Learning Task 1: Employment Trends
Click play on the following audio player to listen along as you read this section.
Being informed about the trends that are transforming employment and the workplace will give you a greater understanding of the labour market and what you need to find employment.
The working world has undergone significant changes in the past two generations. Fifty years ago, most working individuals had a single employer or worked in one occupation for the majority of their lives. Smaller towns or cities revolved around one or two major employers in a specific industry. By the 1980s, most of our parents’ generation had transitioned through recessions, elimination of jobs in the public and private sector, downsizing of industries, and the movement of jobs overseas. Over the past decade, we’ve seen the adoption of digital (computer) technologies spread throughout the working world and in all facets of manufacturing and machinery. This has led to rapid change in the workplace and a need for employers and employees to be ready to adapt to further changes.
Most individuals entering the job market in the 21st century will work for multiple employers and in a number of sectors over the course of their time in the labour force. With almost every industry adopting digital technologies, workers will be required to learn new skills and adapt to an ever-changing workforce. Many will work in more than one sector of employment, and most of the work available, particularly in the trades, will be on contract or project based. More individuals will be self-employed and need the skill sets to manage their own small business.
The three major trends affecting the Canadian and British Columbia economies in 2015 were:
- increased competition within global markets
- a shortage of workers with specific credentials
- a skills gap
In 2014, the Conference Board of Canada released a report titled “Skills for Success: Developing Skills for a Prosperous B.C.” In this report it was noted that skills gaps cost the B.C. economy approximately $4.7 billion annually in gross domestic product (GDP) and an additional $616 million in provincial tax revenue (Stuckey and Munro, 2014). According to the report:
For B.C. to sustain its economy, pursue new opportunities, and achieve its full economic potential, not only will it require an educated and highly skilled workforce to meet near- to medium-term needs, but also one that has the ability to adapt to changing economic and social circumstances and opportunities (Stuckey and Munro, 2014, p. 2).
Over one-third of the Canadian employers surveyed for the report indicated a need for employees with trades qualifications and credentials, with the highest demands for millwrights, heavy-duty equipment mechanics, welders, and industrial electricians (Stuckey and Munro, 2014).
Employers also expressed concern about the insufficient essential skills of recent graduates and potential employees, with the greatest weaknesses noted in critical thinking and problem solving (73%), oral communication (38%), literacy (36%), and working with others (33%) (Stuckey and Munro, 2014). Similar data exists for other Canadian provinces as well. For example, in Ontario it is estimated that insufficient essential skills cost the province $24.3 billion in GDP annually. Through extensive research over the past two decades in numerous post-industrialized countries, there is evidence to show a direct correlation between a company’s productivity and the essential skills of employees.
Labour Market Projections
The job of predicting changes in the labour market is performed by a number of different organizations and individuals, including the federal and provincial governments, banks, business associations (such as local chambers of commerce), academics, and private think tanks. These predictions are used for different purposes. For example, because of Canada’s aging population and low birth rate, it has become increasingly important for the federal and provincial governments to forecast the number of workers that will be needed in the short term and long term in different occupations in order to replace workers lost through attrition (loss of skilled workers due to retirement and other reasons), and to project areas of growth in the economy that require additional workers.
These forecasts are used by the public and education sectors to determine where there will be skills shortages and need for more training. In cases where specific jobs are becoming obsolete, these projections help in plans for retraining employees to work in other sectors of the economy. Where the demand for skilled workers cannot be met, either within British Columbia or Canada as a whole, these projections are also integral to determining changes to the country’s immigration policies.
The following reports on the WorkBC website may help you gain a better understanding of British Columbia’s labour market:
- British Columbia Labour Market Outlook 2022
- High Opportunity Occupations in British Columbia
- Trade Occupations Outlook
While you are on the WorkBC website, take the opportunity to explore it in detail. You’ll find information that is regularly updated on the labour market forecasts by province, region, and occupation. The site also offers a “Blueprint Builder,” which provides you with all the information you will need to explore careers both in the trades and other fields, as well as information on jobs currently available: WorkBC
Global Marketplace, Technology, and Environmental Concerns
We now live in a global economy in which very few products are fully developed, manufactured, and assembled in a single country. Components for most manufactured goods originate from a number of different companies, and products may be assembled anywhere in the world. For example, a car made in Canada may have over 50% of its components manufactured in other countries. Customer service may be provided thousands of miles away from the location of a company or its customer base. The ability to compete on a global scale is integral to Canada’s economic future.
According to the Conference Board of Canada’s report “Innovation and Technology—Increasing Canadian Competitiveness” (Preston, 2015), 99.9% of all Canadian companies are small- to medium-sized enterprises (SMEs) with fewer than 500 employees. These companies employ approximately 90% of all individuals in the Canadian private sector. The adoption of digital technologies by SMEs in Canada is key to becoming more competitive internationally.
Depending on what trade you are in, you may be required to learn about and use new technologies and materials on a regular basis. You may also have to look for solutions for retrofitting , upgrading, and servicing older equipment that is no longer being manufactured. Many of the newer technologies being adopted will be more energy efficient and environmentally sustainable in response to changes in government legislation and a growing public awareness of the effects of pollution locally, nationally, and globally. These factors can trigger changes to building codes and practices and procedures in your industry. The ability to be informed and adapt to the changes are part of continuous learning, one of the nine essential skills desired by employers. These skills are described below.
