Learning Task 1
The Refrigeration Cycle
The refrigeration cycle is the basis of operation of all vapour-compression heat pumps. A chemical compound with a low boiling point, known as refrigerant, travels through piping around a closed-loop circuit that consists of:
- An evaporator
- A compressor
- A condenser, and
- A thermal or thermostatic expansion valve, referred to as a “TXV”
Figure 1 below shows these four components and how they are connected.
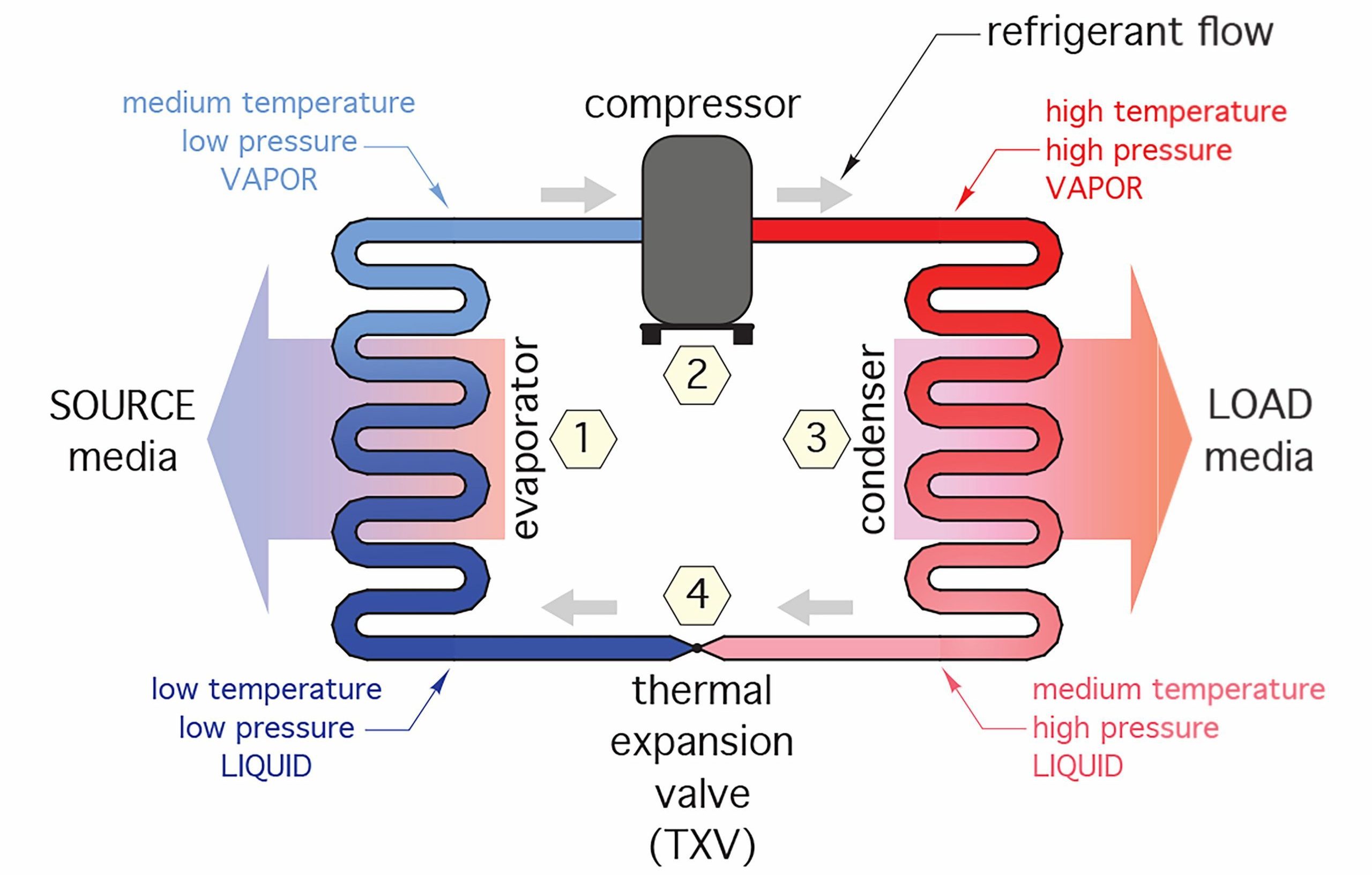
The cycle begins at station (1) as cold liquid refrigerant within the evaporator. At this point, the refrigerant is colder than the source media (e.g., air or water) passing across the evaporator. Because of this temperature difference, heat moves from the higher-temperature source media into the lower-temperature refrigerant. As the refrigerant absorbs this heat, it vapourizes (changes from a liquid to a gas). The vaporized refrigerant continues to absorb heat until it is slightly warmer than the temperature at which it evaporated. The additional heat required to raise the temperature of the refrigerant above its “saturation” temperature (the point at which it vaporizes) is called superheat, and it also comes from the source media. This vaporized refrigerant then flows into the compressor at station (2). Here a reciprocating piston or a rotating scroll driven by an electric motor compresses the vapourized refrigerant. Charles’ Law dictates that this causes a large increase in both pressure and temperature. The electrical energy used to operate the compressor also creates heat which is also absorbed by the refrigerant. The temperature of the refrigerant gas leaving the compressor is usually in the range of 120°F to 170°F depending on the operating conditions.
The hot refrigerant gas then flows into the condenser at station (3). Here it transfers heat to a stream of water or air (the load media) that carries the heat away to the load. As it gives up heat, the refrigerant changes from a high-pressure, high-temperature vapor into a high-pressure, somewhat cooler liquid. In other words, it condenses. The high-pressure liquid refrigerant then flows through the thermal expansion valve at station (4). This valve, mentioned above as being abbreviated to “TXV”, is essentially an orifice that operates on Bernoulli’s Principle, meaning the greater the velocity, the lower the pressure. Thus, the refrigerant’s pressure is greatly reduced and the drop in pressure causes a corresponding drop in temperature. This restores the refrigerant to the same condition it was in when the cycle began, and the refrigerant vapour is now ready to repeat the cycle.
The refrigeration cycle remains in continuous operation whenever the compressor is running. It is used in refrigerators, freezers, room air conditioners, dehumidifiers, water coolers, vending machines and other heat-moving machines. The average person is certainly familiar with these devices and what they do, but often is unaware of how they do it.
Non-Reversible vs Reversible Heat Pumps
Non-reversible (heating-only or cooling-only) heat pumps provide dedicated cooling or dedicated heating of a load by moving the refrigerant through the components within the loop in one direction only. An example of cooling-only heat pumps are appliances such as refrigerators, where the evaporator is the device that is performing the desired task of cooling the load by taking away the heat from the inside of the cabinet and delivering it to the condenser which “dumps” the unwanted heat to the surrounding air. In a heating-only application, such as a dedicated heat pump system providing heat for a building, the evaporator is gathering low-temperature heat from an abundant source such as the outdoors, and transferring it to the condenser (a coil in indoor ductwork) where it is used to heat the air being circulated through the building. So, in a cooling-only scenario, the evaporator is the vehicle for the cooling, while in a heating-only scenario it is the condenser that is the vehicle for delivering the heat.
