Main Body
6 Workplace Hazards
By recognizing and understanding the potential hazards in your work area, you can help prevent accidents from occurring. All accidents are preventable. Both employees and employers must take responsibility for making the workplace safe. Causing injury by failing to follow known safety procedures or knowingly allowing uncontrolled hazardous situations to develop are serious safety violations.
Workplace hazards include things such as slippery floors, loose floor mats, and sharp knives, as well as hazardous materials. It is important for all employees to be aware of hazards, even if they seem obvious. Employers should provide information and training on any safe work procedures related to the job site. Safe work procedures are specific directions for doing a task or operating equipment that may pose a risk or hazard to the worker. Workers should always ask their supervisor if there are any safe work procedures they need to be aware of and/or any written instructions they should be following.
One of the main hazards in any workplace are cleaning products, some of which are everyday products that a person may not regard as hazardous, such as sanitizers and household cleansers. Cleaning products and all other materials that are potentially hazardous are governed by the Workplace Hazardous Materials Information System (WHMIS)
Workplace Hazardous Materials Information System (WHMIS)
The Workplace Hazardous Materials Information System (WHMIS) is Canada’s national system of classifying and communicating information about hazardous materials in the workplace. The key components of the system are the classification of materials, cautionary labels and symbols, material safety data sheets (MSDS) and workplace education and training programs.
WHMIS was first introduced in 1988, and in 2015 it was changed to include the Globally Harmonized System of Classification and Labelling for chemicals (GHS). Currently there is a transition period, until 2018, to allow for suppliers, employers, and workers, to adapt to the new requirements. During this transition period, manufacturers, distributors, and employers will be allowed to comply with either the former WHMIS 1988 requirements or the new WHMIS 2015 requirements to allow for a phased-in approach.[1]
Federal legislation, the Hazardous Products Act HPA[2] establishes which products are regulated under WHMIS and have been traditionally categorized as controlled products within the Controlled Product Regulation (CPR). Changes in 2015 to align with the GHS include a change in terminology, classifying substances as hazardous products, and replacing the CPR with a new Hazardous Product Regulation (HPR).[3]
Regardless of the changes in terminology, WHMIS covers the sale, distribution, and use of hazardous materials in the workplace.
WorkSafeBC regulations cover the use of hazardous materials in the workplace and identify employers’ responsibilities. Workers who work with hazardous products must know how to handle them safely, which requires being properly trained on their use.
WHMIS categorizes hazardous materials in six hazard classes. These classes are depicted by eight symbols that identify the specific hazards of controlled products. After a controlled product has been classified, the following three WHMIS elements are used to communicate health and safety information:
- WHMIS label
- Material safety data sheets (MSDS)
- WHMIS education and training programs
Hazardous (Controlled) Products
WHMIS defines a hazardous or controlled product as a pure substance or mixture that meets or exceeds criteria for inclusion in one or more of the WHMIS hazard classes. The six classes and eight hazard symbols from WHIMS 1988 are shown in Figure 1, and the symbols from the WHMIS 2015 program, which uses the GHS, are included in Figure 2. The appropriate symbol must appear on the applicable supplier labels.
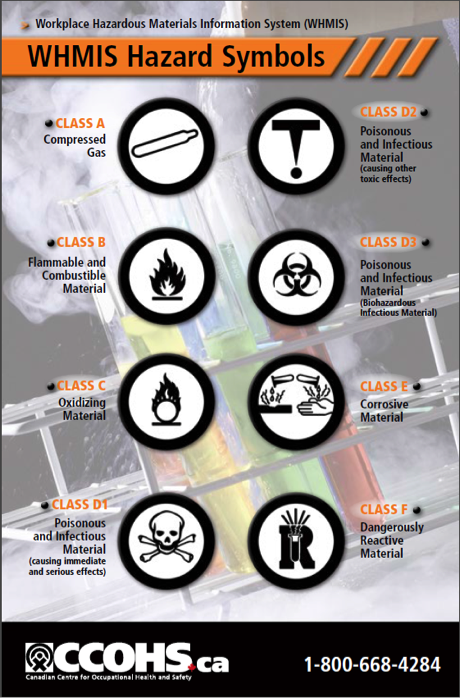
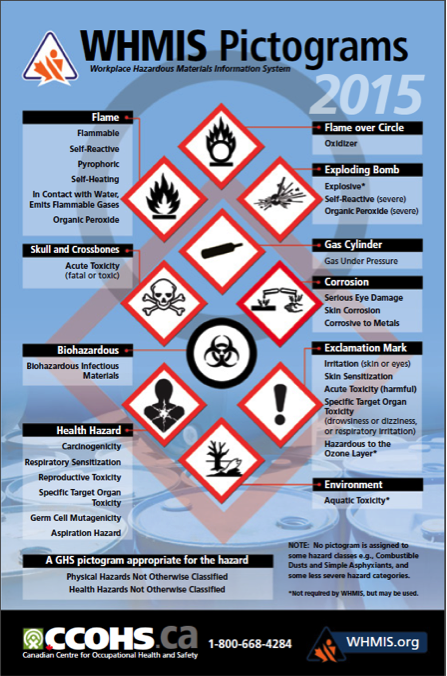
WHMIS Education and Training Programs
Everyone who uses hazardous materials must be trained to use them properly and to use the personal protective equipment specified in the MSDS. It is the responsibility of the employer to provide WHMIS training as a part of an occupational health and safety program. If you have not received training in WHMIS, ask your employer to schedule a session for you as soon as possible.
Training must:
- Address any WHMIS requirements
- Be reviewed at least annually (more frequently if work conditions or hazards change)
- Provide for the periodic assessment of knowledge by testing or observation