Changing Organizational Structures and Diversity in the Workplace
The retirement of baby boomers (individuals born between 1945 and1960) over the next few decades will result in significant shortages of skilled labour not only in Canada, but in most advanced economies around the world. Millions of baby boomers will retire in the next 15 years. Coupled with a low birth rate, this will present significant challenges and opportunities.
Canada continues to diversify its industry by finding more skilled labour in underrepresented groups; including women, Indigenous peoples and landed immigrants. These underrepresented groups represent a previously untapped resource in the skilled trades. People that fall into one or more of these groups may face challenges in finding employment in the skilled trades due to biases and stereotypes that exist. The increased discrimination of people that identify with multiple underrepresented groups is often referred to as intersectionality. Several initiatives are in place to encourage these groups to pursue a career in the trades to help offset the labour shortage.
Women represent greater than 50% of Canada’s population, but according to a 2020 report by the Canadian Apprenticeship Forum (CAF-FCA), make up less than 5% of the skilled trades workforce. This number has only increased marginally over the last decade and with the impending labour shortage it is important to increase representation of women in the skilled trades to help address this. Women have a long history of stepping into skilled trades positions, which is exampled by their work during World War II, which saw women take on roles such as producing munitions, building ships and airplanes, in engineering, and in the metal and shipbuilding industries, as welders, riveters and more. Stereotypes and myths still exist today that deter women from entering the skilled trades, fewer young women are presented the trades as a career option than young men. These misconceptions will have a dire effect on the labour market in the future if they are not addressed, as the exclusion of a large pool of the population makes filling skilled labour positions more challenging.
Indigenous peoples in Canada are also an underrepresented group in our skilled trades workforce. According to a 2019 report entitled “Promoting Careers in the Skilled Trades to Indigenous Youth in Canada” by the Canadian Apprenticeship Forum (CAF-FCA), there is a lack of awareness of the skilled trades as a career among Indigenous youth. Surveyed respondents indicated that barriers to access of shop classes, mentorship by Indigenous journeypersons and unwelcoming institutions and workplaces were also reasons for Indigenous peoples to not pursue a career in the skilled trades. This lack of promotion and inclusivity also limits the opportunity to increase the skilled trades workforce with Canadian workers.
According to Statistics Canada (2011), as of 2012, 20.6% of Canada’s population was born outside of Canada. As of 2031 (Statistics Canada, 2010) this percentage is expected to increase to 25% to 28%. Among the challenges to be addressed are greater cultural diversity in the workplace, greater gender diversity in the workplace, recognition of prior learning experiences and credentials from other countries, and English language acquisition.
As part of increased workplace diversity to meet labour shortages, industry also needs to consider the meaning and implementation of equity in operational and hiring practices. Equity is a term that is often confused with equality, it is important to understand the difference between these two terms and how they apply to the success of a diverse workforce. Equality is giving everyone the same thing regardless of their needs, whereas equity is giving each person the supports they require to be successful. As work is done towards diversifying workplaces, there is a need to ensure that employees have the tools that they need to become successful members of the team. Consider the following: a public library is located at the top of a large steep staircase; in order to access the library everyone must climb the stairs, there are no other options for access; this is an example of equality as the library is accessible to everyone in the same way.
This example of equality alienates several groups of people from accessing the library, including those in wheelchairs, people with strollers, small children, and those with other physical limitations. To make this equitable an alternative means of access to the library would be required, such as an elevator or a ramp, so that everyone has the opportunity to access the library if they choose to. This is an important consideration when looking at workplace diversity. To achieve true diversity in the workplace, employers will ultimately be faced with unique needs and barriers amongst employees. Implementing equitable hiring practices, such as blind hiring or panel hiring can help create a sense of fairness in the hiring process. Equity policies in the workplace ensure that all employees have access to the supports that they require to be successful, whether those are assistive technologies, flexible hours to accommodate childcare, provision of a company vehicle, extra training, physical assistance, or other supports. Ensuring that everyone in the workplace is provided what they need to achieve success means better morale, job satisfaction and more effective problem solving from a diverse pool of perspectives and experiences.
Many of the individuals leaving the workforce will be in senior leadership and middle management positions, which will open new opportunities for individuals to move up in organizations provided they have acquired the necessary skills. For example, individuals with an interprovincial Red Seal who have management training and supervisory experience are excellent candidates to move into management positions. There will also be many openings for qualified trades instructors.
Take the time to explore your intended trade and some of the additional career paths that will be available to you with additional training. This can help you begin to develop ideas for your own personal learning plan. It is also important to identify any barriers that you may face during your training and what supports or strategies you will employ to overcome these. Accessing necessary supports early on in your learning will help you to achieve greater educational successes. The creation of a three- to five-year learning plan is standard practice in companies that are looking for employees to move up in the organization. It is also an activity that you can do for yourself as part of continuous learning.
Focus On Essential Skills
The Government of Canada, along with many post-industrialized nations around the world, has invested significant time and money to conduct research and develop tools, assessments, and training supports to assist employers and employees in understanding essential skills and their importance to productivity. For example, research shows that there is a correlation between the skill levels of employees and a company’s productivity. The Industry Training Authority of British Columbia cites that apprentices with the necessary essential skills for their profession are up to “eight times more likely to pass your technical exams” (see ITA BC Essential Skills).
The following nine essential skills are recognized by the Government of Canada as the foundation for learning all other skills and are integral to an employee’s ability adapt to workplace change and acquire new knowledge. The nine essential skills are listed below, and a short video for each provides you with an overview of the skill.