Some varieties of heat pumps have the ability to either heat or cool the load, by reversing the flow of refrigerant on demand. These are known as reversible heat pumps, and when used for a residential house can heat it in the winter and cool it in the summer. Reversible heat pumps use an electrically-operated device called a reversing valve. As suspected by its name, this valve at rest would direct refrigerant through the system so that the load would be in heating mode. If cooling at the load were needed, the reversing valve is electrically energized and the flow of refrigerant through the system is reversed, providing cooling to the load. Figure 2 below shows the heat pump in heating and cooling modes, dependant on the direction of refrigerant flow.
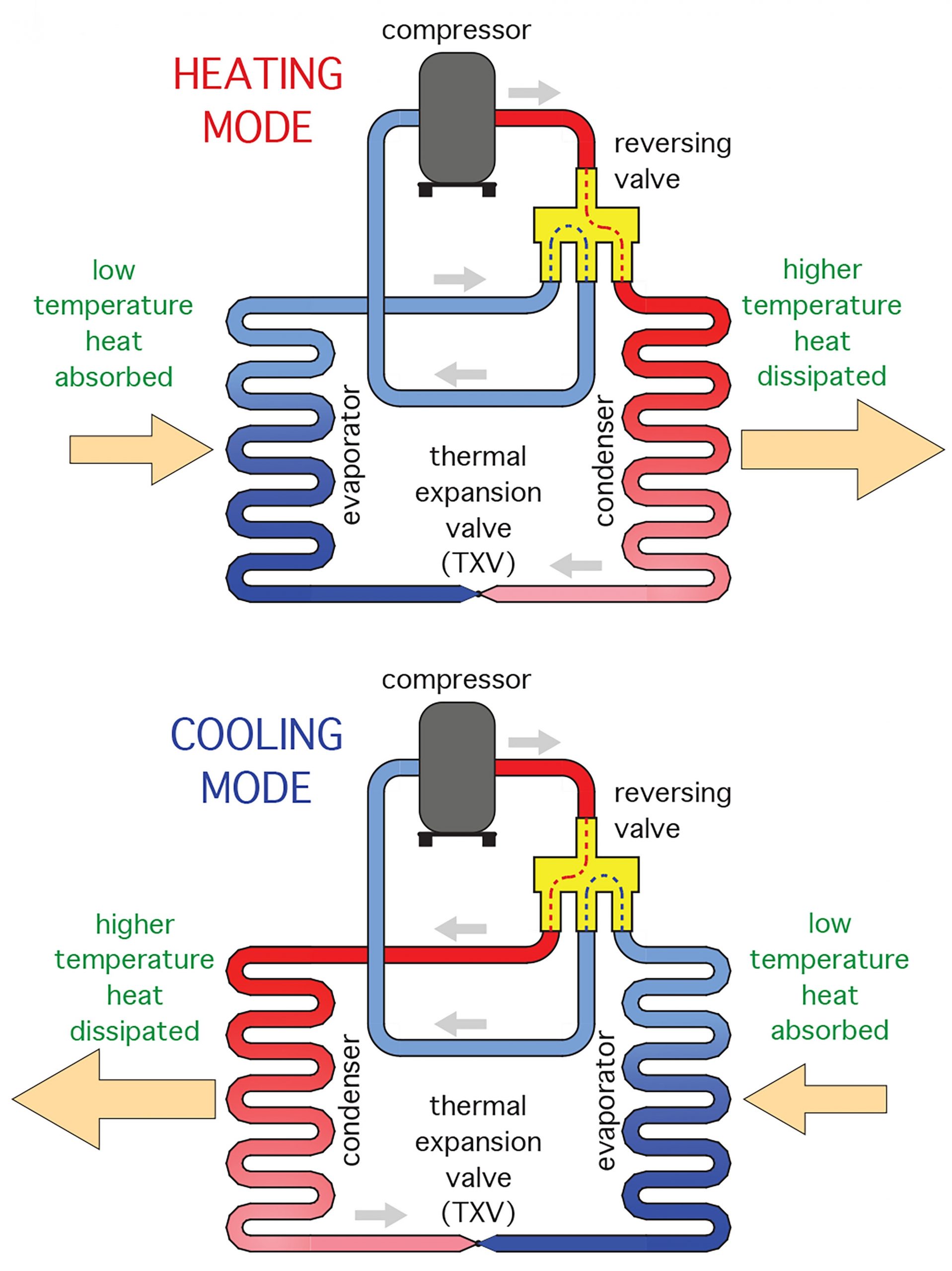
The evaporator and condenser effectively change functions in a reversible system. The heat exchanger that serves as the evaporator while in heating mode becomes the condenser while in cooling mode, and the exchanger that is the condenser in the heating mode becomes the evaporator in the cooling mode.
Reversible heat pumps commonly use two sets of thermal expansion and check valves, with one set used for the cooling mode and the other set for the heating mode. Others use a bi-directional (two-way) TXV for flow reversal of refrigerant. For simplicity and ease of understanding we will use diagrams that show a reversing valve and single TXV.
Heat Pump Categories
Heat pumps are classed by the media that they firstly take heat from (the source) and secondly deliver it to (the load). Consequently, the heat pump types are:
- Air-to-air
- Air-to-water
- Water-to-air, and
- Water-to-water
Air-to-Air Heat Pumps
These are the most commonly-used types for residential buildings in North America, as they can provide both heating and cooling on demand. In heating mode, low-temperature heat is extracted from outdoor air through an evaporator contained within an outdoor unit (“outside coil”). This is a large air-to-refrigerant heat exchanger consisting of several feet of copper or aluminum tubing to which are attached closely-spaced fins of aluminum, similar to a car’s radiator. The large surface area of the fins facilitates the heat exchange process. The fins and coil surround a compressor that is mounted at the base and a fan that is mounted on the underside of the top of the outdoor unit’s housing. The fan pulls outdoor air horizontally across the fins and discharges it vertically upward. The vapourized refrigerant is compressed by the compressor and moved through one of the two copper tubes, known as a lineset, to the condenser coil mounted in the air handling unit inside the building. The condenser is also a heat exchanger consisting of copper or aluminum tubing and closely-spaced fins. The hot refrigerant gas from the outdoor unit passes through the condenser coil, giving up its heat to the airstream and condensing back into a liquid. It then moves through the other copper line of the lineset back to the outdoor unit, where it passes through the TXV and is returned to its same starting condition, ready for the next cycle.
In cooling mode, the refrigerant direction reverses. The condenser in the air handler becomes an evaporator which extracts heat from the air moving through the ductwork. The refrigerant transfers this heat via the lineset to the outdoor coil which becomes the condenser. The fan pulls heat from the condenser and releases the heat to the outdoor air.
Figure 3 below shows an air-to-air heat pump system in heating mode, with a supplemental electric heater, called a strip heater, in the air handler. The strip heater adds heat to the air stream if the heat pump’s output can’t keep up with the heat loss for the building (see the explanation following).
