility installations, there are always space limitations in the ceiling that affect the ventilation, electrical and sprinkler systems. The installer must be able to coordinate work with other trades to accommodate actual architectural, structural and site conditions. Some of the typical coordination requirements are as follows:
- Coordinate with the metal stud partition installer and/or mason to ensure anchors, sleeves and similar items are provided in sufficient time to avoid delays. Ensure that chases and openings are properly sized and prepared.
- Coordinate with the owner to ensure medical gas outlets, whether owner supplied or contractor supplied, in walls, ceilings and all equipment are provided by the same medical gas equipment manufacturer (MGEM) and are satisfactory to the owner.
- Coordinate with the bulk cryogenic gas supplier for installation, connection and verification of bulk gas supply systems.
- Coordinate with the medical gas verifier (or inspector) to deliver a complete, tested medical gas installation ready for the owner’s use.
Pipe and component labelling
Medical gas piping, including all intakes, exhausts and vents, must be clearly identified using non-removable stickers that are colour coded to specify the gas it conveys. Colours are standardized according to the CSA Z7396.1 Standard (Figure 31).
Gas or gas mixture | Symbol | Background colours | Lettering |
---|---|---|---|
Medical air | MedAir | Half black – half white | Half black – half white |
Carbon dioxide | CO2 | Grey | White or black |
Helium | He | Brown | White |
Nitrogen | N2 | Black | White |
Oxygen | O2 | White | Green |
Nitrous oxide | N2O | Blue | White |
Medical – surgical | MedVac | Yellow | Black |
Anaesthetic gas scavenging system | AGSS | Magenta | White |
Labels (Figure 32) must be spaced along the pipe no more than 6 m (20 ft.) apart and also at:
- every valve
- each access door
- each terminal unit
- immediately before and after barriers
- inlet and outlet points
The label must:
- be lettered and coloured in accordance with Table 5 in the CSA Z7396.1 Standard
- have lettering at least 9 mm (3/8″) high
- have arrows indicating direction of flow
- be applied with the lettering parallel to the axis of the pipe
- be of sufficient width to overlap itself when applied
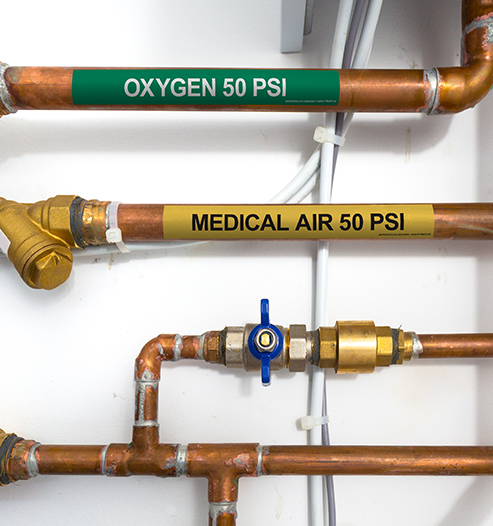
When a large medical gas system is being installed, several different gases may be piped into an area, all running beside each other. This installation will have numerous branch lines connected to the main pipe. These branches will then split and go to various rooms or departments, which will involve using tees, elbows, etc. It is sometimes confusing which line is intended for which gas, especially since they may not be labelled for a short period of time at the location where the work is being done. It is critical that installers use good piping practices to recognize and eliminate cross-connections before the system is tested. Sentence 10.3 of the CSA Z7396.1 Standard states: “Labels shall be placed on the piping, including all intakes, exhausts and vents, as each is installed.”
Dangers associated with cross-connection
The installation, use and verification of medical gas pipeline systems are governed by the CSA Z7396.1 Standard. The driver behind the development of the Standard was to address a fatality that occurred when a patient was being treated for a non-life-threatening condition. It was discovered that a cross-connection between the oxygen and nitrous oxide pipelines supplied the patient with 100% nitrous oxide, which does not sustain human respiration.
CSA Z7396.1 Standard contains significant steps to ensure that a dedicated pipeline is not conveying the wrong gas due to a cross-connection. The Standard prescribes different procedures that must be followed to validate gas-specificity of the pipeline and certify that no two pipelines of different medical gases have been mistakenly cross-connected. These tests and verifications must be completed following any repair, maintenance or modification of a medical gas system.
Now complete Self-Test 3 and check your answers.
Self-Test 3
Self-Test 3
Media Attributions
- Figure 28. “Corrugated copper alloy tube and permanent fitting system” from Purely Med Gas is used for educational purposes under the basis of fair dealing.
- Figure 30. “ACR med nitrogen-filled degreased medical gas tubing” from Descair is used for educational purposes under the basis of fair dealing.
- Figure 32. “Medical gas pipe labels” from DuraLabel is used for educational purposes under the basis of fair dealing.