1. Reading
Reading is the ability to understand reading materials that are in the form of sentences and paragraphs. This skill is used to scan for information, skim overall meaning, evaluate what you read, and integrate information from multiple sources.
Watch this video: Essential Skills: Reading Text (40 seconds)
https://www.youtube.com/watch?v=RYv0dv_l5RA
Essential Skills: Reading Text – Transcript (Provided for accessibility, not openly licensed.)
[Upbeat music]
Narrator: Reading text is how we make meaning from paragraphs and sentences. It’s how we understand instruction in the written form. Whether you closely follow written instructions or skim for reference, when you evaluate and integrate information from multiple sources, that is the ability to read text. It’s recognizing specifications and regulations within journals and manuals. It’s understanding instructions. Essentials skills: The foundation for work, learning, and life.
2. Writing
Writing is the ability to write text and documents by hand or typing or computer. This skill is used to organize, record, document, persuade, justify, or request information.
Watch this video: Essential Skills: Writing (35 seconds)
Essential Skills: Writing – Transcript (Provided for accessibility, not openly licensed.)
[Upbeat music]
Narrator: Writing is how we communicate with text on paper or on screen. It organizes and documents information to persuade and inform. When you convey a message via text, write down a diagnosis on paper, make a request or provide an explanation via email, that is writing. It’s projecting your message or ideas without speaking. Essentials skills: The foundation for work, learning, and life.
3. Document Use
Document use is the ability to perform tasks that include words, numbers, symbols, and other visual characteristics. These items are given meaning based on their special relationship. Graphs, lists, tables, blueprints, schematics, drawings, signs, and labels are documents used in the world of work.
Watch this video: Essential Skills: Document Use (37 seconds)
Essential Skills: Document Use – Transcript (Provided for accessibility, not openly licensed.)
[Upbeat music]
Narrator: Document use is how a collection of displayed information is interpreted. It is the combination of words, charts, labels, and colours that we can create meaning out of. When you read or interpret graphs, that is document use. When you review blueprints and schematics, that is document use. It is how we take meaning from visual characteristics and spacial arrangements. Essentials skills: The foundation for work, learning, and life.
4. Numeracy
Numeracy is the ability to use numbers and think in quantitative terms. You use this skill to do numerical estimating, money math, scheduling or budgeting math, and analyzing measurements or data.
Watch this video: Essential Skills: Numeracy (29 seconds)
Essential Skills: Numeracy – Transcript (Provided for accessibility, not openly licensed.)
[Upbeat music]
Narrator: Numeracy is how we use numbers. It’s thinking mathematically. It’s thinking quantitatively. When you take a measurement, you work with numeracy. It’s practical and analytical. It’s fundamental, and it’s highly technical. Essentials skills: The foundation for work, learning, and life.
5. Digital Skills
Digital skills (formerly computer use) is the ability to use different kinds of computer or smart phone applications and technical tools. This includes using cash registers, word processing software, sending emails, using social media, or modifying spreadsheets.
Watch this video: Essential Skills: Digital (50 seconds)
Essential Skills: Digital – Transcript (Provided for accessibility, not openly licensed.)
[Upbeat music]
Narrator: Digital skills are how we work with modern technology. They are essential to use digital systems, technical tools, and applications. It’s imputing data, measuring variables, and calibrating systems. It’s analyzing and organizing information on digital devices. When you use a cell phone, a computer, a CNC machine. It’s word processing, software, spreadsheets, email, the web. It’s a vital component of communication and manufacturing. It’s being able to understand and process information from digital sources. Essentials skills: The foundation for work, learning, and life.
6. Thinking
Thinking is the ability to process information and evaluate ideas to come to a decision. This skill is used for problem solving, making decisions, thinking critically, and planning and organizing job tasks.
Watch this video: Essential Skills: Thinking (35 seconds)
Essential Skills: Thinking – Transcript (Provided for accessibility, not openly licensed.)
[Upbeat music]
Narrator: Thinking is how we evaluate ideas to make informed decisions. It’s using our memories and experience to work efficiently and effectively. It’s task planning, organizing, problem solving. It’s rational and critical thought. It’s the core of everything we do. Essentials skills: The foundation for work, learning, and life.
7. Oral Communication
Oral communication is the ability to use speech to give and exchange thoughts and information. You use this skill to give and exchange ideas and information and to resolve conflicts.
Watch this video: Essential Skills: Oral Communication (30 seconds)
Essential Skills: Oral Communication – Transcript (Provided for accessibility, not openly licensed.)
[Upbeat music]
Narrator: Oral communication is how we use speech to exchange information. It’s how we share ideas. It’s also how we understand others. It’s listening. When you greet people or take messages, that is oral communication. Essentials skills: The foundation for work, learning, and life.
8. Working with Others
Working with others is the ability to carry out tasks as a member of a team or in a leadership or supervisory role.
Watch these videos:
Essential Skills: Working with Others (28 seconds)
Essential Skills: Working with Others – Transcript (Provided for accessibility, not openly licensed.)
[Upbeat music]
Narrator: Working with others is how we operate in a partnership or as a team. Carrying out a task together requires the engagement of all participants. Whether you are the leader or part of the team, being able to work with others is vital for getting the job done. Essentials skills: The foundation for work, learning, and life.
Working with Others: An Essential Skill (1.5 minutes)
Working with Others: An Essential Skill – Transcript (Provided for accessibility, not openly licensed.)