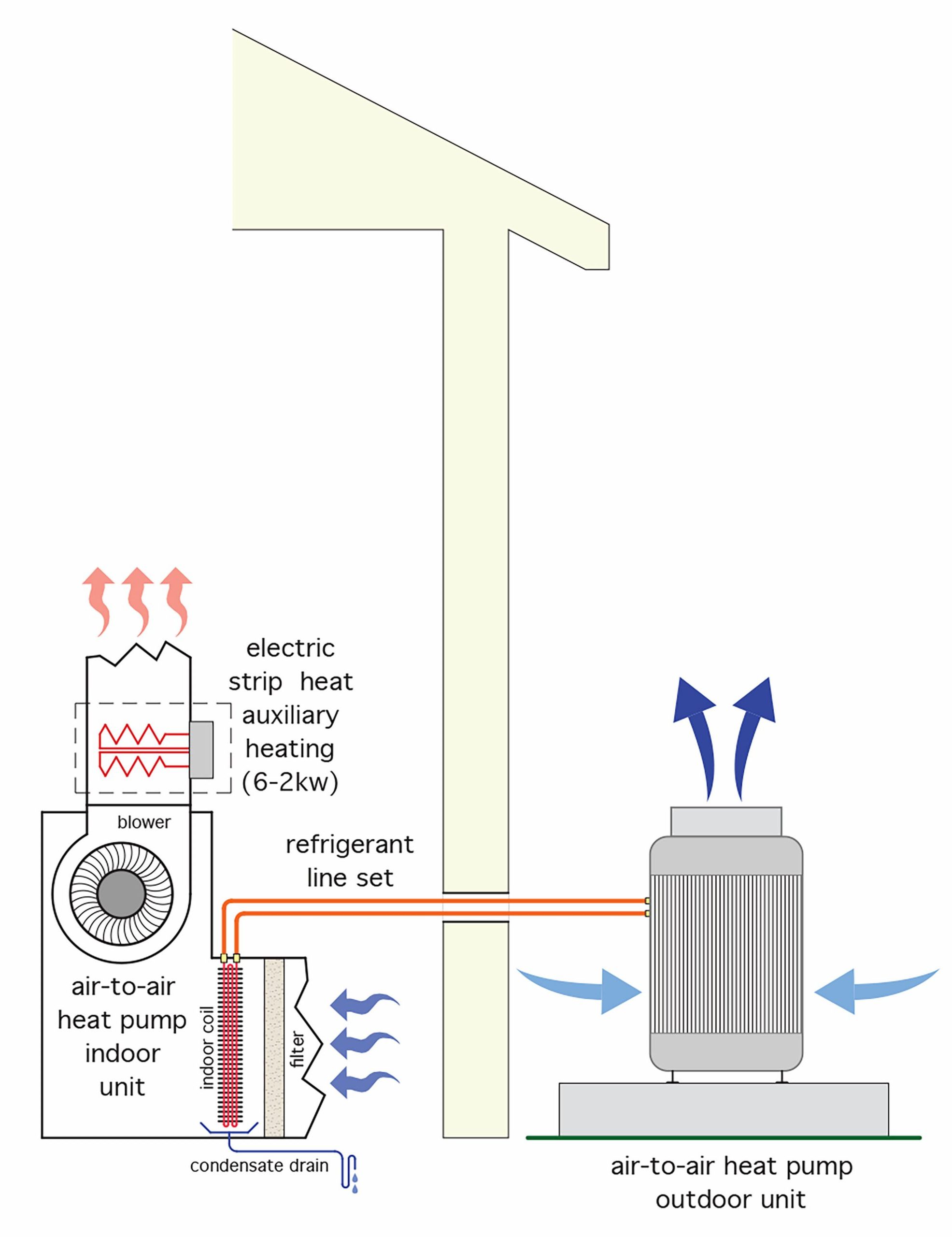
When in cooling mode, water vapour in the air passing through the inside coil will condense onto the surfaces of the coil. This will create a couple of issues. Firstly, the liquid water will need to be collected and drained safely away from the unit so as to avoid corrosion problems and water damage. Indoor coils for cooling normally sit within a drain pan that can be piped to a safe location. Secondly, the damp surfaces of the indoor coil will allow dirt, dust and other impurities in the air stream to cling to it. Over time, this will plug the very small openings between the fins and hinder the flow of air through them. The installation of a high-quality filter element is essential in order to avoid plugging the heat exchanger.
Because of the prominence of forced air heating systems in North America, homes that are located in areas where air conditioning in summer months is a necessity are prime candidates for reversible heat pump systems. They work very well in temperate climates, where the winter outdoor design temperature is not extremely low. In Canada, however, their use is fairly restricted to the lower latitudes. The further geographically north that they are installed, the more potential the need for some form of supplemental heat in the coldest times of the year. Although technology is improving, many air-to-air heat pumps are still not suitable for severe winter climates where temperatures frequently drop below -18°C (0°F) and large accumulations of snow and ice are possible around the outdoor unit. Figure 4 below shows a typical outdoor unit.
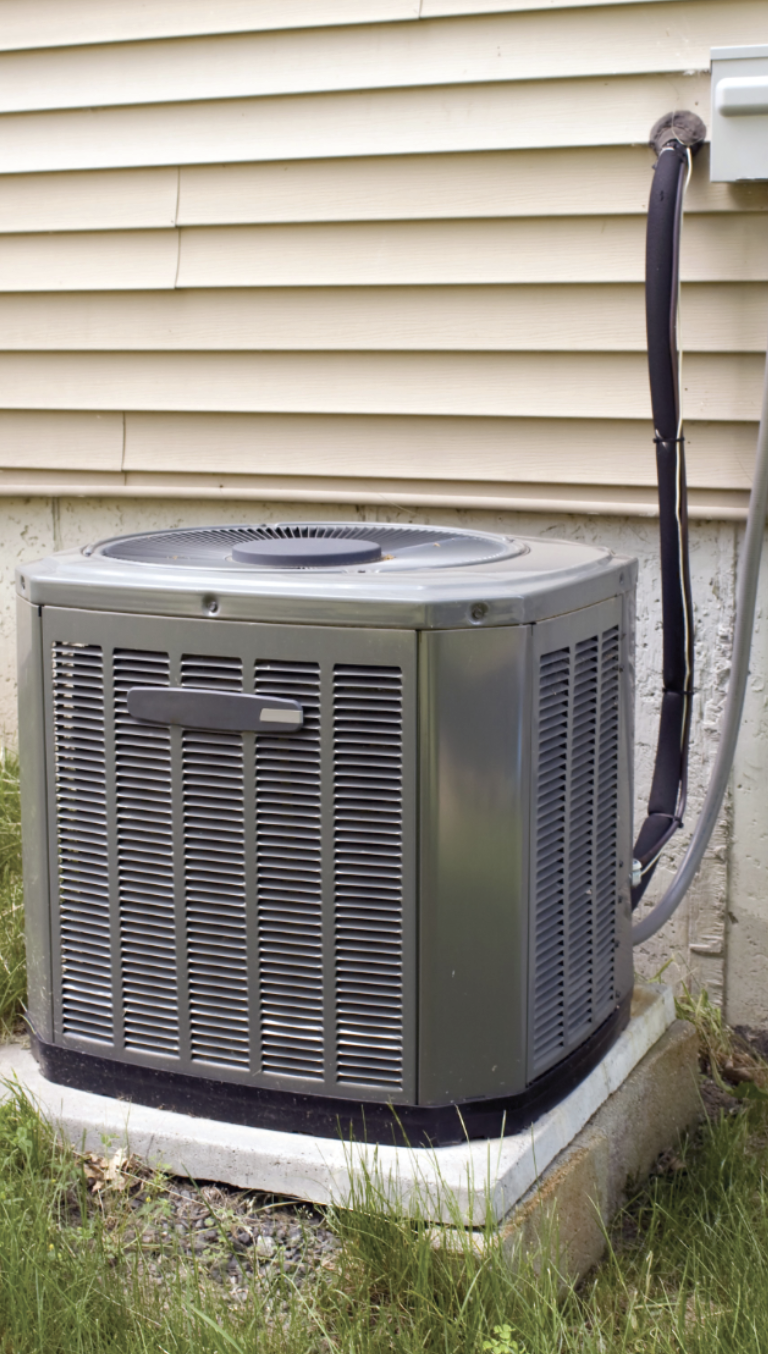
Downsides to an air-to-air outdoor unit are its visibility and noise. While the more recent versions of these units are much quieter in operation than their early counterparts, they can still be aesthetically objectionable.
