Terms and Definitions
5 Plugging vs. Anti-Plugging
Click play on the following audio player to listen along as you read this section.
https://media.bccampus.ca/id/0_v7yra6xr?width=608&height=80&playerId=23449753
When a three-phase motor is first energized, it experiences an inrush current and harsh starting torque. If, for example, a motor is spinning in the forward direction and is stopped and suddenly reenergized in the reverse direction before the shaft of the motor has time to come to a complete stop, the motor will be said to have been “plugged.”
Plugging is hard on motors, and if they are directly attached to high inertia loads, the shaft of the motor can shatter. Plugging also causes excess heating of the conductors that make up the coils inside the motor, as well as the power contacts of the motor starter. If a motor is expected to make sudden reversals of direction, then the motor starters should be increased in size and horsepower rating to accommodate for this more severe operation.
Some circuits use this plugging action to quickly decelerate and stop a motor. For example, in certain machine-tool operations where instantly stopping motor drives may be necessary. We will be examining a plugging circuit in greater detail further in this text.
If the sudden reversal of a motor is considered undesirable, then our control circuit can be designed to provide anti-plugging, which can be provided by either a normally closed zero-speed switch or off-delay timer relays.
As a general rule, the control scheme for plugging includes a reversing magnetic starter and a rotary-motion switch called a zero-speed switch. The switch assembly is usually connected directly to the shaft of the motor or the driven equipment so that when the motor spins in a particular direction, the contacts change their state (normally closed contacts open, and normally open contacts close).
Normally open contacts provide plugging while normally closed contacts provide anti-plugging.
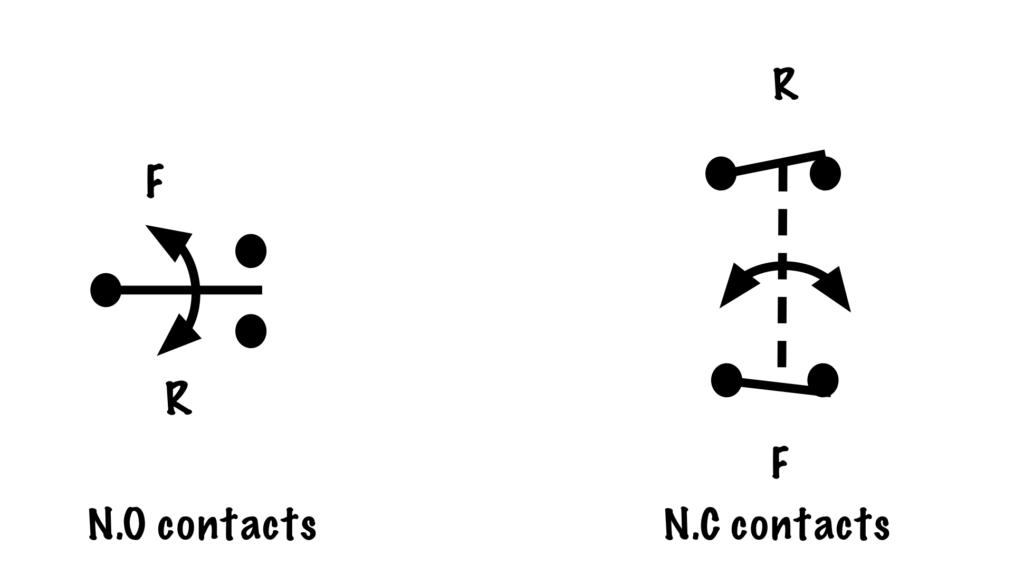
The initial high value of current produced when an inductive load is first energized.
When a motor is spinning in one direction and is stopped and suddenly re-energized in the opposite direction before the shaft of the motor has time to come to a complete stop.
A device that controls the flow of electrical power to a motor. It is designed to safely start and stop a motor, and provide overload protection.
A circuit that utilizes the momentary reversal of the direction of a three-phase motor to bring it to a sudden stop. Can be very hard on the motor and any driven equipment.
In contrast to the Power Circuit, the Control Circuit consists of inputs, in the form of switches, pushbuttons or pilot devices, which when activated, can either directly, or through a magnetic motor starter, energize a load. The Control Circuit often operates at a lower voltage than the Power Circuit for safety and ease of installation.
A circuit that is not designed to suddenly stop or reverse a motor until the shaft has come to a rest.
A contact that under normal conditions has continuity through it. When the contact changes its state it interrupts the flow of current by opening its contacts. Can be associated with pushbuttons, pilot devices or magnetic contactors.
A switch that is activated by centrifugal forces and is attached either directly or via a belt to the shaft of the motor.
The conducting part of a switch that makes or breaks a circuit.
A contact that under normal conditions does not have continuity through it. When the contact changes its state it permits the flow of current by closing its contacts. Can be associated with pushbuttons, pilot devices or magnetic contactors.