[Upbeat music]
Narrator: Working with others: An essential skill. What could you do today? You’re full of dreams. There’s no stopping you. The world is your oyster. But you can’t do it alone; you need help: a whole stew of people to sweeten the pot, to stir the juices. But throw a dinner rush into the mix, and you could have a recipe for disaster. Fortunately, there are things you can do to help: Recognize strengths and attributes, identified leadership, an established workflow. Don’t forget to encourage participation, because a little collaboration gets everyone on the same page. Working with others is an essential skill, and it’s a learned one. Find out how you can cook up a smoother workplace to make your job easy as pie. Literacy Alberta: Essential skills for an evolving world. What could you learn today?
9. Continuous Learning
Continuous learning is the ability to participate in acquiring new skills and knowledge. This can be part of your regular work or through additional training on- or off site.
Watch this video: Essential Skills: Continuous Learning (36 seconds)
Essential Skills: Continuous Learning – Transcript (Provided for accessibility, not openly licensed.)
[Upbeat music]
Narrator: Continuous learning is how we learn on the job and offsite. It is part of the regular routine, upgrading out skills as the world and technology evolves. When your coworker teaches you something new, that is continuous learning. It’s using past experience to do the job better. That is continuous learning. It’s how we grow. Essentials skills: The foundation for work, learning, and life.
The video at the following link provides a first-hand account from two employers on the importance of essential skills to their company’s success.
Watch this video: Worth the Investment (7 minutes)
Worth the Investment – Transcript (Provided for accessibility, not openly licensed.)
[Upbeat music]
Narrator: Reading text, document use, numeracy, writing, oral communication, working with others, continuous learning, thinking skills, computer use. Essential Skills: Worth the Investment.
On a country road in winter. Cambridge, Nova Scotia.
Jack Thompson: Dave Brown’s has a fleet of 42 trucks. We have drivers on the road 24 hours, 7 days a week. To be truck driver, you have to have the three basic skills: reading, writing, and arithmetic, okay? And if you don’t have that, okay, you’re not going to survive in the trucking industry. You must update these essential skills, because with today’s regulations, you have to write information in a book. When you’re dealing with customers, you have to count freight. You have to be able to read bill [inaudible], because all of that will affect what we do as a business. The new technology coming in has forced us to upgrade our fleet and our systems in order to stay competitive in the industry and maintain our market share and be profitable.
Narrator: Between 2004-2006, nearly 43% of private sector firms introduced improved technologies into their business.
Lettering on a building that read, “All Weather Windows.” Edmonton, Alberta.
Onkar Athwal: We are at All Weather Windows’s head office and manufacturing facility in Edmonton, Alberta. We manufacture doors and windows. One of our key objectives in moving forward as a company is to ensure that all of our employees have all of the skills necessary to preform all of their jobs at their maximum potential.
Jason Flemming: We have a lot of interaction with manual labour. There is no way that one is taking away from the other. And that the skills that people need, even if they are doing manual labour, it still requires them to be able to read, interpret data, use documents that have been generated through some of these processes, whether it’s from our oracle systems, our ERP. And then they have to then interpret that information and then apply it what they are doing on the job.
Onkar Athwal: If you want to succeed in business, you have to invest in your employees. And it’s not a one-time investment. It’s a constant investment. And you will reap the benefits ten times over.
Narrator: Every 10% increase in the number of employees using computers increases productivity by 1.3%.
Letters on the side of a building that read, “Willow Printing Group.” Concord, Ontario.
Jeff Ekstein: Digital technology and the skills that people require has impacted the print industry and our business drastically. Today, having to be literate, to be able to put the information required to keep our business running is crucial. Our number one asset is people. If we don’t train them in today’s standards, we will be out of business. So it’s important to ensure that people understand the changes in technology and what we need to do as a company to stay ahead of the curve.
Narrator: In 2009, Canadians used the Internet to place orders for goods and services valued at $15.1 billion dollars.
Outside an industrial building, CL Malach. Winnipeg, Manitoba.
Phillip Portelance: CL Malach is a sheet metal fabrication shop. We take raw material sheet. We can laser cut it, we can sheer punch it, we can break it, weld it, and paint it all onsite. Over the last couple years, the processes and the procedures have changed. We’ve had our database system to work with the equipment that we have on the plant floor. So that has changed not only some of the duties and responsibilities of specific employees, but other procedures that they need to follow, such as barcoding in and out of jobs to give us more transparency as to where a particular job is at in the plant. We know that there is a lot of employees that, over years, are able to learn how to function even if their essential skills are lacking. And they can even mask that at times. So we’ve been able to identify certain employees, and now we are going to provide them training that is going to help them not just here at work, but also at home. It’s going to improve our bottom line, and it will allow the employees to be more successful.
Narrator: 89% of small and medium enterprises indicate that technological change is at the forefront of issues impacting Canada’s economy in the next 10 to 20 years.
Elmsdale, Nova Scotia.
Roy McNeill: Don McNeil Shell is a 2nd generation service repair facility. Most of us here have a grade 12 education, and you’ve always been able to get through with and find your way. But things have changed so fast so rapidly. I think the biggest change is we’re used to just going to the [inaudible] and saying, “Yes, that’s close enough.” But the specs on the newer vehicles, it’s really important to know exactly what the tolerances are. So now we can go online in real time and find out exactly what they are supposed to be. We have one technician who has been here since ’77. He’s got over 34 years with us.
Man with grey hair: It’s just amazing how things have changed. Years ago, I looked everything up in a book. Nowadays you have to look everything up on the computer. If I wanted to stay in this trade, I had to learn.