Air-to-Water Heat Pumps
An air-to-water heat pump uses an outdoor unit that is similar to those in the air-to-air systems, but the indoor unit is a heat exchanger that transfers its heat to a hydronic distribution system. Figure 5 below shows an air-to-water reversible heat pump in both heating and cooling modes.
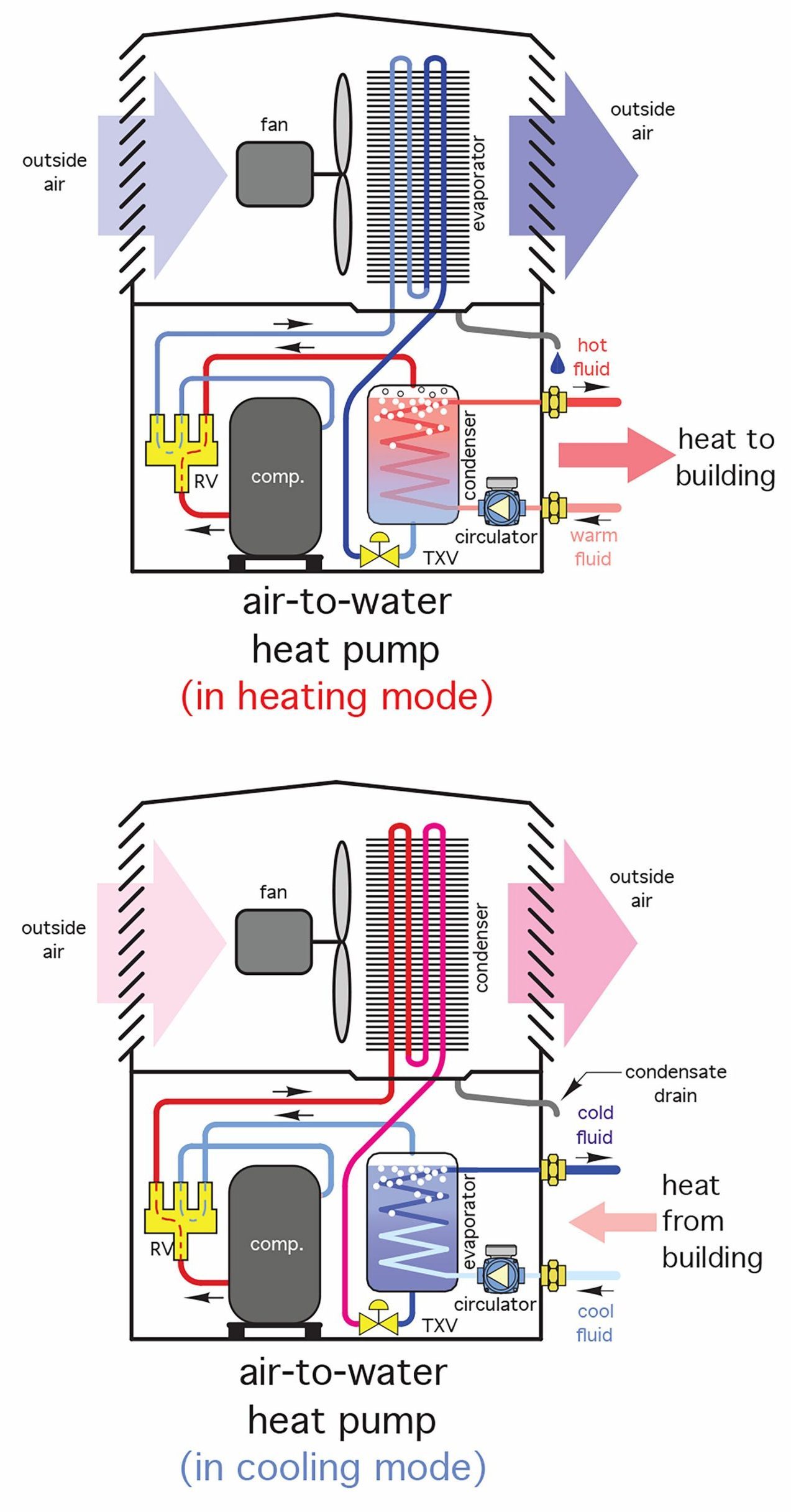
The outdoor unit shown above is “self-contained”, in that the heat exchange tank acting as the evaporator/condenser, depending on the mode, is built into the outdoor unit. A circulator, which is also located within the housing, pumps heated or chilled water from the heat exchanger into the building to feed the hydronic distribution system. In cold climates, the water being circulated between the outdoor unit and the building must be treated with an anti-freeze solution in addition to being insulated. This would mean that the entire distribution system would need to have anti-freeze solution running through it. An alternative to that strategy would be to have the anti-freeze feed a load such as a heat exchanger. That way, only the loop between the outdoor and indoor heat exchangers would need to be freeze protected. Figure 6 below shows such a system.
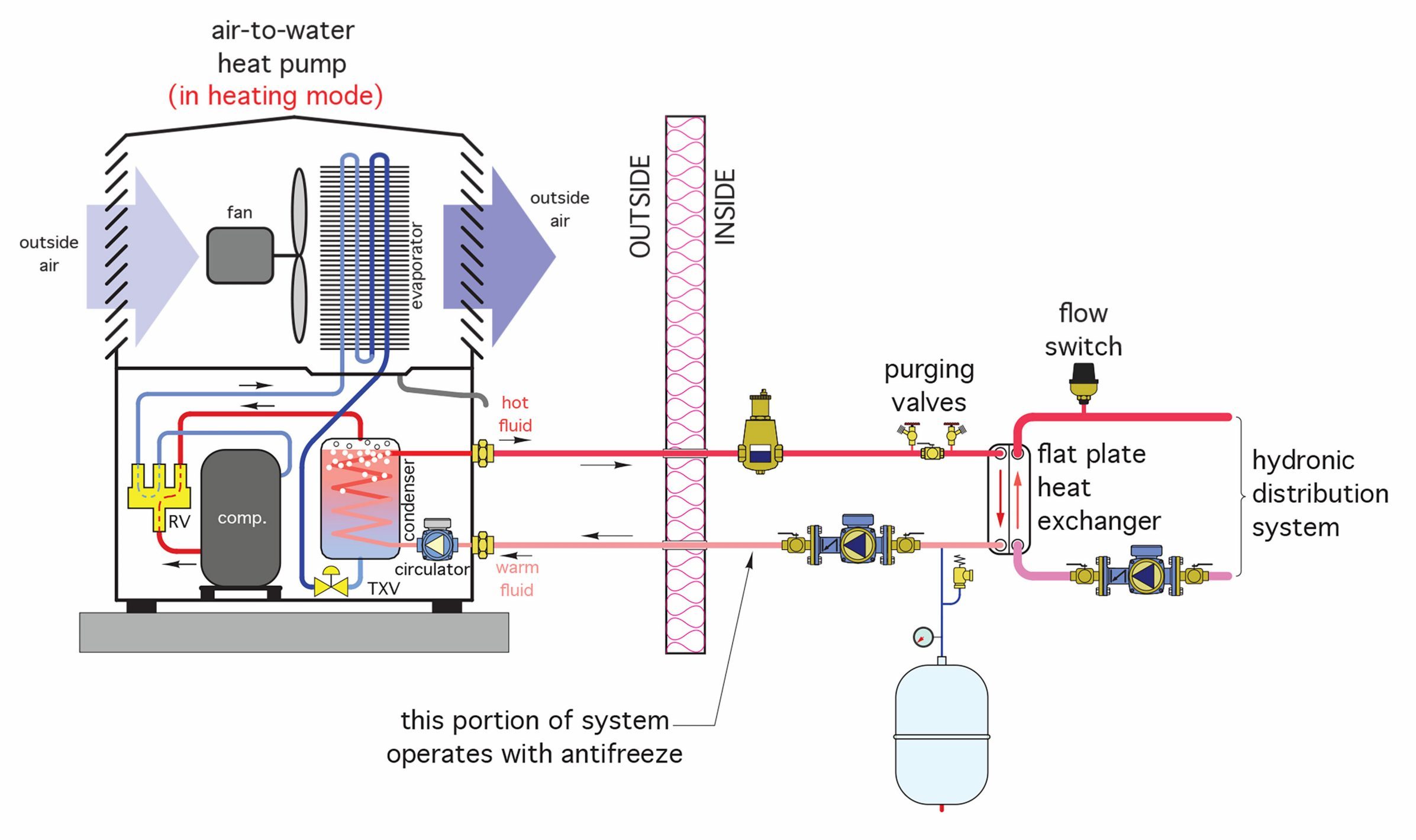
The antifreeze loop above would be a closed system and therefore require its own circulator, expansion tank and makeup water station. If conditions allow, connecting the outdoor unit to the indoor unit using refrigerant within linesets makes the most sense, as it eliminates the need for an antifreeze solution and extra equipment.
Water-to-Air Heat Pumps
Water-source heat pumps are used in almost all applications where a heat pump is drawing low-temperature heat from any other source other than air. The fluid that delivers heat to the heat pump can be either water or a water-based antifreeze solution that pulls heat from a few different sources, such as a pond, stream, horizontal trenches, vertical wells, etc. Figure 7 below is an example of a common variety of water-to-air heat pump.
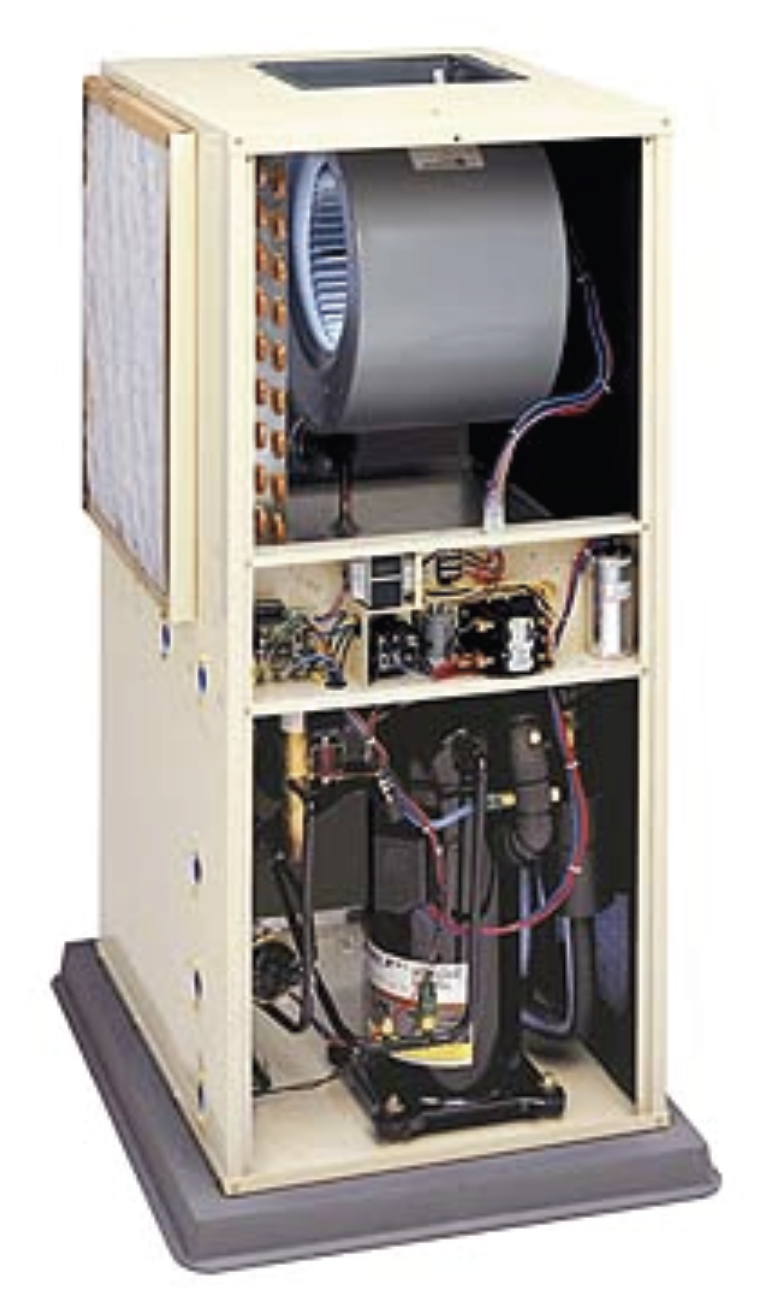
In Figure 7, a fan pulls return air through the filter on the side of the cabinet and across the condenser coil which heats the air. The heated air is discharged through the supply outlet on the top of the cabinet into the ducting. Tubing carrying low temperature heat from the evaporator is piped into the lower compartment of the housing which contains the compressor, circulator and controls. The cabinet shown above would be found in an upflow or downflow forced air ducting system, whereas the unit shown below in Figure 8 would be more preferable for installation horizontally, such as in an attic or crawl space.