Roy McNeill: Things have changed so fast so rapidly. We have no choice. We can’t ignore it.
Narrator: Small firms with a high level of web connectivity see their revenues rise 2.25 times faster than firms with no connectivity.
Calgary, Alberta.
John Simpson: Standen’s Ltd is a manufacturer of alloy steel products for the automotive, heavy-truck industry. At the end of the day, if you don’t work with your employees to try to help them get better at what they do, you’re going to sit still, you’re going to move backwards. Your competition is always trying to get better. And competition today is global, it’s not local. So you have to try to improve continuously and improve throughout your organization. So giving people the skills they need to do that is critical. And having the ability to identify people who are struggling with some of the core, essential skills is equally important because if they are not able to learn the basics, how can they learn the more advanced things that you’re teaching them. For our business, we find helping them with their essential skills helps us grow and be a better company.
Roy McNeill: Essential skills are essential to my business.
Jack Thompson: Digital technology in our trucks demands a skill to work for. Without it, we wouldn’t be able to stay competitive.
Jeff Ekstein: Investment in essential skills is an investment in my buiness.
Jason Flemming: Without reading, writing, basic math skills, our employees would not be able to meet the demands of new technology.
Phillip Portelance: Digital technology is everywhere. We need to make sure our employees are ready.
John Simpson: By training our employees with essential skills, we have made sure that our company is prepared for the future of digital technology. It is absolutely worth it.
Narrator: To learn more about the advantages of essential and digital skills for your employees, contact the Office of Literacy and Essential Skills or visit [website that is no longer active].
Canada’s National Occupational Analysis (NOA)
Part of the essential skills project in Canada was the creation of an essential skills profile for each occupation in Canada. The basis of the profile is Canada’s National Occupational Analysis (NOA), something that you can learn more about in Competency B-4, Describe the Apprenticeship System. The profile lists all of the major tasks performed for an occupation categorized by essential skill. It also indicates the level of complexity required to perform this task, with (1) being the most basic and (5) the most complex. To understand how levels of complexity are determined for each essential skill, visit the Readers’ Guide to Essential Skills Profiles.
On the following pages is an example of the essential skills profile for plumbers (National Occupational Classification #7251). Look over this document and you will notice that the level of complexity (in parentheses) for most tasks is (3) or below. This is the case for almost all occupations. You’ll also notice that the sections “Working with Others,” “Continuous Learning,” and “Impact of Digital Technologies” do not use the ranking system and instead provide a description of how each skill is used in the occupation.
Once you have had a chance to read the profile, ask yourself this question: Do you think that this information provides you with a better understanding of the essential skills you would need if you were to become a plumber?
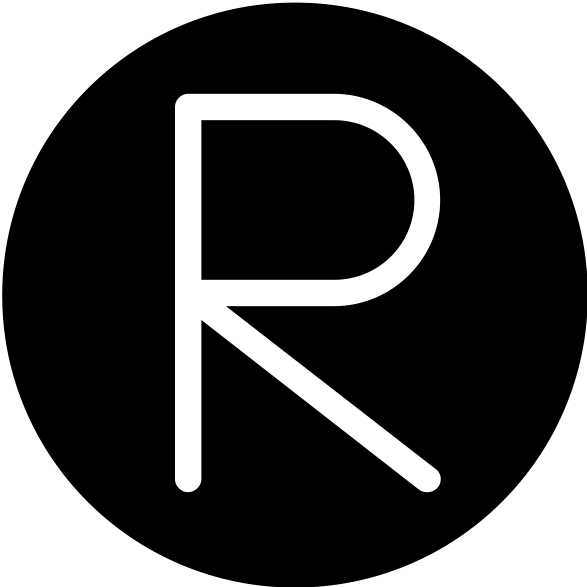
Essential Skills Profile – Plumbers (NOC 7251)
Plumbers install, repair and maintain pipes, fixtures and other plumbing equipment used for water distribution and wastewater disposal in residential, commercial and industrial buildings.