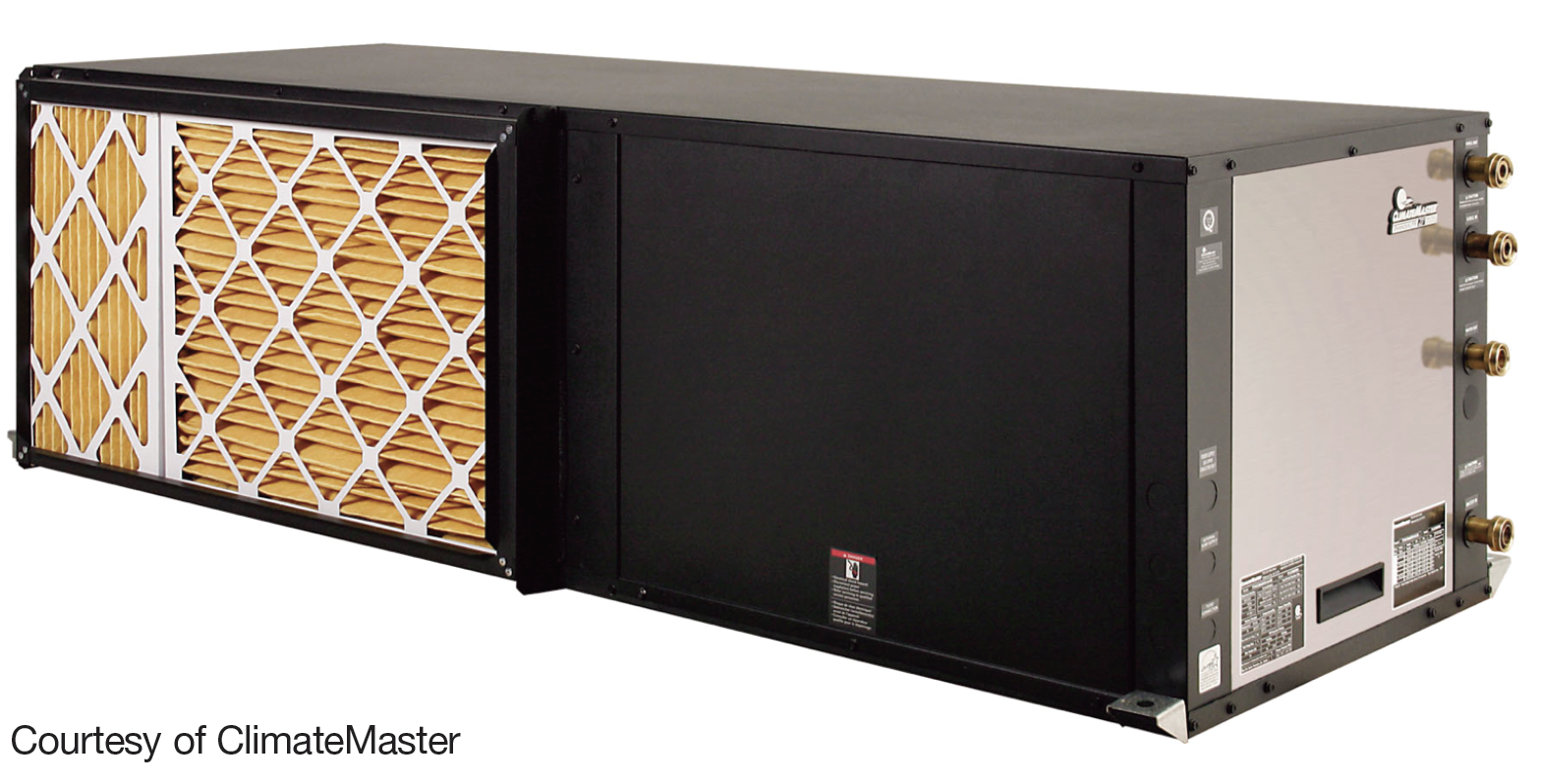
Figure 9 below is a schematic diagram of a reversible water-to-air heat pump.
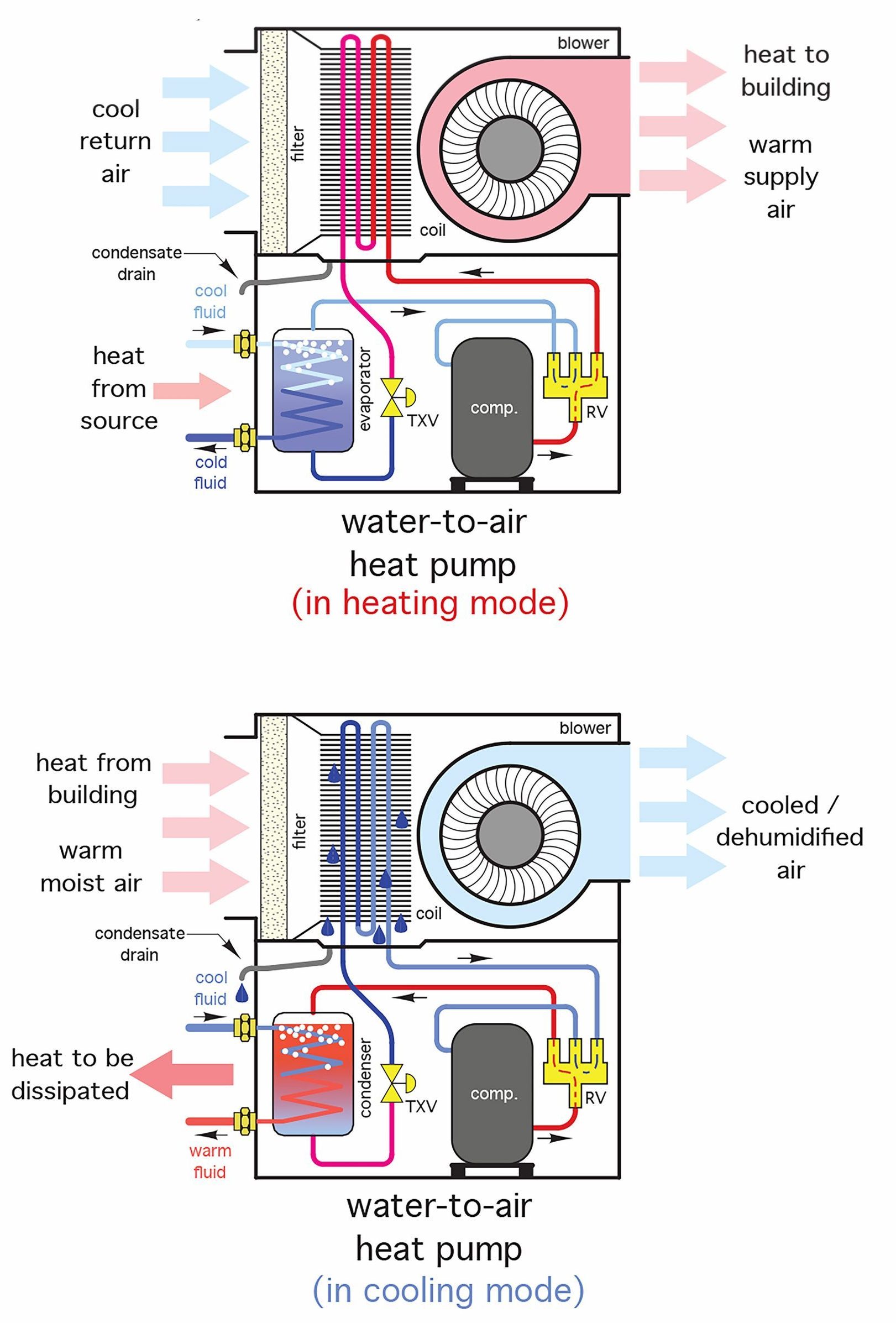
Water-to-air reversible heat pumps will either cool or heat the building air while extracting or dumping heat between the source and load, depending on which mode the unit is in.