Reading
- Read short text entries on forms, such as work orders and log books. (1)
- Read bulletins and notices, e.g. read bulletins to learn about changes to operating procedures and read notices to learn about product recalls. (2)
- Read workplace safety materials, e.g. read Material Safety Data Sheets (MSDS) to understand the chemical composition of products and possible hazards. (2)
- Read a variety of installation procedures, e.g. read manufacturers’ instructions when installing new plumbing fixtures. (2)
- May read magazine and website articles to stay current on industry trends and broaden their knowledge of plumbing techniques and materials. (3)
- Read occupational health and safety standards, e.g. read rules to learn how to work safely in confined spaces. (3)
- Read a variety of manuals to learn how to install, repair and maintain plumbing fixtures and systems. (3)
- Read trade textbooks, e.g. read textbooks to understand the acceptable use of materials and science related to plumbing, such as the properties of water, metals and alloys. (4)
- Read the Canadian Plumbing Code to learn the regulations that govern the design, construction, extension, alteration, renewal or repair of plumbing systems. (4)
Document Use
- Observe hazard and safety icons, e.g. scan icons affixed to products, such as flux-core solders, to learn about their toxic properties. (1)
- Enter and locate data, such as dates and identification numbers, in labels and tags. (1)
- Complete a variety of checklists and forms, e.g. complete hazard assessment forms and purchase orders by checking boxes and entering data, such as dates, times and quantities. (2)
- Study a variety of assembly drawings, e.g. study assembly drawings to learn how to install fixtures and appliances. (2)
- Locate data in a variety of complex tables, e.g. locate data, such as dimensions, classifications, tolerances, coefficients, identification numbers and quantities, in specification tables. (3)
- Interpret a variety of construction drawings, e.g. scan construction drawings to learn how plumbing, electrical, carpentry and mechanical installations are to coordinate. (4)
- Interpret a variety of complex schematic drawings, e.g. scan schematics to locate circuits, flows and capacities when planning for complex plumbing installations of piping. (4)
Writing
- Write reminders and short notes to customers and co-workers, e.g. write short notes to inform supervisors about repairs in-progress and tasks to be completed. (1)
- Write short comments in forms and logbooks, e.g. write comments in order forms to specify part requirements. (1)
- May describe project details on estimate sheets and work orders, e.g. explain the plumbing tasks to be performed on job estimates. (2)
- May write reports to describe events leading up to workplace accidents, e.g. write about injuries and events when completing reports for workers’ compensation boards. (2)
Numeracy
- May receive cash, debit and credit card payments and make change. (1)
- Take a variety of measurements using basic tools, e.g. measure the lengths and diameters of pipes using tape measures. (1)
- Compare measurements to specifications, e.g. compare pressure gauge readings to required manufacturers’ standards. (1)
- May approve payment for invoices submitted by suppliers, verifying the accuracy of the charges for parts ordered and received. (2)
- May schedule the completion of complex plumbing projects by considering project tasks, lead times and the availability of labour and parts. (2)
- Use formulae, e.g. use formulae to calculate the total falls on drain lines. (2)
- Calculate material requirements, e.g. calculate the amount of material, such as valves, connectors and piping, needed to complete projects. (2)
- Calculate averages from sets of readings to determine if humidity, temperature and water pressure are within levels recommended by manufacturers. (2)
- May estimate the material requirements for projects. They consider project scopes and the materials needed for similar jobs in the past. (2)
- Estimate the length of time it will take to complete projects. They consider projects and the availability of materials and labour. (2)
- May calculate amounts for estimates and invoices. They multiply hours worked by labour rates and add amounts for materials, supplies and applicable taxes. (3)
- Calculate loads, e.g. calculate the total hydraulic loads on sanitary drainage systems using Canadian Plumbing Code conversion factors and variables, such as fixture units. (3)
- Analyze multiple pressure readings to evaluate plumbing system functions and troubleshoot faults, e.g. compare measurements of pressure to calculated or predicted values at various points in a system to identify the location of leaks. (3)
- Calculate rolling offsets to design, fabricate and install piping around obstacles. (4)
Oral Communication
- Speak with suppliers to learn about products, prices and delivery schedules. (1)
- Discuss specifications, timelines, procedures, expectations and other work-related matters with co-workers and other tradespeople, e.g. speak with forepersons about job assignments and with other tradespeople to co-ordinate activities and schedules. (2)
- May talk to customers to respond to questions and complaints, gather information about needed repairs, explain plumbing procedures and discuss the results of inspections and repairs. (2)
- Talk to building inspectors, engineers, and architects, e.g. speak with Technical Standards and Safety Authority (TSSA) representatives about system certification requirements. (2)
- May provide detailed step-by-step instructions to apprentices, customers and other tradespeople, e.g. explain to apprentices the steps to install water heaters. (3)
Thinking
- Encounter delays due to equipment breakdowns and shortages of materials. They inform others about the delays and perform other work until repairs are completed and needed materials arrive. (1)
- Miss deadlines when tasks extend beyond time estimates for completion. They may consult with their supervisors and customers to reschedule work and work overtime as required. (1)
- Decide order of tasks and their priorities, e.g. decide the order in which to install fixtures and test systems. (2)
- Choose tools, methods and products for plumbing installations and repairs, e.g. consider project scopes and the availability of materials and labour. (2)
- Evaluate the safety of work sites. They consider the hazards of working from heights and in confined spaces. (2)
- Evaluate the preparedness of job sites for plumbing installations. They consider the adequacy of access to work areas and protection from inclement weather. (2)
- Clarify installation procedures by referring to the Canadian Plumbing Code and job specification books and by talking to mechanical engineers, suppliers and manufacturers. (2)
- Locate information on plumbing products and fixtures by conducting Web research and by reading catalogues issued by suppliers. (2)
- Refer to schematics and speak with general contractors to locate system components, such as gas flow shut-off valves. (2)
- Refer to trade, provincial and national code books to ensure installations and repairs are compliant with industry standards for plumbing and heating systems. (2)
- Face disruptions of work schedules, timelines and budgets when project designs are found to be faulty and when specifications change after projects have already started. They assist in the development of new designs and perform other work until the project starts. (3)
- May select materials and suppliers, e.g. decide which brand and type of materials to use by considering specifications, warranties, costs and ease of use. (3)
- Assess the quality of plumbing installations and repairs. They take measurements, observe the appearance of joints and check for signs of leaks. (3)
- Plan their work in conjunction with forepersons, supervisors and other tradespeople on the job. Time pressures may become intense and interruptions from others result in frequent stops and starts. They reprioritize their tasks to accommodate emergencies and make adjustments to project timelines. Job task planning and organizing differs according to the work context.