Remember that when using an indoor heat exchanger for cooling of air, liquid condensate must be collected and piped to a safe location.
Water-to-Water Heat Pumps
Water-to-water heat pumps extract low-temperature heat from the same sources as do the water-to-air heat pumps, however the load for these systems is water or a water-based solution rather than air. They can be used to heat or cool a building’s hydronic distribution system or process piping, or to heat swimming pools or domestic hot water. Figure 10 below shows one variety of water-to-water heat pump. They can be more compact than a water-to-air type because of the lack of need for a large blower assembly and associated ductwork.
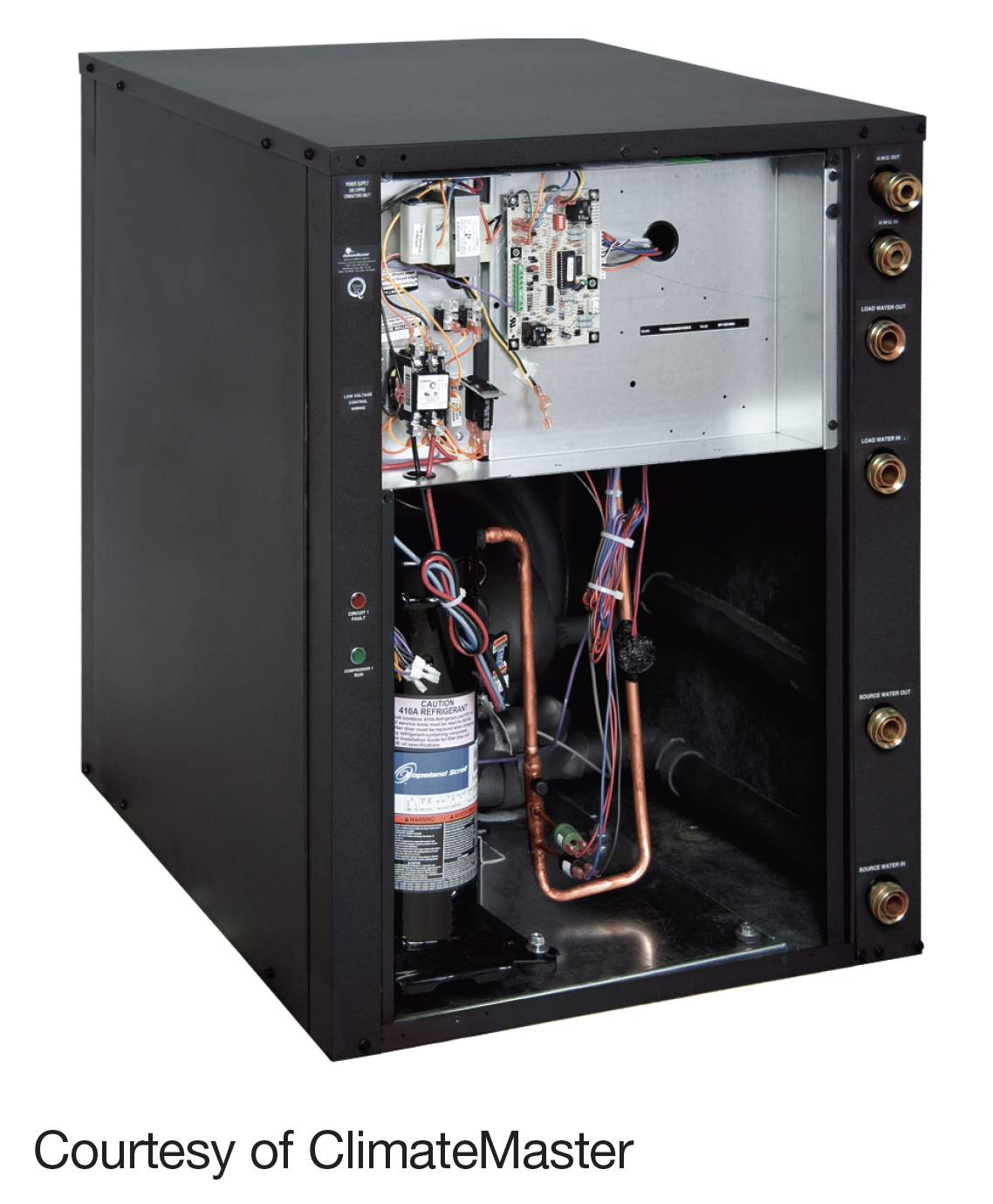
A common example of the use of a water-to-water heat pump might be one that is found in a radiant heating system for a house. Either vertical or horizontal underground (earth loop) piping carrying water or a water-based solution is connected to a water-to-water heat pump located within the building. The heat pump provides heated water for the building’s radiant system and may also provide heat for domestic hot water. Figure 11 below is a schematic drawing for a water-to-water heat pump.