- In the case of residential service appointments, there may be 10 to 15 service calls in one shift. Planning and organizing must take into account the distance between customer locations and the urgency of specific calls. When working on new construction projects, job task planning and organizing is geared towards fitting smoothly into a schedule that involves other trades coming before and after them. Plumbers work both independently and in co-operation with other tradespeople on job sites. (3)
Digital Technology
- Use calculators and personal digital assistant (PDA) devices to complete numeracy-related tasks, such as calculating material requirements. (1)
- May use word processing software to write letters to customers and prepare job estimates and invoices. (2)
- May use spreadsheet software to tally costs for job estimates and invoices. (2)
- May use billing and accounting software to input and track sales, produce invoices and estimates and print reports, such as income and expense statements. (2)
- May use communication software to exchange email with customers, suppliers and co- workers. (2)
- May use computer-assisted design (CAD) software to access, modify and print technical drawings. (2)
- May use databases to enter and retrieve project information. (2)
- May use databases to retrieve and print scale and assembly diagrams. (2)
- May use the Internet to access training courses and seminars offered by apprenticeship trainers, associations, unions, suppliers and employers. (2)
- May use Internet browsers and search engines to access technical service bulletins, plumbing codes, specifications and troubleshooting guides. (2)
- May use online plumbing software to streamline their scheduling, dispatching and routing activities. (2)
- May use project management software for complex equipment installations to schedule lead times and the completion of project milestones. (3)
Additional Information
Working with Others
The degree to which plumbers work with others depends on the specific setting in which they work. On construction sites, plumbers must co-ordinate with other trades onsite as there is an order in which the work should be performed, and safety is always a concern. For example, during installation they complete the rough in and then return to complete the finishing after other trades (e.g., plasterers, tilesetters) have completed their work. Plumbers frequently work with an apprentice and are asked to provide mentorship to these apprentices as they continue to learn the trade. Plumbers servicing residential clients typically work with other trades to a lesser extent. They often work alone on small residential jobs, however, do engage more with their customers than those on construction sites.
Continuous Learning
Although the fundamentals of plumbing remain constant, the nature of the plumbing occupation is changing, resulting in a corresponding need for continuous learning. For example, changes to the Canadian Plumbing Code periodically modify procedures for the installation of piping systems. Advances in technology are also having a significant impact on trade procedures. For example, the use of computer-assisted design (CAD) software is required in some jurisdictions. Advances in technology are also changing the design, applications and materials of systems. Technical courses may be offered when new products, procedures and equipment are introduced.
Apprentices learn through a combination of classroom training delivered by community colleges and on-the-job training. In unionized environments, they are paired with journeypersons according to ratios defined in collective agreements. Journeyperson upgrading programs are often offered by joint apprenticeship and training committees with a focus on both classroom and hands-on training. An increased emphasis on worker health and safety means that related training is often mandatory for both apprentices and journeypersons. Many plumbers stay current by reading trade magazines.
Impact of Digital Technology
All essential skills are affected by the introduction of technology in the workplace. Plumbers’ ability to adapt to new technologies is strongly related to their skill levels across the essential skills, including reading, writing, thinking and communication skills. Technologies are transforming the ways in which workers obtain, process and communicate information, and the types of skills needed to perform in their jobs. In particular, the use of technology, such as computer-assisted design (CAD) software for system design, layout and project management, is increasing. Self-employed plumbers may also require a broad range of computer skills to operate software applications that help them bill and communicate with customers, track costs and revenues and produce financial summaries.
Digital technologies also provide workers with tools, such as smartphones which increase opportunities for verbal interaction and text-based interaction and improve workplace safety. For example, workers working independently in remote locations can access customers, supervisors and medical assistance using their smartphones or use them to pull up reference documents for equipment.
Technology in the workplace further affects the complexity of tasks related to the essential skills required for this occupation. For example, sophisticated plumbing installations have increased the complexity of schematics and other diagrams. In contrast, electronic databases, cloud storage, USB drives and keyword search functions make it easier to find information, such as diagrams and specifications. Not only can workers complete documents (e.g., work orders) with speed and accuracy using specialized software applications that input data automatically, but they can also calculate costs, material requirements, conversions, electrical resistance, volumes, rates and offsets using Web- based applications, specialized plumbing software and hand-held devices, such as tablets and smartphones.
How Do My Skills Measure Up?
There are many different assessments used to measure essential skills levels. Some are formal assessments that require taking a test that is marked and reviewed with you; for example, the Test of Workplace Essential Skills, known as TOWES (see below). However, there are also many non-formal assessments that are free of charge and available for your use, some of which are computer-based assessments:
- ITA Essential Skills: This website allows you to look at programs, take an assessment, and obtain a personalized learning plan based on your scores.
- Build Your Career with Essential Skills: This website allows you to research occupations and assess your skills in reading, document use, and/or numeracy. At the end of the assessment, you obtain your results and a personalized learning plan to help you build your skills.
- Essential Skills for Ontario’s Tradespeople: This website allows you to research essential skills for 53 Red Seal trades, take online assessments, and receive a customized learning plan based on your scores.
- Measure Up: SkillPlan’s Measure Up site allows you to complete an informal test to assess yourself and have an idea of how your skills match up with those required for over 200 different occupations. The site also provides practice for individuals who will be completing a formalized TOWES assessment (see below) and allows you to explore careers.
- TOWES: TOWES is a suite of nationally recognized assessment products that measure three essential skills: reading, using documents, and numeracy. This site provides information on preparing for TOWES, including sample questions.
Self-Assessments
Employment and Social Development Canada (ESDC) has developed a number of paper- based self-assessments that you can use to help understand your strengths and areas where there is need for improvement for each of the individual essential skills.