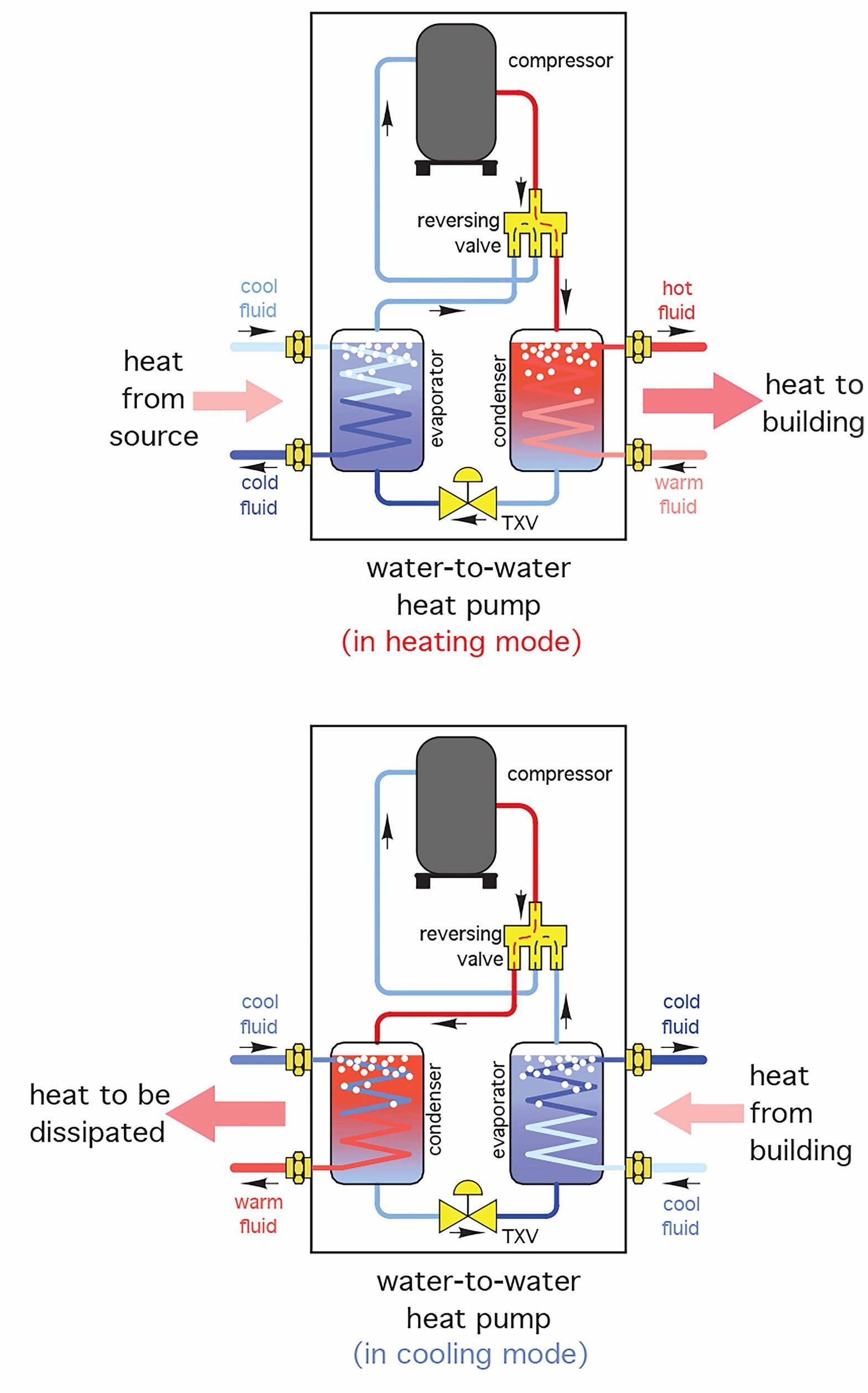
The water-to-water systems are predominantly used as building heating-only systems due to the restraints encountered in using a hydronic heating system for summer cooling. Process systems, however, could utilize the cooling side of these systems quite easily.
Now complete Self-Test 1 and check your answers.
Self-Test 1
Self-Test 1
- What is considered to be the core of a heat pump system?
- Heat
- A furnace
- The refrigeration cycle
- The earth’s hydrological cycle
- Which one of the following is the fourth component of a refrigeration system that contains a compressor, a condenser, and a TXV?
- A chiller
- A manifold
- A buffer tank
- An evaporator
- What is the term given to the additional heat that is required to raise the temperature of the refrigerant above its saturation temperature?
- Extra heat
- Superheat
- Latent heat
- Sensible heat
- Which component of a refrigeration system is responsible for absorbing heat from a source into the refrigerant?
- The condenser
- The evaporator
- The compressor
- The thermal expansion valve
- Which component of a refrigeration system is responsible for “dumping” heat from the system to a load?
- The condenser
- The evaporator
- The compressor
- The thermal expansion valve
- In a cooling-only scenario, which one of the following would be the vehicle responsible and would be mounted within the ductwork?
- The condenser
- The evaporator
- The compressor
- The thermal expansion valve
- What component listed below is responsible for allowing a heat pump to either heat or cool a load?
- The condenser
- The compressor
- The reversing valve
- The thermal expansion valve
- What type of heat pump is most commonly used in homes in North America?
- Air-to-air
- Air-to-water
- Water-to-air
- Water-to-water
- What is the term given to the pair of copper tubes that move refrigerant between the evaporator and compressor?
- A supply/return set
- A supply set
- A return set
- A lineset
- What may be required if an air-to-air heat pump can’t keep up with the building heat loss in very cold climates?
- An auxiliary electric heater installed in the supply ductwork
- A changeover to an air-to-water heat pump
- A newer, bigger air-to-air heat pump
- A larger TXV
- What component will aid in keeping a cooling coil in a furnace’s supply duct from becoming plugged?
- A condensate drain pan
- A high-quality air filter
- A reversible TXV
- A strip heater
- What component, when installed with an air-to-water heat pump, eliminates the need for having to freeze-protect the entire distribution system?
- A TXV
- A circulator
- An evaporator
- A heat exchanger
- If a heat pump pulls low-temperature heat from vertical loops installed in a well and transfers it to a coil in a forced-air furnace, what variety of heat pump is it?
- Air-to-air
- Air-to-water
- Water-to-air
- Water-to-water
- A coil installed within a supply duct on a heat pump, intended to heat the air, would be an example of what component?
- A condenser
- A strip heater
- An evaporator
- A reversing valve
- A heat pump installed to heat or cool a building through a radiant floor system by using the heat from an earth loop would be an example of what type of heat pump?
- Air-to-air
- Air-to-water
- Water-to-air
- Water-to-water
Check your answers using the Self-Test Answer Keys in Appendix 1.
Media Attributions
- Figure 1 The refrigeration cycle © Caleffi Hydronic Solutions. Used with permission.
- Figure 2 Reversible heat pump © Caleffi Hydronic Solutions. Used with permission.
- Figure 3 Air-to-air heat pump in heating mode © Caleffi Hydronic Solutions. Used with permission.
- Figure 4 Typical air-to-air outdoor unit © Caleffi Hydronic Solutions. Used with permission.
- Figure 5 Air-to-water reversible heat pump © Caleffi Hydronic Solutions. Used with permission.
- Figure 6 Air-to-water system using antifreeze and heat exchanger for freeze protection © Caleffi Hydronic Solutions. Used with permission.
- Figure 7 Water-to-air heat pump © Caleffi Hydronic Solutions. Used with permission.
- Figure 8 Horizontal water-to-air heat pump © Caleffi Hydronic Solutions. Used with permission.
- Figure 9 Reversible water-to-air heat pump © Caleffi Hydronic Solutions. Used with permission.
- Figure 10 Water-to-water heat pump © Caleffi Hydronic Solutions. Used with permission.
- Figure 11 Water-to-water reversible heat pump schematic © Caleffi Hydronic Solutions. Used with permission.