The Government of Canada updated its Essential Skills Framework at the end of June 2021. The new “Skills for Success” initiative replaces the Essential Skills model and adds two new skills: Adaptability and Creativity and Innovation; expands Problem Solving, Communication, Collaboration, and Digital; and updates Reading, Writing, and Numeracy. Details of the new program are available here: Skills for Success. As such, some of the old self-assessments have been removed from the Government of Canada site, and there appears to be a mix of old and new terminology on the site. Self-tests for Computer Use, Document Use, Continuous Learning, Working with Others, and Thinking appear to have been removed from the site. The Writing, Reading and Numeracy and Oral Communication self-tests have been retained and are linked below. They reference the new Skills for Success model and indicate that updated self-assessments may be developed in the future:
- Oral Communication Self-Assessment
- Writing Self-Assessment
- Reading Self-Assessment
- Numeracy Self-Assessment
The following two tools were also made available specifically for trades, however, the term “Essential Skills” is still used and it does not reflect the ‘Skills for Success’ model:
- Essential Skills Self-Assessment for Trades: This checklist will help you to identify strengths and areas for improvement in all nine essential skills.
- Essential Skills Workbook for Trades: This workbook, which includes an answer guide, allows you to practice your skills with activities in areas such as reading, document use, numeracy, math, conversions, and word problems.
There is also a general page with links that has some additional self-tests from other agencies: Skills for Success – Assessment and Training Tools.
Now complete the Learning Task Self-Test.
Self-Test
Self-Test 1
- Understanding the labour market and how employment in the workplace is changing will help you to find employment.
- True
- False
- Over the course of your lifetime, you will most likely work for multiple employers and in a variety of different employment sectors.
- True
- False
- What were the three major trends affecting the labour market in Canada and British Columbia in 2015?
- The ability to compete locally, a lack of employment prospects, and low wages
- The ability to compete in a global market, a shortage of workers with specific credentials, and a skills gap
- The ability to compete in a global market, a surplus of employment prospects for all Canadians, and a shortage of training opportunities
- The lack of opportunities for new tradespeople, a surplus of workers with specific credentials, and the ability to compete in a global market
- Most employers believe that recent graduates and potential employees have adequate essential skills.
- True
- False
- Insufficient essential skills cost the Canadian economy billions of dollars in gross domestic product (GDP) annually.
- True
- False
- Who predicts changes in the labour market?
- Banks
- Governments
- Business associations
- All of the above
- The majority of companies in Canada are small- to medium-sized enterprises with 25 employees or less.
- True
- False
- The majority of baby boomers will retire by 2030, and this will create significant opportunities for new employees with the desired skills and qualifications.
- True
- False
- Research does not show a direct correlation between the essential skill levels of employees and a company’s productivity.
- True
- False
- Apprentices with the necessary essential skills for their profession are up to eight times more likely to pass their exams.
- True
- False
- Essential skills are the foundation for learning all other skills.
- True
- False
- Which of the nine essential skills is missing from this list?
- reading
- writing
- numeracy
- digital skills
- thinking
- oral communications
- working with others
- continuous learning
- Listening
- Working alone
- Computer skills
- Document use
- The Canadian government has prepared detailed essential skills profiles for almost every trade and occupation, and this information is available on the Web.
- True
- False
- There are numerous free self-assessment tools available on the Internet (Web based and paper based) to help you understand your essential skills levels and how you can improve them.
- True
- False
- Giving each person the support they require to be successful is:
- Equity
- Equality
- Giving everyone the same thing regardless of their needs is:
- Equity
- Equality
- The increased discrimination of people that identify with multiple underrepresented groups is often referred to as:
- Racism
- Bipartisanism
- Intersectionality
- Equality
- Women represent more than 50% of Canada’s population, but only ____ % of Canada’s skilled trades workforce.
- 5%
- 20%
- 40%
- 70%
- Which of the following is/are reason(s) that Indigenous peoples tend not to pursue a career in the skilled trades?
- Barriers to access of shop classes
- Lack of mentorship by Indigenous journeypersons
- Unwelcoming institutions and workplaces
- All of the above
- It is important to assess any extra support you will need with your education prior to the start of your studies.
- True
- False
See the Answer Key in the back matter of the textbook for self-test answers.
Media Attributions
- “Line B-2 Learning Task 1” was generated using NaturalReader Commercial by BCcampus and is licensed under a CC BY 4.0 licence.
- “R” icon by Nathan David Smith is licensed under a CC BY 3.0 licence.
- “Essential Skills: Reading Text” video by Skills/Compétences Canada is licensed under the Standard YouTube licence.
- “Essential Skills: Writing” video by Skills/Compétences Canada is licensed under the Standard YouTube licence.
- “Essential Skills: Document Use” video by Skills/Compétences Canada is licensed under the Standard YouTube licence.
- “Essential Skills: Numeracy” video by Skills/Compétences Canada is licensed under the Standard YouTube licence.
- “Essential Skills: Digital” video by Skills/Compétences Canada is licensed under the Standard YouTube licence.
- “Essential Skills: Thinking” video by Skills/Compétences Canada is licensed under the Standard YouTube licence.
- “Essential Skills: Oral Communication” video by Skills/Compétences Canada is licensed under the Standard YouTube licence.
-
“Essential Skills: Working with Others” video by Skills/Compétences Canada is licensed under the Standard YouTube licence.
-
“Working with Others: An Essential Skill” video by literacyAB is licensed under the Standard YouTube licence.
- “Essential Skills: Continuous Learning” video by Skills/Compétences Canada is licensed under the Standard YouTube licence.